Castings are metal molded parts obtained by various casting methods, that is, products with a certain shape, size, and performance are obtained by pouring, injection, suction, or other casting methods into the prepared mold, cooling, grinding, and other subsequent processing methods.
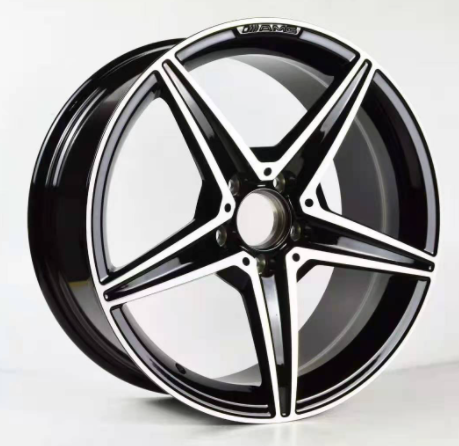
Types of Castings: Cast Iron, Cast Steel, Cast Light Alloy & Cast Composite
Castings have a long history of application. In ancient times, people used castings for coins, sacrificial vessels, weapons, tools, and some household utensils. In modern times, castings are mainly used as machine parts of the blank, some precision castings can also be used directly as parts of the machine. Castings in machinery products occupy a large proportion, such as tractors, the weight of castings accounted for about 50 to 70% of the weight of the machine, agricultural machinery accounted for 40 to 70%, machine tools, internal combustion engines and other up to 70 to 90%. Various types of castings, with the most varieties of mechanical castings, the most complex shape, the amount is also the largest, accounting for about 60% of the total output of castings. Followed by metallurgy with ingot mold and engineering with the pipe. Castings also have a close relationship with daily life. For example, often used door handles, door locks, heaters, water, and sewage pipes, iron pots, gas grates, irons, etc., are castings. Castings have a variety of classification methods, according to the different metal materials used, divided into cast steel parts, cast iron parts, cast copper parts, cast aluminum parts, cast magnesium parts, cast zinc parts, cast titanium parts, etc. Each type of casting can be further divided into different types according to its chemical composition or metallographic organization.
1. Cast iron
Cast iron has the advantages of low cost, good processability, remelting and regeneration, and saving resources and energy, so the application and development of this material will last forever. Such as research and development of cupola electric furnace duplex smelting process and equipment. Widely used molten iron desulfurization and filtration technology. Manufacturing technology of thin-walled high-strength iron castings; Manufacturing technology of Cast Iron Composites. Surface or local strengthening technology of iron castings. Complete set technology of isothermal foreign fired nodular cast iron; Special processes and equipment such as metal mold casting, metal mold sand coated casting and continuous casting is adopted.
2. Cast steel
The output of steel casting is relatively stable, while the quality, variety, and performance of steel castings and the proportion of alloy steel and special steel are continuously improved. Adopting various refining processes and technologies and developing new cast steel materials can improve the strength, toughness, and special properties of the materials.
3. Cast light-alloy
Cast light alloy will be widely used in aviation, aerospace, automobile, machinery, and other industries because of its excellent characteristics such as low density, high specific strength, and corrosion resistance. Especially in the automotive industry, in order to reduce fuel consumption and improve energy efficiency, it is a long-term development trend to replace steel and iron castings with aluminum and nickel alloy castings. Among them, it focuses on pollution-free and easy-to-operate refining technology, modification technology, grain refinement technology, and rapid detection technology in front of the furnace. In order to further improve the properties of materials and maximize the potential of materials, high-quality aluminum alloy materials, especially aluminum matrix composites, can be developed to meet the performance requirements of different working conditions; Strengthen the research of cluster alloy melting process, and continue the development and research of alloy die casting and squeeze casting process and related technologies; Improve the development and research of ferroalloy smelting equipment and related technologies and processes.
4. Cast composite
Composites will become new engineering materials in the 21st century. Cast composites will be committed to the development and research of metal matrix composites, base materials, matrix materials, and reinforced component materials, and accelerate the development and research of their applications.
Casting defects are the main cause of waste products and a serious threat to the quality of castings. Due to various reasons, there are various defects in castings. Due to the difference in solidification conditions, the types of defects are different in shape and position. For example, the solidification shrinkage of liquid metal will form shrinkage cavity and porosity; The redistribution of elements in solid and liquid phases during solidification will cause segregation. The concentration of thermal stress during cooling will cause cracks and deformation of castings. Corresponding measures shall be taken to control according to the causes and degree of occurrence, so as to eliminate or minimize it. In addition, there are many defects, such as inclusions, pores, cold shut, etc., which appear in the filling process. They are not only related to the type of alloy but also related to the specific forming process. In short, preventing, eliminating, and controlling all kinds of defects is a key issue that can not be ignored.