Wire terminals must be coated to prevent corrosion and degradation of electrical characteristics, as is well knowledge. While it’s possible to combine gold with silver, it’s impossible to combine it with silver. The primary focus of this guide is to provide an introduction to terminal electroplating’s fundamentals, and items that need to be considered when designing precious metal electroplating.
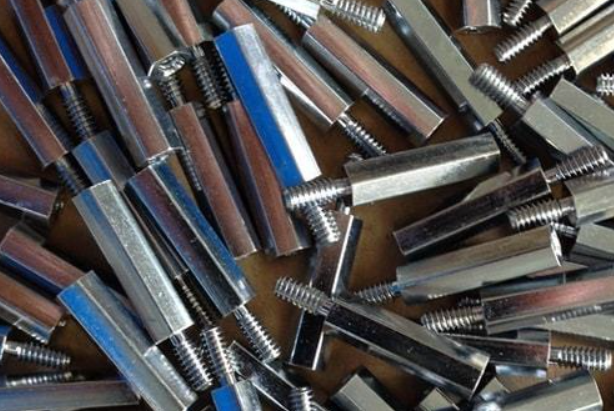
What does the word “terminal plating” mean?
For the purpose of electrochemically forming metal atoms adherent to an electrode surface, electroplating refers to the process in which simple or complex metal ions are discharged and reduced on the surface of solids (conductors or semiconductors).
Terminal electroplating’s intended use
Changing the surface qualities of a solid using electroplating may alter its look while also improving its corrosion and wear resistant as well as hardness, and it can also offer particular optical and electrical as well as magnetic, thermal, and other properties to the surface.
Terminal electroplating: a brief introduction
Electroplating is the most common surface treatment for electronic connections and terminals. To protect the terminal reed substrate from corrosion, and to enhance the performance of the terminal surface, create and maintain the contact interface between terminals, particularly the film control. Making metal to metal contact simpler is another way of saying this.
Most reeds are constructed of copper alloy, which is susceptible to oxidation, vulcanization, and other forms of corrosion in the service environment. The purpose of terminal electroplating is to protect the reed against corrosion by isolating it from the surrounding environment. As long as the application environment doesn’t deteriorate, electroplated materials are a good choice.
There are two techniques to improve the performance of the terminal surface. To begin, the connection must be designed in such a way that a reliable terminal contact interface can be established and maintained. Secondly, in order to create metallic contact, no surface facial mask layer must be present otherwise the insertion would shatter. There is no distinction between precious metal plating and non-precious metal plating when it comes to film and film rupture.
Gold, palladium, and their alloys are inert and do not form a film during electroplating. As a result, metallic contact is “automatic” for certain surface treatments. To maintain the terminal’s “noble” surface from external causes including pollution, substrate diffusion, and terminal corrosion, we need to think about a few things.
Tin, lead, and related alloys are often used as non-metallic electroplating materials. These materials are typically shielded from metal contact by an oxide layer, but when introduced, the oxide film breaks down and metal contacts are made.
Precious metal electroplating at the terminals
Terminal electroplating refers to the coating of precious metal that covers the nickel underneath it. The thickness of a connector’s gold or nickel plating might range from 15 u to 100 u. Gold, palladium, and their alloys are the most widely utilized precious metals.
Because of its high electrical and thermal conductivities, gold is the perfect material for electroplating. As a matter of fact, it is unaffected by corrosion in any setting. Gold is the most common electroplating for connections in high-reliability applications because of these benefits, but the cost of gold is prohibitive.
The valuable metal palladium is similar in properties to gold, although it has a lower heat transfer coefficient and a lower corrosion resistance, but it is better at resisting wear. The connector’s terminals are typically made of a palladium nickel alloy (80/20). (post).
When developing precious metal electroplating, the following considerations must be made:
Porosity
Gold nucleates on numerous stains exposed to the surface during the electroplating process. There is a constant expansion of these nuclei on the surface. When these islands (isolated items) finally meet and fill the surface, an electroplated porous surface is formed. The porosity of gold coating is related to the thickness of the coating in a specific way. Porosity rises fast below 15u, then drops precipitously over 50U, at which point the decrease rate is so small that it may be disregarded. Since precious metal plating often has a thickness of 15 to 50u, this is why. Additionally, substrate flaws such as inclusions, laminations, stamped markings, inadequate stamping cleaning, and improper lubrication all contribute to porosity.
Abuse and neglect
The substrate will become exposed when the electroplated surface of the terminal degrades. It is the friction coefficient and the hardness of the electroplated surface that determines how long the coating will last. The friction coefficient drops and the service life of surface treatment are increased as hardness increases. Cobalt (CO) is one of the most popular hardeners in electroplated gold, and it may increase the gold’s wear resistance. Electroplating with palladium nickel may enhance precious metal coatings’ friction resistance and service life. Most often, a 2030u PD Ni alloy with a 3U gold coating is used. This alloy has a strong conductivity and wear resistance. For further protection, nickel underlayers are often employed.
Precious metal electroplating requires careful consideration of the nickel substrate. To maintain the terminal contact interface’s integrity, it performs a number of critical tasks. Nickel’s positive oxide surface acts as an efficient isolation barrier, blocking both the substrate and pores, lowering the risk of pore corrosion. A firm supporting layer is supplied underneath the precious metal electroplated coating, enhancing the coating’s service life. What is the ideal thickness? Lower wear is associated with thicker nickel bottom layers. In terms of cost and surface roughness control, the thickness of 50 to 100u is often used.
Electroplating of nonprecious metals
For non-precious metal electroplating, the number of facial mask layers always remains the same. The presence of these coatings must be considered since the connector’s primary function is to establish and maintain a metallic contact surface. In order to preserve the integrity of the terminal contact interface during the electroplating of non-precious metals, the positive force often has to be strong enough to destroy the film layer. Terminal surfaces that have film on them should also be cleaned.
Tin (tin lead alloy), silver, and nickel are three of the non-metallic surface treatments available in terminal electroplating. It’s tin that’s the most frequent. In comparison to high current, silver offers benefits. High-temperature applications are the only places where nickel is employed.
The treatment of the surface of tin
When we talk about tin, we usually mean tin-lead alloys, particularly tin-lead alloy 93.
Since tin’s oxide coating is so easily broken down, our surface treatment idea is based on this feature. Tin coatings will have a strong, thin, and brittle oxide layer on the surface. Soft tin lies behind the oxide film. This is because the oxide of tin, which is exceedingly thin, is brittle, delicate, and easily broken when subjected to a strong force. The load is passed to the tin layer when such circumstances exist. Softness and flexibility allow it to flow easily under stress. The cracking of oxide is broader because of the flow of tin. Through the gaps and crevices in the walls. To ensure metal contact, tin is extruded onto the surface. lead serves to decrease the creation of metallic tin whiskers in tin-lead alloys. Tin whiskers are stress-induced single crystals on the electroplating surface of tin. Terminals will be shorted out by tin whiskers. Tin whiskers may be reduced by increasing lead concentrations by at least 2%. Welding connections often employ a Sn Pb alloy with an SN/Pb ratio of 60/40, which is similar to the 63/37 ratio used in our welding process. The amount of lead in electronic and electrical items has been steadily decreasing in recent years, thanks in part to new legislation. In many electroplated terminals, lead-free electroplating is required, such as tin plating in combination with copper or silver plating in combination with copper. In order to reduce tin whisker formation, nickel plating may be applied between layers of copper and tin, or a matte tin surface can be used instead.
Plating with a thin layer of silver
Because of its reaction with sulfur and chlorine to generate a vulcanized layer, silver is used as a surface treatment for non-precious metal terminals. “Diode” properties may be achieved by using vulcanized film as a semiconductor.
Silver, like gold, is also pliable. There is no friction corrosion of silver because sulfide is difficult to break down. Silver is a superb conductor and thermal conductor, and it will not melt at high currents.. High-voltage terminals may be coated using this substance.
Lubrication toward the end
Lubrication plays a varying function depending on the final surface treatment. It primarily serves two purposes: to reduce friction and to isolate the vehicle from the outside environment. First, it reduces the insertion force of the connection; second, it improves the connector’s service life by minimizing friction. By creating a “sealing layer,” terminal lubrication may isolate the contact surface from the environment and delay or avoid environmental interaction. In most cases, terminal lubrication is utilized to minimize the friction coefficient and increase the service life of the connection. Terminal lubrication is applied to the surface of tin to isolate it from the environment and avoid friction corrosion. Electroplating may be supplemented with lubricant, but only as a last resort. Welding cleaning may remove lubrication from PCB board connections that need to be welded to the PCB board. Dust clings to the lubricant, making it difficult to remove. The resistance will rise and the service life will be shortened if used in a dusty environment. Finally, the lubricant’s ability to withstand high temperatures may also restrict its use.
Terminal surface treatment summary
It’s expected that a 50U nickel substrate is covered with precious metal plating.
When it comes to gold, thickness is determined by the desired life expectancy, although porosity may have an effect.
Palladium should not be used to preserve weldability.
Rust and migration have a strong effect on silver. Typically, it’s found in power connections. Silver’s service life may be considerably extended by lubricating.
Although tin is an excellent environmental insulator, mechanical stability must be ensured