The Importance Of CNC Programming For Die Casting Companies
The foundation of CNC programming is a very big factor affecting the machining efficiency of CNC. Excellent CNC programming can shorten the machining time by a lot. Therefore, manage the secondary development of 3D software, such as UG and CAD, and establish a unified machining template library, tool library and unified parameter setting. It can greatly improve the working efficiency of CNC programming and CNC machine tools, save manpower and improve the machining accuracy. At the same time, the programming level is also directly related to the accuracy and efficiency of EDM EDM, EDM wire cutting, Gong grinding and so on.
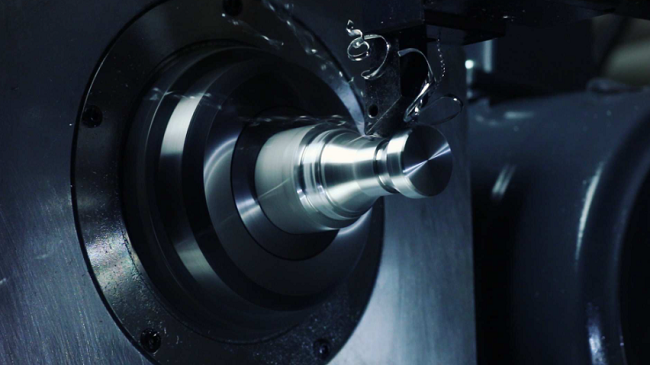
The Importance Of CNC Programming For Die Casting Companies
1. Formulate standard UG mold processing template and plug-in, which can be applied by all programmers to improve programming efficiency and reduce errors, including tool speed and feed speed. To determine the reasonable processing parameters such as die core, insert, mold embryo and electrode, the die casting company shall strictly implement the NC speed control with programming program to prevent the CNC in the workshop from changing the program and improve the efficiency.
2. The program is written according to single piece and single tool number, which is easy to operate when repairing in CNC workshop. There is no need to write the program separately.
3. Formulate complete programming manual instructions, including specific processing instructions for steel, graphite and copper.
4. Secondary development of link drawings and files to reduce manual operation and improve efficiency.
5. The secondary development program list can be used for paperless operation after maturity. The CNC workshop can open the PDF file and install the knife. The die casting company should classify and save all drawings and files and make backup.
6. Electrode automatic discharge, in cooperation with EDM spark, secondary development of automatic discharge. The basic concept is that the operator installs the electrode, divides the workpiece, opens the CNC file automatically generated by programming, and automatically discharges, including automatic completion of XYZ data, automatic setting of discharge parameters, current pulse width, etc.
7. Automatic detection of workpiece, secondary development in cooperation with QC, automatic detection. The basic concept is that the operator installs the electrode on the three-dimensional element, opens the CNC file automatically generated by programming after scoring, and automatically measures the relevant detection points.
8. Die casting companies should collect and summarize common programming errors and formulate common abnormal problems in CNC mold programming for programmers to learn and eliminate programming abnormalities.
9. The work of the programmer is carried out in accordance with the working specifications for CNC programmers, CNC mold programming parameter standards and common abnormal problems in CNC mold programming. The programmer is responsible for following up the NC progress of his own programmed mold.
10. After completing a set of molds, the program and electrode list are listed and distributed to For NC, EDM, EDM wire cutting and mold room, all relevant personnel can clearly and timely understand their required programs or the progress of electrodes. NC, EDM, EDM wire cutting and mold room can arrange work in time according to the overall schedule of molds.
11. In the early stage of design, the programmer shall participate in the design review and check the design. After the design is completed, a processing review meeting shall be held. The programmer shall dismantle the electrode at the first time, issue the material order, then write the electrode program, issue the discharge drawing, and then write the steel program. And fill in relevant progress information on the schedule.