The Influence of Mold Temperature Controller On aluminum Alloy Die Casting Production
With the development of large-scale transportation technology, the lightweight of automobile and aircraft has also been put on the agenda. Industries such as automobiles and airplanes are slowly beginning to use aluminum alloy die casting (referring to pure aluminum or aluminum alloy equipment components obtained by casting processing methods) instead of traditional stamping parts. Die-casting mold temperature controllers are also increasingly used in the die-casting industry, which is of vital importance to the die-casting process. In this guide, we discuss what’s the influence of mold temperature controller on aluminum alloy die casting production.
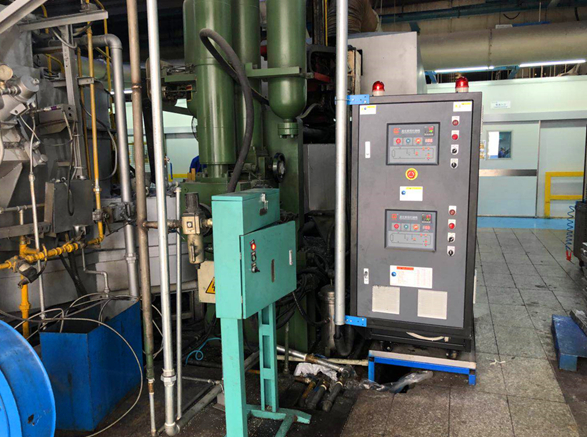
The Influence of Mold Temperature Controller On Aluminum Alloy Die Casting Production
Many people know that the defects of aluminum alloy die casting products are poor size and poor surface, but this view is wrong. These defects are because most of the aluminum alloy die casting products on the market are not high-precision products. It is necessary to use die casting mold temperature controller & machine to produce high-precision aluminum alloy die-casting products. What’s the difference between high precision aluminum alloy die casting and ordinary aluminum alloy die casting?
There are two points:
1.High precision die casting is used for high precision aluminum alloy die casting, but ordinary aluminum alloy die casting is not.
2.High precision aluminum alloy die-casting temperature control uses die-casting mold temperature machine, ordinary aluminum alloy die-casting uses electric heating tube or torch heating.
The properties of aluminum alloy die castings are as follows:
– It has good mechanical properties at room temperature and strong corrosion resistance.
– The casting property is poor, the fluctuation of mechanical properties and wall thickness effect are large.
– The stress of die-casting parts tends to decrease due to long-term corrosion.
Why must mechanical mold temperature controller be used for high-precision aluminum alloy die casting?
Because before the injection of high-precision aluminum alloy die casting, it is necessary to ensure that the mold temperature reaches a limit value, so that the whole metal jet can perfectly fill the die casting cavity before cooling. In this step, if the mold temperature is too high, the surface will blister. If the mold temperature is too low, the surface will cool in advance, and the injection is not enough for the whole cavity, what should we do? It can only increase the injection pressure, and then it will lead to large internal stress and dimensional deformation. Basically, the defect of aluminum alloy die casting is caused by this step. The higher the precision of aluminum alloy die casting production, the more important the temperature is.
In the process of pressure maintaining, the temperature of die casting mould temperature machine is also very important. The appropriate pressure maintaining temperature can reduce the internal stress of die-casting, reduce the dimensional deformation of die-casting, and reduce the internal bubbles of die-casting.
It can be seen that the die casting mold temperature controller is still very important for aluminum alloy die casting production, which can effectively improve the defective rate and dimensional deformation degree of die-casting products, and is an indispensable part of aluminum alloy die casting manufacturing.