The Difference Between Die Casting And Casting In Temperature| Diecasting-mould
In die casting and casting, how to control the temperature very well? In fact, it is not very difficult. For example, the capacity of the mold can not be very large or very small. The suitable mold capacity can make us more difficult to operate. In this article, we introduce the difference between aluminum alloy die casting and casting in temperature control.
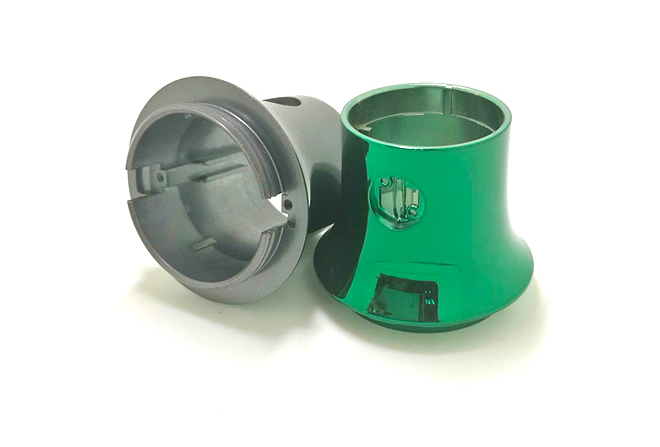
What’s The Difference Between Die Casting And Casting In Temperature
There are many reasons leading to this kind of situation, among which there will be poor casting structure. It is very easy to deform when the rubber inlet is removed, and some of the surface layer is not smooth, which leads to high friction resistance and deformation during commodity injection. In the mold part, the temperature is too high, the goods are not completely dry, the pressure is large, or the small chain is not set properly, the pressure is uneven, resulting in the deformation of goods.
Working pressure forging is a special forging method which is developing rapidly in laser cutting process of modern metal materials. It is the whole process that the molten metal material is filled with metal mold under high pressure and high speed, and the crystal condenses under high pressure to produce the casting. The key feature of aluminum die casting is high pressure and high speed. The common working pressure is tens of Kpa, the filling rate is about 16-80 M / s, and the filling time of metal material liquid is very short, about 0.01-0.2 s.
Casting is the situation that raw materials melt at high temperature and become liquid with certain flow performance. Then they are introduced into the mold. Generally, the mold is sand mold and metal material mold. After the fluidity is set in the die, they are formed by refrigeration. However, the roughness is very low. Most of them are used as rough embryo. In the future, they must be processed independently. Generally, they are used for casting raw materials It’s pig iron.
Because the metal material copper, zinc, aluminum and aluminum alloy profiles have very good liquidity and ductility, and the forging production and processing is forged in the aluminum die casting machine with working pressure, so the aluminum alloy die casting can make a variety of more complex appearance, but also can make a higher precision and smoothness, and then a large level of reducing the mechanical processing capacity and metal cost of casting parts The forging capacity of copper, zinc, aluminum or aluminum alloy profiles not only saves power engineering, metal composite materials, but also saves labor costs. Copper, zinc, aluminum and aluminum alloy profiles have high heat transfer performance, small proportion and process performance. Castings are widely used in every manufacturing industry.