In metal welding, there is a technology that is like a magic wand in the hands of a magician. With a gentle wave, two pieces of cold metal can embrace each other tightly and merge into one without leaving any trace. This technology is TIG welding, a term that sounds mysterious and high-tech. Today, we will talk about TIG welding, without any complicated terms, using the simplest and most colloquial language to take you into this wonderful world of seamless metal connection.
In this blog, we will explain TIG Welding full form, discuss how to use it and its pros and cons, as well as tell the differences between MIG welding and TIG Welding. To learn more about TIG welding, contact a Diecasting-Mould representative.
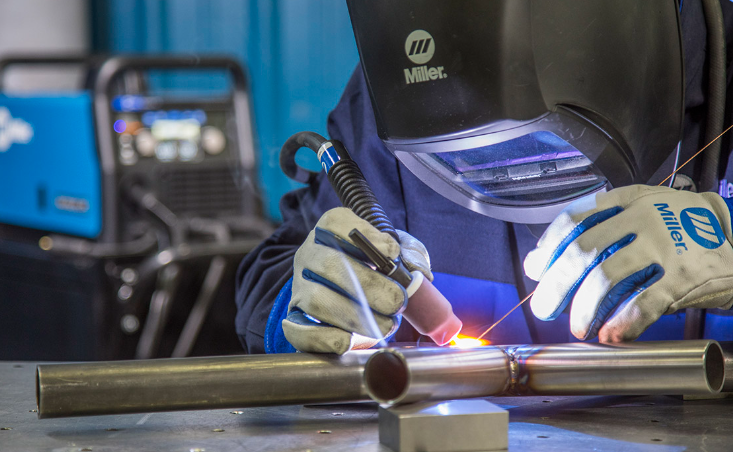
What is TIG Welding?
TIG welding, which stands for tungsten inert gas welding, also known as gas tungsten arc welding (GTAW) and Keeley Arc Welding, is an arc welding process that uses a non-consumable tungsten electrode to produce the weld. The weld area is protected from oxidation or other atmospheric contamination by an inert shielding gas (usually argon or helium), and a separate welding filler material is often used. A constant-current welding power supply produces an arc between the tip of the non-consumable tungsten electrode and the weld pool. The electrode does not melt during the process, so it must be manually sharpened as needed between welds using a stone.
How Does TIG Welding Work?
TIG welding uses a non-consumable tungsten electrode to create an electric arc between the tip of the electrode and the metals being welded. A constant current power supply is used to generate the arc. An inert gas, such as argon or helium, flows through a torch and delivers the gas to the weld area through nozzles around the tungsten electrode.
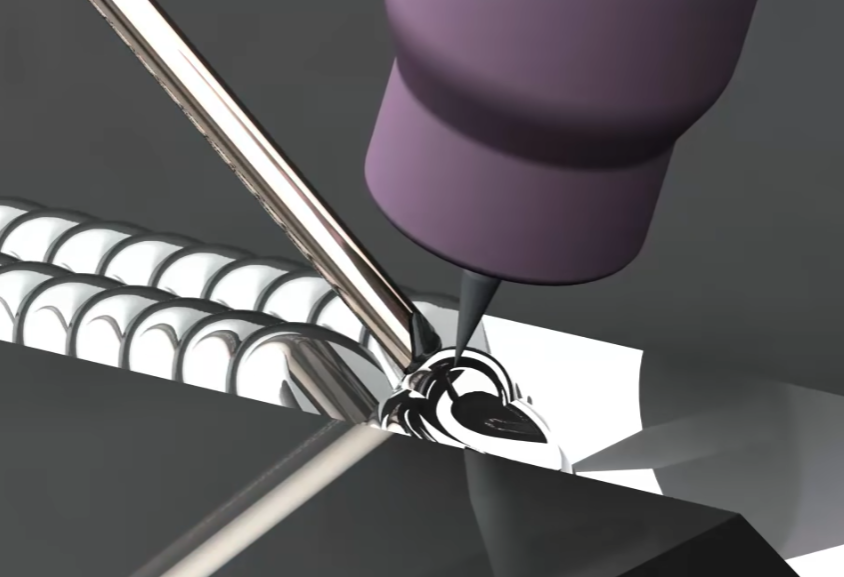
The gas shields the weld area from oxygen and other gases in the air that could react with and contaminate the hot weld metal. It also helps conduct heat and electricity. A filler rod made of the same or similar material as the base metal is often added manually to increase welding deposition rates.
When the electrode is brought close to the base metal, the constant current power supply senses the change in electrical resistance and triggers, generating an arc. Temperatures at the tip of the arc can reach over 6,000°C, melting the base and filler metals to form a weld pool.
The welder carefully controls the weld pool using the electrode like a brush, forming a joint. As the weld pool solidifies behind the arc, it fuses the materials. By precisely controlling variables like arc length, travel speed, and filler addition, high-quality welds can be produced.
Advantages and Disadvantages of TIG Welding
TIG enables high-quality precision welds but takes more skill and equipment investment compared to other techniques.
Advantages:
- – Produces high-quality, aesthetic welds suitable for precision applications
- – Provides excellent welding control with a focused arc
- – Versatile process for many metals including aluminum, stainless steel, titanium
- – Minimal filler material needed, permitting tightly controlled welds
- – Does not generate smoke or slag like other welding processes
- – Can be used to weld most any position including overhead
- – Inert gas protects the weld area from contamination
Disadvantages:
- – Requires more skilled operators compared to other welding processes
- – The learning curve can be steep for the TIG technique and setup
- – Welding costs are higher than some other welding processes
- – Process is slower than alternatives like MIG or stick welding
- – Equipment costs are higher for the power source and torch
- – Filler material must be added manually for some joints
- – Greater chance of operator error affecting weld quality
- – Proper shielding gas and flow rate are critical for good results
TIG Welding Gear
The torch, electrode, gas, power source, and work cables are core gear for TIG welding:
- – Tungsten electrode: The non-consumable electrode that arcs to the workpiece and is manually sharpened as needed. Common types are thoriated, ceriated, lanthanated, or pure tungsten.
- – Torch: Houses the electrode and gas delivery parts. Different-sized torch cups fit various electrode diameters.
- – Shielding gas: Inert gas like argon or helium that flows through the torch to shield the weld. Cylinders or machines provide the gas source.
- – Clamp: Secures the torch while welding to allow electrode manipulation with both hands. Booms help position large workpieces.
- – Filler rod: Added manually as needed for fillet or some groove welds. Made of matching filler metal.
- – Welding power source: Constant current AC or DC power supplies. More advanced units have waveforms and pulsing options.
- – Work cable: Connects the workpiece to the power source to complete the circuit. Heavy duty for welding large metal.
- – Ground clamp: Secures the work cable for proper welding current path.
- – Safety gear: Helmet, gloves, and other PPE to protect the welder from UV rays, sparks, and electric shock.
TIG Welding Torches
The tig torch is super important because you have to interact with it all the time that’s what your hands holding on with that’s how you get the job done. There are a bunch of different types and sizes but commonly, if a welder came with a tig torch, it’s probably a number 17 torch and it has the hose that goes up into the handle. This hose carries both the argon gas and electricity up through the handle to the torch.
The torch consists of several components:
- Back cap: A cover for the electrode as well as a nut to hold the collet in place. Different lengths allow fitting a full length tungsten electrode.
- Collet: A little sleeve inside the torch that fits over the tungsten, with a split and taper. Tightening the back cap squeezes the collet to hold the tungsten in place. Different sizes are used for different welds.
- Cup: Comes in different sizes for various applications. For example, numbers 5 or 6 cups are often used on aluminum jobs, while 10 or 12 cups are common for stainless steel.
- Collet body: The part where the collet fits into, squeezed by the back cap to hold everything securely.
Additional accessories include various heads for tight spaces, flexible necks for air-cooled torches, different collet bodies, and cups. Not all are necessary; only some are used regularly depending on the job.
A notable upgrade is the stubby gas lens kit, which replaces the long collet body with a short collet body that has a diffuser for more even gas flow. This allows the use of smaller cups and improves gas coverage. This upgrade is recommended for those wanting better torch performance without moving to a water-cooled system.
Water-cooled torches have three lines (argon gas plus two water lines) and are bigger, requiring a size upgrade. Many welders use air-cooled torches before upgrading to water-cooled.
TIG Welding Machines
Choosing a TIG welding machine depends on several important features:
AC vs DC output: For welding steel or stainless steel, direct current (DC) with the torch negative and work positive is typical and machines are generally lower priced. Welding aluminum requires machines with alternating current (AC) capability, where the torch and workpiece alternate between positive and negative 60 to 200 times per second to clean the oxide layer on aluminum.
Arc starting methods:
– High frequency arc starter: Sends a high voltage, high frequency electrical signal to ionize the air, allowing arc start without touching the electrode to the workpiece. This is the ideal method.
– Lift arc start: The electrode touches the workpiece and as it lifts, the machine increases current to start the arc. This works well but can wear electrodes faster on some machines.
– Scratch start: The electrode is live constantly and must be scratched or flicked to start the arc. This is the least desirable method, especially for beginners, as it wears out tungsten quickly.
Variable amperage control: A foot pedal or finger controls allow adjusting the amperage while welding, offering better heat control and efficiency.
Amperage capacity: Machines generally range from around 200 amps to 300 amps. For quarter-inch aluminum, 200 amps is usually sufficient, but thicker materials require higher amperage and additional techniques like preheating.
Pulse feature: Pulsing changes amperage between high and low during welding. It’s not essential but can be helpful for advanced techniques.
What is Tig Welding Used For?
- – Aerospace: Welding jet engine components, aircraft frames, and skin that require high strength, corrosion resistance, and transparency.
- – Automotive: Joining chassis, suspension, and powertrain parts for cars, trucks, and motorcycles. Often used on luxury and high-performance vehicles.
- – Medical: Surgery tools and implants made of titanium or stainless steel. Also dental implants, crowns, and bridges. Precision and biocompatibility are critical.
- – Art and sculpture: Artists will use TIG for assembling metal sculptures and other works given the aesthetic quality of welds.
- – Jewelry manufacturing: Brazing or welding precious metals like gold, silver, and platinum used in rings, bracelets, and other fine pieces.
- – Bicycles: Frames and components like gears and pedals are commonly TIG welded for lightweight and corrosion resistance.
- – Pipefitting: Connecting pipes, valves, and fixtures made of copper, brass, or stainless for plumbing, heating, and cooling systems.
- – Food processing equipment: Welding parts for machinery used in dairy, beverage, and other food production due to sanitary requirements.
What Types of Materials Can Be TIG Welded?
TIG is very versatile and can fuse an array of metals provided the proper gases and techniques.
- – TIG Welding Aluminum: A very popular material for TIG welding due to the process control and compatibility with aluminum. Alloys like 6061 are commonly welded.
- – TIG Welding Stainless steel: The various grades of austenitic and duplex stainless steel weld well with TIG. 304 and 316 are frequently used.
- – TIG Welding Titanium: An important structural metal that requires an inert shielding gas. Both commercial purity and alpha-beta alloy titanium.
- – TIG Welding Magnesium: When used with pure argon gas, TIG can join this light but flammable metal. Alloys like AZ31B.
- – TIG Welding Copper: Both copper alloys and pure copper are amenable to TIG. Good for piping, tubing, and electronics applications.
- – TIG Welding Nickel alloys: Corrosion-resistant alloys containing nickel perform well with TIG, such as Monel and Hastelloy.
- – TIG Welding Zinc: Galvanized sheet metal and die-cast zinc components can be spot welded or repaired.
- – TIG Welding Platinum: Precious metal TIG welding used for industrial process parts and jewelry.
- – TIG Welding Steel (carbon and low-alloy): Mild steels like A36 can be welded though higher alloy steels are more common.
What Gas is Used For TIG Welding?
In TIG welding, the molten metal is protected by a shielding gas, which gas usually argon and sometimes helium or other gases keeps the molten metal from reacting with oxygen and water vapor in the atmosphere. This shielding gas is stored in high-pressure cylinders like these, the pressure is reduced to a usable level by a device called a regulator. The shielding gas flows through a hose and comes out right at the point of the welds.
How To Set & Do TIG Welding Properly?
Now, let’s give our experiences on TIG welding clear settings to form the foundation of quality TIG welding:
Setup:
- Start with clean materials. Grind off any mill scale on steel, then wipe the surface with acetone or denatured alcohol to remove grease or oils. Also clean filler metal by pulling a rag soaked in acetone across it.
- Prepare the torch by grinding the tungsten electrode to a nice point. A consistent point shape is less critical for beginners; a sharp point is sufficient. Insert the tungsten so it protrudes about 1/4 inch beyond the cup or gas lens.
- Set machine amperage based on material thickness. A good rule of thumb is one amp per 0.001 inch of thickness. For 1/8 inch steel plate, set around 110 amps without a foot pedal or 130 amps with a foot pedal.
Technique:
- Focus on arc length:
Maintain about a 1/8 inch gap between the tungsten and the workpiece. Practice dry runs moving the torch steadily in a straight line before turning the machine on. Adjust arc length to keep it consistent; too long causes unstable arc and poor puddle control. - Maintain proper torch angle:
For fillet joints, hold the torch at approximately 45 degrees to each surface, then tilt torch about 10 degrees in the direction of travel, pushing the puddle forward. For flat work, hold the torch perpendicular to the workpiece with a slight forward tilt, and keep the angle consistent to avoid extending the arc and disrupting the puddle. - Control movement speed:
Move the torch at a steady pace to maintain a consistent puddle width and watch the puddle size and adjust speed to keep it uniform. - Add filler metal correctly:
Wait for a puddle to form before adding filler, and dab the filler rod into the leading edge of the puddle. Avoid melting the filler in mid-air by maintaining correct arc length and torch angle, but keep filler addition smooth and continuous as you move.
TIG Welding AC or DC, When To Use Each Type?
TIG welding works by melting the base metal and that is the metal that makes up the two pieces that are to be joined. The heat is generated by an electric arc that forms between the base metal and the tungsten electrode. Based on the electric arc, TIG Welding can be divied into DC (full form Direct Current) and AC (full form Alternating Current)
DC TIG Welding
For most metals, the current is DC, full form direct current. DC is like the current flowing from a car battery, one wire is always the negative, and one is always the positive. In DC TIG welding, the electrode is usually negative and the workpiece is positive. The term of DECN is used for this, indicating that the current is DC, the electrode is negative. This is also called Straight Polarity. The DCEN is a more descriptive term. DCEN puts most of the heat on the workpiece, and it’s the most common setup.
AC Tig Welding
When welding aluminum, however, AC is used. In AC, the positive and negative voltages switch back and forth between the electrode and the workpiece; this puts more heat on the electrode, but it has a cleaning effect on the workpiece. You see, aluminum forms oxides that float to the top of the weld pool and prevent a good weld. AC current helps control these oxides.
MIG vs TIG Welding, What is the Difference Between Them?
Is TIG welding the only way to go for metal welding? No way! There is another welding process that is also widely used by serious hobbyists or especially automotive enthusiasts wanting to fabricate their own parts, this is the MIG welding. Should I choose TIG Welding or MIG Welding? This question may confuse some beginners. Actually, for a lot of projects, you could really use either process, however, there are still some differences that make them distinct from each other and applicable individually to certain situations.
Work Principle
TIG Welding stands for Tungsten Inert Gas or Gas Tungsten Arc Welding, uses a tungsten electrode that does not melt. Electricity flows between the tungsten electrode and the workpiece, creating a hot electrical arc to melt metal and join parts. It requires shielding gas to protect the weld area from atmospheric contamination. The additional filler metal is manually added with the other hand, so it is a manual process with a learning curve.
TIG Welding stands for Metal Inert Gas, the electrode and filler wire are the same, fed continuously by a motorized mechanism. It uses shielding gas to protect the weld from the atmosphere, semi-automatic process maintaining the arc length automatically.
Material Compatibility
TIG and MIG welding both can weld a wide variety of materials. TIG has advantages when welding aluminum or magnesium due to AC output capability. MIG welding requires different shielding gases and torches for different materials (steel, aluminum, stainless steel). Switching materials on MIG requires equipment changes; TIG only needs filler wire and gas cup changes.
Weld Length and Speed
MIG welding is faster for long welds, saving significant time. TIG welding is slower due to its manual nature but can still handle long welds efficiently (e.g., 40-foot aluminum TIG welds on trailers). MIG is preferred for speed in long welds.
Material Preparation
MIG welding tolerates less clean material; quick wipe or mill scale grind is often enough. TIG welding requires meticulously clean material for quality welds. MIG is better if less prep time is desired.
Applicability
For many projects, either process could be used. For example, in a budget go-kart build, MIG welding was used for speed, but TIG could have been used just as well. There is no one right process for every project, but sometimes one is better than the other.
Weld Appearance
MIG welds can look good but generally cannot match the aesthetic quality of TIG welds. TIG welding offers greater control and superior appearance.
Ease of Use
MIG welding is faster to learn for most people, while TIG welding takes more time but can be learned faster with a systematic approach. So take structured courses can accelerate your TIG welding learning and improve practice efficiency.
Welding Position and Accessibility
TIG welding is easier on a bench setup. MIG welding is easier when welding in awkward positions or confined spaces such as roll cages or under cars. So you should consider the typical welding positions when choosing between them.
TIG vs Laser Welding, What is the Difference Between Them?
The key differences are that the laser uses a focused non-contact beam vs TIG’s electric arc, and the laser typically provides faster, more precise, and higher-powered welding capabilities.
- Electrode: TIG uses a non-consumable tungsten electrode to create an arc, while laser welding uses a focused laser beam.
- Heat Source: The electric arc heat source in TIG welding is concentrated but not as precise as the laser beam, which can be tightly focused.
- Shielding Gas: TIG requires an inert shielding gas like argon to protect the weld area. Lasers typically do not need external shielding gas.
- Filler Material: TIG often uses a separate filler rod added manually, while laser welding can join materials without filler.
- Welding Speed: Laser welding is generally much faster than TIG, which must be moved along the joint manually.
- Joint Preparation: TIG typically requires a beveled joint for proper penetration, while a laser can often fusion weld without edge preparation.
- Material Depth: Laser energy can be absorbed to weld deeper into thick materials, while TIG is better for thinner gauges.
- Precision: The laser beam enables highly precise welds down to a few microns in width and depth. TIG is less precise.
- Cost: Laser systems are more expensive initially but can have higher welding throughput rates than TIG.