There are different dies or molds used in the die casting process and the selection is affected by the application and requirements. Below we’ll take a look at the different types of dies in die casting and their uses.
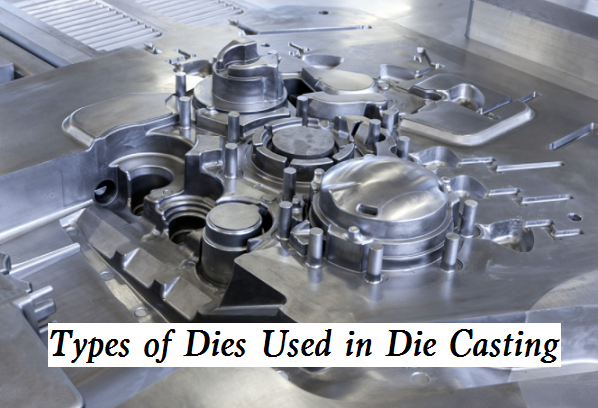
Types of Dies Used in Die Casting Process
In die casting, a metal mold or die is used to shape molten metal into a specific shape. Different types of dies are used in the die casting process depending on the application and the type of metal being cast. Here are some of the most common types of dies used in die casting and their uses:
1) Single Cavity Dies: These dies are used to cast a single part at a time and are often used for low-volume production or for prototyping.
2) Multiple Cavity Dies: These dies are used to cast multiple parts at the same time, which increases production efficiency and reduces the cost per part. They are often used for high-volume production.
3) Unit Dies: These are pre-manufactured dies that can be used to cast multiple parts with minor modifications. They are often used for producing parts with a standardized design.
4) Combination Dies: These dies have multiple cavities of different shapes and sizes, allowing for the production of different parts with the same die.
5) Hot Chamber Dies: In this type of die casting, the molten metal is injected into the die from a chamber that is attached to the die. This is typically used for metals with low melting points, such as zinc and magnesium.
6) Cold Chamber Dies: In this type of die casting, the molten metal is poured into the die from a separate furnace. This is typically used for metals with high melting points, such as aluminum and copper.
7) Semi-Solid Die: In this type of die casting, the metal is partially solidified before it is injected into the die. This allows for more complex shapes to be cast with higher dimensional accuracy.
How to Select the Die or Mold?
Selecting the right die or mold is crucial to the success of the die casting process. Here are some factors to consider when selecting a die or mold:
– The type of material being cast is a critical factor in selecting the appropriate die or mold. Different materials have different properties, such as melting point, flowability, and shrinkage rate, which must be taken into account when selecting the die or mold.
– The complexity and size of the part being cast also impact the choice of die or mold. More complex parts may require more intricate and costly dies, while larger parts require larger and more robust molds.
– The volume of production is an important factor in selecting the die or mold. For small production runs or prototyping, a single cavity die may be sufficient, while larger production runs may require multiple cavities dies to increase efficiency.
– The required tolerance and surface finish of the part must also be considered when selecting the die or mold. Tight tolerances and high surface finishes require more precise dies and molds.
– Lead Time and Cost: The lead time and cost of the die or mold are also important considerations. Custom-made dies and molds require longer lead times and are more expensive than standard dies and molds.
Die Casting Dies Material
The material used for die casting dies depends on various factors such as the type of metal being cast, the complexity of the part, the expected production volume, and the required dimensional accuracy. Generally, the following materials are commonly used for die casting dies:
– Tool Steel: This is the most commonly used material for die casting dies. It offers high strength, durability, and heat resistance, which makes it suitable for high-volume production runs. The most commonly used tool steel grades for die casting dies are H13, P20, and D2.
– H-Grade Steel: This steel is similar to tool steel but with higher levels of molybdenum and chromium, which makes it more heat-resistant and durable. It is suitable for casting high-temperature alloys such as aluminum and magnesium.
– Carbide: This material is used for die inserts and offers high wear resistance and dimensional stability. Carbide inserts can be used to reinforce the areas of the die that experience the most wear and tear.
– Ceramic: This material is used for high-temperature applications where steel or carbide may fail. Ceramic dies offer excellent heat resistance and dimensional stability, but they are more brittle and less durable than steel or carbide.
– Beryllium-Copper: This material is used for low-volume production runs and offers excellent thermal conductivity and corrosion resistance. It is not suitable for high-volume production runs due to its low durability.