Hot chamber die casting is a highly efficient and widely used metal casting technique that allows for the rapid production of complex and precise parts with excellent surface finishes. This process involves injecting molten metal into a reusable steel mold, or die, under high pressure. To achieve optimal results, the composition of the materials used in hot chamber die casting is of utmost importance. In this article, we will delve into the composition requirements for the major components involved in hot chamber die casting and highlight the critical factors that contribute to its success.
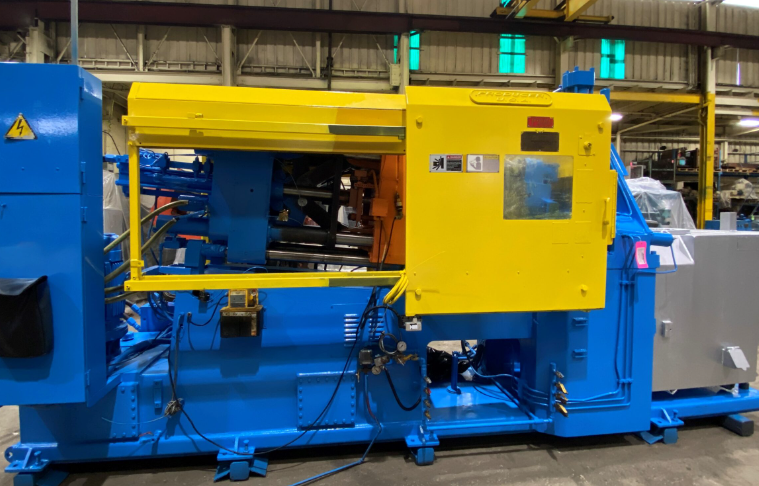
The Composition of Hot Chamber Die Casting
- Die Materials:
The die used in hot chamber die casting is typically made of high-quality, heat-resistant steel. The composition of the die material is carefully chosen to withstand the repeated thermal and mechanical stresses during the casting process. The die must have excellent thermal conductivity, high hardness, and resistance to wear and thermal fatigue. Common die materials include H13, H11, and H21 steels, which exhibit good resistance to thermal cracking and can maintain their mechanical properties even at elevated temperatures.
- Alloy Composition:
The choice of alloy composition for hot chamber die casting depends on the desired properties of the final product. Aluminum, zinc, and magnesium alloys are commonly used due to their excellent castability, strength, and lightweight characteristics. The composition of the alloy is carefully controlled to ensure proper fluidity, solidification behavior, and mechanical properties. Alloying elements such as copper, silicon, and magnesium are added to enhance specific characteristics such as strength, corrosion resistance, and dimensional stability.
- Plunger and Gooseneck:
The plunger and gooseneck assembly is a critical component in hot chamber die casting machines. The plunger is responsible for injecting molten metal into the die cavity, while the gooseneck acts as a conduit between the furnace and the plunger. These components are typically made of high-strength alloys, such as tool steels or nickel-based alloys, to withstand the high-pressure forces involved in the process. The composition of these parts ensures both mechanical strength and resistance to thermal and chemical degradation.
- Furnace Crucible:
The furnace crucible holds and melts the alloy before it is injected into the die. It must withstand high temperatures and corrosive environments without contaminating the molten metal. Common crucible materials include graphite, ceramic, and refractory metals such as molybdenum and tungsten. The composition of the crucible material ensures good thermal conductivity, chemical resistance, and durability to ensure consistent and reliable melting of the alloy.
- Shot Sleeve and Nozzle:
The shot sleeve and nozzle are responsible for transferring the molten metal from the furnace crucible to the die cavity. These components must withstand high temperatures and pressures while maintaining excellent thermal conductivity and resistance to wear and erosion. Typically, the shot sleeve is made of a high-temperature alloy such as tool steel or a nickel-based superalloy, while the nozzle is often composed of materials like zirconia or ceramic, known for their excellent thermal and chemical resistance.
The composition of the shot sleeve and nozzle materials is chosen to prevent premature solidification of the molten metal, ensure proper flow, and minimize the formation of defects such as cold shuts or porosity. Additionally, the design of these components, including their geometry and surface finish, is carefully optimized to minimize turbulence and maximize the efficiency of metal transfer.
- Cooling System:
Efficient cooling is vital in hot chamber die casting to ensure rapid solidification and dimensional stability of the cast part. Cooling channels are incorporated into the die to control the cooling rate and prevent the formation of internal defects. These channels are typically created using a network of drilled holes or integrated cooling lines.
The composition of the cooling system components, such as cooling lines or inserts, is selected based on their ability to withstand thermal cycling and resist corrosion from the coolant. Copper alloys, stainless steels, or even ceramics are commonly used in these applications due to their good thermal conductivity and resistance to degradation.
- Lubricants and Coatings:
To enhance the flow of molten metal and prevent the adhesion of the cast part to the die, lubricants and coatings are applied to the die surfaces. The composition of these substances depends on the specific casting material and process requirements. Common lubricants include graphite-based compounds or proprietary die release agents, while coatings may consist of ceramic or diamond-like carbon films.
Lubricants and coatings improve the release of the cast part from the die, minimize the occurrence of defects such as soldering or sticking, and extend the die’s lifespan by reducing wear. The appropriate composition and application of lubricants and coatings are crucial to achieving high-quality castings consistently.
- Alloy Modifiers and Additives:
In certain instances, alloy modifiers and additives are introduced to optimize the properties of the casting material. These additives can include grain refiners, modifiers, or degassing agents, which are introduced into the molten metal before injection. Their composition is carefully selected to refine the microstructure, improve mechanical properties, enhance fluidity, reduce gas porosity, or minimize shrinkage defects.
For example, titanium or boron-based grain refiners can be added to aluminum alloys to refine the grain structure and improve mechanical strength. Magnesium is commonly used as a degassing agent to reduce hydrogen gas content in the melt, minimizing the formation of porosity. The precise composition and dosage of these additives are crucial to achieving the desired casting characteristics.
- Process Control and Monitoring:
In hot chamber die casting, maintaining strict process control is essential to ensure consistent quality and dimensional accuracy of the castings. Various parameters such as injection pressure, injection time, die temperature, and cooling rate need to be closely monitored and controlled throughout the casting cycle.
Advanced control systems, often integrated with sensors and real-time monitoring, play a crucial role in optimizing the process parameters. These systems provide valuable feedback and allow for adjustments to be made, ensuring the composition and performance of the castings meet the desired specifications. Real-time monitoring of critical variables also helps detect any deviations or anomalies during the casting process, enabling quick interventions to avoid defects or scrap.
- Environmental Considerations:
As industries increasingly focus on sustainability and environmental impact, the composition choices for hot chamber die casting materials are also influenced by eco-friendly practices. Efforts are being made to reduce the use of hazardous substances and optimize material recyclability.
For instance, the selection of die lubricants and coatings considers factors such as low volatile organic compound (VOC) content and eco-friendly formulations. Additionally, there is ongoing research to develop alternative alloys with reduced environmental footprints, such as low-carbon aluminum or zinc alloys. These alloys aim to minimize energy consumption, greenhouse gas emissions, and the overall ecological impact of the casting process.
- Material Development and Research:
Continuous research and development initiatives are being undertaken to explore new materials and compositions that can further enhance the hot chamber die casting process. These efforts aim to improve the mechanical properties, casting performance, and cost-effectiveness of the materials used.
For example, researchers are investigating the use of advanced composite materials for dies, integrating ceramic or diamond-like carbon coatings to enhance wear resistance, or developing novel alloys with improved strength and corrosion resistance. Additionally, studies are being conducted to optimize the compositions of alloy modifiers and additives to achieve specific casting objectives and address challenges associated with different metal systems.
- Simulation and Virtual Modeling:
The advent of computer-aided design (CAD) and simulation software has revolutionized the hot chamber die casting industry. Virtual modeling and simulation allow engineers to predict and optimize the casting process, simulate material flow, identify potential defects, and evaluate the impact of different compositions and process parameters.
By leveraging virtual modeling, designers and manufacturers can efficiently optimize the composition of materials, reduce the number of physical prototypes needed, and minimize the time and cost associated with trial-and-error experiments. This approach facilitates the exploration of various compositions and process scenarios, leading to improved casting quality and overall process efficiency.