The famous line from Jin Cao Pi’s “Yong Ye Fu”, which depicts the scene of ancient China’s smelting and die casting production, is “smelting stone as a tool and setting up a thousand furnaces together”. In ancient metal processing techniques in China, die casting played a prominent role and had a wide social impact. Idioms such as “model”, “pottery”, “melting and die casting”, and “conforming” continued to use the terminology of the die casting industry. The working people have created traditional die casting techniques with Chinese national characteristics through long-term production practices passed down from generation to generation. Among them, clay molds, iron molds, and investment die casting are the most important, known as the three major ancient die casting techniques.
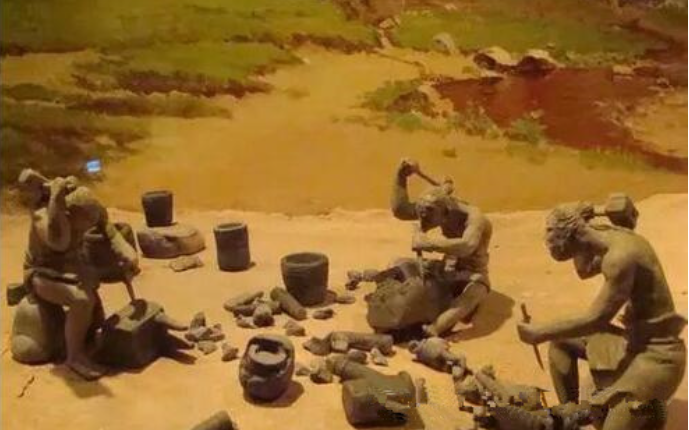
Clay mold die casting
The initial die casting technique was the use of stone molds. Due to the difficulty in processing stone and its inability to withstand high temperatures, with the development of the pottery industry, clay molds were used instead. For over three thousand years before modern sand die casting, clay mold die casting had always been one of the most important die casting methods.
Brief introduction
The die casting industry occupies a prominent position in the metal processing technology of ancient China and has had a huge social impact. The vocabulary of “model”, “molten”, “clay model” and other words that we often use in our daily lives today comes from the terminology of the ancient foundry industry. In ancient China, the laboring people created two traditional die casting techniques, the pottery model method and the lost wax method, in their long-term production practice.
The process of clay mold die casting
1. Mold making
Carve clay molds according to the prototype of the object using clay;
2. Overturning
Beat the evenly mixed soil into flat mud sheets, press them on the outside of the mud mold, and press them firmly to make the patterns on the mud mold imprint on the mud sheets. After the mud pieces are half dried, cut them into several pieces with a knife according to the ears, feet, toes, bottom, edges, corners, or symmetry points of the object. Then, make triangular mortise and tenon joints for the adjacent two mud pieces, and air dry them or bake them over a low heat to trim and repair the patterns on the inner surface of the molds. This becomes the outer mold used for die casting;
3. Internal standard
Scrape a thin layer of mud mold that has been used to make the outer mold while it is wet, and then dry it over heat to make the inner mold. The thickness scraped off is the thickness of the cast copper ware;
4. Compliance
Invert the inner mold onto the base, and then place the outer mold block around the inner mold. After the outer model is closed, there is a closed model cover on it, and at least one pouring hole is left on the model cover;
5. Die casting
Inject molten bronze solution along the pouring hole, wait for the copper liquid to cool, break the outer mold, remove the inner mold, and take out the cast copper ware. After polishing and trimming, a beautiful bronze ware is completed.
Split die casting method as the basic process principle
When making complex shaped bronze vessels, the ancients also adopted the die casting method as the basic process principle to obtain complex vessel shapes. Alternatively, first cast the body of the vessel, and then pour accessories (such as animal heads, pillars, etc.) into the upper mold; Alternatively, the accessories (such as the ears and feet of the tripod) can be cast first, and then the boundary can be cast into one during the pouring of the vessel body. The famous Four Sheep Zun (unearthed in Ningxiang, Hunan) was cast using the die casting method.
Split die casting
When making complex shaped bronze vessels, the ancients also adopted the die casting method as the basic process principle to obtain complex vessel shapes. Alternatively, first cast the body of the vessel, and then pour accessories (such as animal heads, pillars, etc.) into the upper mold; Alternatively, the accessories (such as the ears and feet of the tripod) can be cast first, and then the boundary can be cast into one during the pouring of the vessel body. The famous Four Sheep Zun (unearthed in Ningxiang, Hunan) was cast using the die casting method.
Originating from the early Shang Dynasty
The origin of this method can be traced back to the Erligang period (early Shang Dynasty) and the Xiaotun period (late Shang Dynasty), and the basic form has already been roughly established.
Spring and Autumn period became the mainstream of separate die casting
Die casting accessories first and then die casting the body became the mainstream of the separate die casting method. Most of the Yi wares in Xinzheng and the tripods and pots in the Warring States period were cast in this way. The successful application of simple process principles to solve complex process problems, using simplicity to resist complexity, and demonstrating unique craftsmanship in ordinary labor is an outstanding creation of ancient working people, and also a key to understanding the die casting technology of Shang and Zhou bronze ware. It is not realistic to mistake complex objects such as the Four Sheep Buddha for lost wax die castings, and it is even more wrong to make Shang and Zhou bronze vessels mysterious and insurmountable.
Stacking die casting
Another outstanding achievement of ancient Chinese clay mold die casting is the early emergence and widespread application of the stacking die casting method. The so-called stacked die casting refers to the assembly of many mold blocks or pairs of mold pieces, which are poured through a common runner, resulting in dozens or even hundreds of die castings at once. The cost is relatively low and is still widely used today. The earliest overlapping die casting in China is Qi Dao coin in the Warring States period, which is made of copper mold boxes, with high symmetry and interchangeability. Each two pieces are combined into one layer, which is made of multiple layers. In the Han Dynasty, it was widely used in the production of coins, chariots, and horses. In recent years, in provinces such as Shaanxi, Henan, and Shandong, this type of die casting and baking kiln has been unearthed. Especially at the Han Dynasty smelting and die casting site in Xizhaoxian Village, Wen County, Henan Province, over 500 sets of stacked die casting molds of 16 types and 36 specifications were excavated, providing valuable physical information for us to understand this process. They are cleverly structured and finely crafted, with an inner gate thickness of only 2 to 3.5 millimeters for easy cleaning of die castings. The die castings cast using these molds have a surface finish of five levels (a total of fourteen levels). The metal yield can reach 90%, and the technological level is close to that of similar methods used in modern times in Foshan, Guangdong.
Fan die casting technology has a long history in China
Since the late Neolithic period, China has entered the era of Chalcolithic. The early copper artifacts unearthed in Tangshan and other places in Hebei Province, including those formed by forging and melting, indicate that the die casting technology has a long history in China and has developed very early.
There are many records in ancient literature about Kunwu (a tribe from the Xia Dynasty, residing in the north of present-day Duyang City, Henan) making pottery and die casting copper, as well as legends about Yu die casting the Nine Cauldrons. From recent archaeological excavations, it can be seen that the Xia Dynasty was able to melt and cast bronze. The initial mold used stone molds. Due to the difficulty in processing stone and its inability to withstand high temperatures, on the basis of advanced pottery making techniques, clay molds were quickly used. For over 3000 years, before the rise of modern machine manufacturing and the use of sand mold die casting, it had always been the main die casting method.
In the early Shang Dynasty, the Erlitou site in Yanshi, Henan Province was used as a symbol, and small production tools such as copper adzes and chisels were already cast using clay molds, as well as daily utensils such as copper bells and bronze nobles. Later, with Erligang in Zhengzhou as a symbol, the bronze smelting and die casting industry began to develop. The two large cauldrons unearthed in Zhangzhai, Zhengzhou, weighing 64.25 kilograms and 82.25 kilograms respectively, indicate that the copper die casting technology in the mid Shang Dynasty had reached a considerable level, from single sided and double sided mold die casting to the ability to use multiple molds and cores to form composite molds to cast large die castings weighing over a hundred kilograms.
After Pan Geng moved to Yin, the bronze smelting and die casting technology reached its peak, marked by the Yin Ruins in Xiaotun, Anyang. The tens of thousands of Shang and Zhou bronze artifacts unearthed and passed down are not only important historical relics, but also the crystallization of the wisdom and talent of the smelting slaves. Their academic, artistic value, and technical level are universally recognized.
In order to obtain bronze die castings with highly complex shapes and exquisite patterns, ancient smelting and die casting craftsmen adopted a series of important technological measures.
For example, in the preparation of molding materials, local materials are selected, and pure sand and mud with high fire resistance are selected for refining. The surface mud used for the mold surface is washed with water to obtain extremely fine and pure clay (clay). This clay has good plasticity and strength, and can achieve high clarity and accuracy when flipping the mold. The back mud is made of relatively coarse mud or mixed with sand and plant matter to reduce the consumption of clarified mud and increase the permeability of the die casting mold. All mud materials must undergo long-term drying in the shade, repeated throwing and sweeping to ensure that they are highly evenly cooked and do not crack when shaped or dry.
Mature craftsmanship
For the drying, roasting, and assembly of the mold core, uniform wall thickness to achieve simultaneous solidification, and preheating the mold to ensure smooth pouring, a complete set of mature processes have been explored during the Shang and Zhou dynasties, which not only laid a technical foundation for future generations of clay mold casting, but also for metal mold and investment casting.
However, under the social condition that the exploiting class possesses the Means of production and masters the state machinery, the scientific and technological achievements of the working people are always seized by the rulers, which are used to suppress and deceive the people and meet their decadent and extravagant life needs. Among the bronze artifacts of the Shang and Zhou dynasties, the four categories of ritual, music, military, and chariot accounted for the vast majority, with few production tools. Many Ming artifacts (accompanying burial objects) were buried underground after being cast. This situation greatly hinders the development of social productivity. As a result, for more than a thousand years, clay mold casting basically remained in the stage of one-time casting, and only in the Spring and Autumn period did copper tools (picks) be cast with multiple types (semi permanent clay molds).
The use of clay molds to cast large and oversized castings has undergone significant development since the Tang and Song dynasties. The iron lion of the Five Dynasties in Cangzhou, the iron tower of the Northern Song Dynasty in Dangyang, and the bell of the Ming Dynasty in Big Bell Temple in Beijing are all world-famous giant castings. Volume 8 of Song Yingxing’s “Heavenly Creations” describes two ways to pour large pieces: one is to pour them one by one with multiple row furnaces (clocks within a kilo), and the other is to pour them with multiple furnace slots (ten thousand bells). Under the technological conditions of ancient handicraft production, this should be said to be a clever and skillful process that requires skilled skills and good organization and coordination. Even in modern times, it is not an easy task to successfully pour 30 to 40 tons of large castings.
China had clay model casting in the early Shang Dynasty, and reached its peak in the middle of the Shang Dynasty. In this way, ancient craftsmen created unprecedented treasures like Simuwu Ding and Four-goat Square Zun.
Mature craftsmanship
For the drying, roasting, and assembly of the mold core, uniform wall thickness to achieve simultaneous solidification, and preheating the mold to ensure smooth pouring, a complete set of mature processes have been explored during the Shang and Zhou dynasties, which not only laid a technical foundation for future generations of clay mold die casting, but also for metal mold and investment die casting.
However, under the social condition that the exploiting class possesses the Means of production and masters the state machinery, the scientific and technological achievements of the working people are always seized by the rulers, which are used to suppress and deceive the people and meet their decadent and extravagant life needs. Among the bronze artifacts of the Shang and Zhou dynasties, the four categories of ritual, music, military, and chariot accounted for the vast majority, with few production tools. Many Ming artifacts (accompanying burial objects) were buried underground after being cast. This situation greatly hinders the development of social productivity. As a result, for more than a thousand years, clay mold die casting basically remained in the stage of one-time die casting, and only in the Spring and Autumn period did copper tools (picks) be cast with multiple types (semi permanent clay molds).
The use of clay molds to cast large and oversized die castings has undergone significant development since the Tang and Song dynasties. The iron lion of the Five Dynasties in Cangzhou, the iron tower of the Northern Song Dynasty in Dangyang, and the bell of the Ming Dynasty in Big Bell Temple in Beijing are all world-famous giant die castings. Volume 8 of Song Yingxing’s “Heavenly Creations” describes two ways to pour large pieces: one is to pour them one by one with multiple row furnaces (clocks within a kilo), and the other is to pour them with multiple furnace slots (ten thousand bells). Under the technological conditions of ancient handicraft production, this should be said to be a clever and skillful process that requires skilled skills and good organization and coordination. Even in modern times, it is not an easy task to successfully pour 30 to 40 tons of large die castings.
China had clay model die casting in the early Shang Dynasty, and reached its peak in the middle of the Shang Dynasty. In this way, ancient craftsmen created unprecedented treasures like Simuwu Ding and Four-goat Square Zun.
Metal die casting
Brief introduction
Metal die casting is the process of melting metal into a liquid that meets certain requirements and pouring it into the mold. After cooling, solidification, and cleaning treatment, a die casting with predetermined shape, size, and performance is obtained. die casting rough embryos, due to their near formation, achieve the goal of avoiding mechanical processing or minimal processing, reducing costs and to some extent reducing time. die casting is one of the basic processes in modern mechanical manufacturing industry.
Classification
The types and modeling methods of metal die casting are customarily divided into:
① Ordinary sand mold die casting includes three types: wet sand mold, dry sand mold, and chemically hardened sand mold.
② Special die casting can be divided into two types based on the molding materials: special die casting with natural mineral sand and gravel as the main molding material (such as investment die casting, mud die casting, shell die casting in die casting workshops, negative pressure die casting, full mold die casting, ceramic mold die casting, etc.) and special die casting with metal as the main molding material (such as metal mold die casting, pressure die casting, continuous die casting, low-pressure die casting, centrifugal die casting, etc.).
Sand die casting process
Metal die casting processes typically include:
① Preparation of die casting molds (containers that turn liquid metals into solid die castings), which can be divided into sand molds, metal molds, ceramic molds, mud molds, graphite molds, etc. according to the materials used, and can be divided into disposable molds, semi permanent molds, and permanent molds according to the number of uses. The quality of die casting mold preparation is the main factor affecting the quality of die castings;
② The melting and pouring of cast metals, including cast iron, cast steel, and cast non-ferrous alloys;
③ die casting treatment and inspection, including the removal of foreign objects on the core and surface of the die casting, removal of die casting and riser, scraping and grinding of burrs and burrs, as well as heat treatment, shaping, rust prevention treatment, and rough machining.
History
In ancient times, China, India, Babylon, Egypt, Greece, and Rome had already cast weapons, sacrificial vessels, artworks, and household utensils. Early die castings were made of gold, silver, copper, and their alloys. The Bronze Age is a glorious page in the history of human civilization; In the future, cast iron parts appeared again. Iron die castings were widely used in China as early as the Warring States period, with a long technological tradition. The attached figure is a diagram of the die casting kettle in “Tiangong Kaiwu” (see metallurgical history). Metal die casting
Metallurgy and die casting are complementary technological processes, and the term “smelting and die casting” in ancient China reflects this fact. Although foundry technology has developed into a relatively independent branch of mechanical manufacturing technology in later times, it is still inseparable from metallurgical technology.
① Cast iron has a long history, but its development speed is slow. It was not until 1722 that Leomir created the “cupola” and began studying the microstructure and fracture surface of cast iron under a microscope that the situation changed. In 1734, Svedenberg’s “De ferro” was published, providing a preliminary theoretical understanding of cast iron technology. From 1765 to 1785, due to the emergence of the Steam engine, cast iron was widely used in machine manufacturing since the 1860s, and the transport sector also used cast iron rails. In 1788, a total length of 60 km of cast iron pipes for water delivery was produced for the Paris Waterworks. The increasing demand for cast iron has promoted the technological progress and theoretical research work of cast iron.
The die casting properties of metals include:
① Liquidity, the ability of liquid metal to fill the mold;
② Shrinkage tendency, large volume shrinkage from liquid to solid, prone to defects such as shrinkage cavities, and large linear size shrinkage, affecting the final dimensional accuracy of die castings;
③ Hot cracking tendency, some metals and alloys are prone to cracking and segregation during the die casting process (see solidification of metals).
Investment die casting
History
The Lost-wax die casting in China originated in the Spring and Autumn period at the latest. The bronze ban of the Spring and Autumn Period unearthed from the No. 2 Chu Tomb in Xiasi, Xichuan, Henan Province, is the earliest Lost-wax die casting die casting known so far. This bronze ban is adorned with carved cloud patterns on all four sides and sides, with twelve standing beasts around it, and a total of ten standing beast feet underneath. The complexity and variety of openwork patterns, gorgeous and solemn appearance, reflect that China’s Lost-wax die casting has been relatively mature in the middle of the Spring and Autumn Period. After the Warring States Period and the Qin and Han Dynasties, the Lost-wax die casting became more popular, especially during the Sui and Tang Dynasties to the Ming and Qing Dynasties, the Lost-wax die casting was mostly used to cast bronze wares.
The Lost-wax die casting is generally used to make small die castings
The copper ware cast using this method has no mold marks or gasket marks, and it is better to use it to cast hollow objects. The traditional investment die casting technology in China has a significant impact on the world’s metallurgical development. The investment precision die casting of modern industry is developed from the traditional Lost-wax die casting. Although there are significant differences in wax materials, molding materials, and process methods used, their process principles are consistent. In the mid-1940s, when Austin, an American engineer, founded the modern investment die casting technology named after him, he got inspiration from the Chinese traditional Lost-wax die casting. In 1955, Austin Laboratory submitted a petition for the first Lost-wax die casting, and Japanese scholar Lu Caiyi male objected to the fact that Lost-wax die casting was used in the history of China and History of Japan, and finally won the lawsuit.
Lost-wax die casting
Investment die casting, also known as “wax loss die casting”, usually refers to a die casting method where a pattern is made of a fusible material, and several layers of refractory material are coated on the surface of the pattern to form a mold shell. The mold is then melted and discharged from the mold shell to obtain a mold without a parting surface. After high-temperature roasting, the mold can be filled with sand and poured. Due to the widespread use of waxy materials for manufacturing, investment die casting is often referred to as “wax loss die casting”.
The types of alloys that can be produced by investment die casting include carbon steel, alloy steel, heat-resistant alloy, stainless steel, precision alloy, permanent magnet alloy, bearing alloy, copper alloy, aluminum alloy, titanium alloy and nodular cast iron.
The shape of investment die castings is generally relatively complex, with the minimum diameter of holes that can be cast on the die castings reaching 0.5mm and the minimum wall thickness of the die castings being 0.3mm. In production, some components that were originally composed of several parts can be designed as a whole by changing the structure of the parts and directly cast by investment die casting to save processing time and metal material consumption, making the structure of the parts more reasonable.
The weight of investment die castings is mostly in the range of tens of newtons (i.e. tens of grams to several kilograms). It is more difficult to produce heavy die castings using investment die casting method, but currently the weight of producing large investment die castings has reached around 800 newtons.
The investment die casting process is complex and difficult to control, and the materials used and consumed are expensive. Therefore, it is suitable for producing small parts with complex shapes, high precision requirements, or difficult to process, such as turbine engine blades.
Manufacturing of investment molds
The first process of investment die casting production is the manufacturing of investment molds, which are used to form a model of a refractory shell with a medium cavity. Therefore, in order to obtain die castings with high dimensional accuracy and surface finish, the investment mold itself should have high dimensional accuracy and surface finish. In addition, the performance of the mold itself should also be as simple and feasible as possible for subsequent processes such as shell making. In order to obtain the high-quality investment mold required above, in addition to having good molding (molds for pressing investment molds), it is also necessary to choose appropriate mold making materials (referred to as mold materials) and reasonable mold making processes.
Mold material
The performance of mold making materials should not only ensure the convenient production of investment molds with precise dimensions, high surface finish, good strength, and light weight, but also create conditions for the manufacturing of mold shells and obtaining good die castings. The mold material is generally prepared with wax, natural resin, and plastic (synthetic resin). Wax based molds, which are mainly prepared with wax, have a lower melting point of 60-70 ℃; Any mold material mainly prepared with natural resin is called resin based mold material, with a slightly higher melting point of about 70-120 ℃.
Preparation and recycling of mold materials
1) Preparation of mold materials
The purpose of preparing the mold material is to mix various raw materials that make up the mold material into a uniform whole and ensure that the state of the mold material meets the requirements of pressing and melting.
During preparation, heating is mainly used to melt and mix various raw materials into a whole. Then, under cooling, the mold material is vigorously stirred to create a paste state for pressing molten molds. Sometimes there are situations where the mold material is melted into liquid and directly poured into the mold.
2) Recycling of mold materials.
When using resin based molds, due to the high quality requirements for investment molds, new materials are mostly used to prepare molds for pressing investment molds of die castings. The recycled mold material after demolding is used to make the melt mold for the gating and riser system after remelting and filtering.
When using wax based molds, the mold material obtained after demolding can be recycled and used to manufacture new molds. However, during cyclic use, the performance of the mold material will deteriorate, with increased brittleness, increased ash content, decreased fluidity, increased shrinkage rate, and a color change from white to brown. These are mainly related to the deterioration of stearic acid in the mold material. Therefore, in order to restore the original performance of the old mold material as much as possible, it is necessary to remove soap salts from the old mold material. Common methods include hydrochloric acid (sulfuric acid) treatment, activated clay treatment, and electrolytic recovery.
Manufacturing of investment molds and modules
1) Manufacturing of investment molds
In production, pressure is mostly used to press the paste mold material into the mold to manufacture the melt mold. Before pressing the mold, a thin layer of parting agent needs to be applied to the surface of the mold to remove the mold from the mold. When pressing wax based pattern material, the parting agent can be engine oil, Turpentine, etc; When pressing resin based molds, a mixture of sesame oil and alcohol or silicone oil is commonly used as a parting agent. The thinner the parting agent layer, the better, so that the mold can better replicate the pressed surface and improve the surface smoothness of the mold. There are three methods for pressing molten molds, namely plunger pressure method, air pressure method, and piston pressure method.
2) Assembly of Molds
The assembly of investment molds is the combination of the investment molds that form the die casting and the investment molds that form the gating and riser system. There are two main methods:
1. Welding method uses a thin piece of soldering iron to melt the connection parts of the fusion mold, so that the fusion mold is welded together. This method is more common.
2. When producing small investment die castings in large quantities, the mechanical assembly method has been widely used in foreign countries to combine modules. The use of this type of module can greatly improve the module combination and efficiency, and the working conditions have also been improved.
Manufacturing of molded shells
The mold of investment die casting can be divided into two types: solid body and multi-layer shell, and currently the commonly used type is multi shell.
After immersing the module with refractory coating, sprinkle it with material like refractory material, and then dry and harden it multiple times until the refractory coating layer reaches the required thickness. This forms a multi-layer shell on the module, which is usually left for a period of time to fully harden, and then melt off the module, resulting in a multi-layer shell.
Some multi-layer shells need to be boxed and filled with sand; Some do not need to be poured directly after roasting.
When the mold is lost during melting, the shell will be subjected to pressure from the increasing volume of the molten mold material; During roasting and pouring, various parts of the mold shell will experience mutual restraint and uneven expansion and contraction, therefore, the metal may also undergo high-temperature chemical reactions with the mold shell material. So there are certain performance requirements for the shell, such as small expansion and contraction rates; High mechanical strength, thermal shock resistance, fire resistance, and chemical stability at high temperatures; The mold shell should also have a certain degree of breathability, so that the gas inside the mold shell can smoothly escape during pouring. These are all related to the refractory materials, adhesives, and processes used in the manufacturing of the shell.
Materials used for manufacturing mold shells
The materials used for manufacturing mold shells can be divided into two types. One type is used to directly form the mold shell, such as refractory materials, adhesives, etc; Another type is the materials used to obtain high-quality shells, simplify operations, and improve processes, such as fluxes, hardeners, surfactants, etc.
Refractory materials
At present, the refractories used in investment die casting are mainly quartz and corundum, as well as Aluminium silicate refractories, such as refractory clay, bauxite, coke stone, etc. Sometimes zircon, magnesia (MgO), etc. are also used.
binder
The most commonly used binder in investment die casting is silicate colloidal solution (referred to as silicate sol), such as ethyl silicate hydrolysis solution, water glass, and silica sol. The substances that make up them are mainly silicic acid (H2SiO3) and solvents, sometimes with stabilizers such as NaOH in silica sol.
Ethyl silicate hydrolysate is the earliest and most commonly used binder in silicic acid sol-gel die casting obtained by hydrolysis of ethyl silicate; The water glass shell mold is prone to deformation and cracking, and the die castings cast with it have poor dimensional accuracy and surface finish. However, in China, when producing carbon steel die castings with higher precision requirements and non-ferrous alloy die castings with lower melting points, water glass is still widely used in production; The stability of silica sol is good, and it can be stored for a long time. When making mold shells, there is no need for specialized hardeners, but silica sol has a slightly poor wetting effect on the mold. The mold shell hardening process is a drying process that takes a long time.
Shell making process
The main processes and processes in the shell making process are:
1) Degreasing and degreasing of modules
When using wax based mold materials to make investment molds, in order to improve the ability of the coating to wet the surface of the module, it is necessary to remove the oil stains on the surface of the module.
2) Apply coating and sand on the module
Before applying the coating, the coating should be stirred evenly to minimize the precipitation of refractory materials in the coating barrel. The viscosity or specific gravity of the coating should be adjusted to ensure that the coating can fill and wet the mold well. When applying the coating, the module should be immersed in the coating and shaken up and down to ensure that the coating can wet the mold well and evenly cover the surface of the module. After the coating is applied, the noise can be scattered.
3) Shell drying and hardening
After each layer of shell is coated, it should be dried and hardened to make the binder in the coating change from sol to gel and gel, and connect the refractory materials together.
4) Molten loss in self formed shell
After the shell is completely hardened, the module needs to be melted away from the shell. As the module is commonly made of wax based materials, this process is also called dewaxing. According to different heating methods, there are many methods for dewaxing, with the most commonly used being the hot water method and the same pressure steam method.
5) Calcined shell
If molding (sand filling) pouring is required, before roasting, the demolded shell should be buried in the sand particles inside the box, and then loaded into the furnace for roasting. If the shell has high high-temperature strength and does not require molding and pouring, the demolded shell can be directly sent into the furnace for roasting. Gradually increase the furnace temperature during roasting, heat the shell to 800-1000 ℃, and hold it for a period of time before pouring can proceed.
Pouring of investment die castings
The commonly used pouring methods for investment die casting include:
1) There are several methods for thermal gravity die casting.
This is the most widely used form of pouring, where the mold shell is removed from the roasting furnace and poured at high temperatures. At this point, the metal cools slowly in the mold shell and can fill the mold with high fluidity, so the die casting can replicate the shape of the mold cavity well and improve the accuracy of the die casting. However, slow cooling of the die casting in the hot mold can cause coarsening of the grains, which reduces the mechanical properties of the die casting. When pouring carbon steel die castings, the surface of the die castings with slower cooling is also prone to oxidation and decarburization, thereby reducing the surface hardness, smoothness, and dimensional accuracy of the die castings.
2) Vacuum suction pouring
Place the mold shell in a vacuum pouring box and suck out the gas in the cavity through the small pores in the mold shell, allowing liquid metal to better fill the cavity, replicate the shape of the cavity, improve die casting accuracy, and prevent defects such as air holes and insufficient pouring. This method has been applied abroad.
3) Crystallization under pressure
Place the mold shell in the pressure tank for pouring. After completion, immediately close the pressure tank and inject high-pressure air or inert gas into the tank to solidify the die casting under pressure, in order to increase the density of the die casting. The maximum pressure abroad has reached 150atm.
4) Directional crystallization (directional solidification)
Some investment die castings, such as turbine blades, magnetic steel, etc., can improve their working performance significantly if their crystalline structure is columnar crystals arranged in a certain direction. Therefore, the directional crystallization technology of investment die casting is rapidly developing.