The convenience of using new energy vehicles goes beyond the capacity of onboard batteries; charging time also plays a crucial role. This has led major automotive companies to concentrate on developing fast-charging technology and enhancing charging efficiency, which, in turn, places more demanding requirements on the performance of onboard charging equipment.
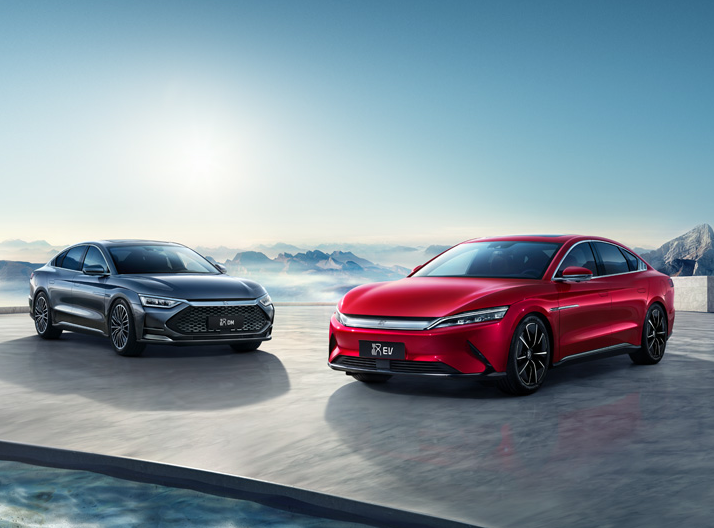
The “Casting Expert” Behind BYD and Xpeng’s Components
In the confined interior space of vehicles, the challenge lies in creating onboard charging equipment that is compact, well-sealed, lightweight, and efficient at dissipating heat. The key to meeting these requirements lies in the performance of the outer casing. There’s an enterprise based in Foshan China has taken up the challenge of providing the industry with high-performance integrated casings for onboard charging equipment. The company, with a notable reputation for superb surface quality, precise dimensions, and the ability to craft intricate, thin structures, has managed to achieve a remarkable 27% market share in the domestic market. They have become suppliers to various well-known new energy vehicle manufacturers.
Employing precision die casting in millimeters to craft high-performance automotive components, the secret behind the compact design of the aluminum alloy integrated power supply box, labeled as model HA2HE-2122111C, lies partly in the “holes” within the casing of this onboard charging equipment. These cavities are evenly distributed throughout the casing, serving as storage spaces for cooling liquid, which efficiently dissipates excess heat through fluid flow. The advanced casting technology ensures a consistently sealed state between the inner and outer casing walls, with only millimeters of space separating them, effectively preventing any liquid leakage. The internal water channels of the casing can withstand high pressures of up to 200KPa, enduring 70 seconds of inflation and pressure retention, all while maintaining a leak rate of ≤6Pa/s. This ensures a high level of sealing integrity, safeguarding both internal and external electrical components.
Furthermore, the product adheres to national and industry standards concerning machining, form, and positional tolerances, as well as casting tolerances. Any flaws such as cracks, incomplete casting, voids, bubbles that might affect functionality, or any penetrating defects on the surface are strictly prohibited. The casting tolerance grade meets the industry’s elevated level of 7, indicating that the casing, roughly the size of a shoebox, has a dimensional tolerance of less than ±0.8 millimeters.
Owing to its exceptional quality and performance, the cast casing for onboard charging equipment has found its way into the manufacturing processes of renowned new energy vehicle manufacturers like BYD, NIO, XPeng, Hezhong, and NIO. In fact, it has even secured an exclusive supplier status for numerous enterprises. The China Mold Industry Association attests to the fact that this cast casing holds a significant 27% market share nationwide, securing its place as the second-largest in the country.
With this year’s burgeoning production and sales of domestic new energy vehicles, the production line has been running tirelessly. Leveraging digitalization and intelligent tools, the company ensures the seamless delivery of products that meet high-quality standards, and with remarkable speed. In the case of crucial components like power supplies, motors, and electronic controls, new energy vehicle manufacturers often demand that suppliers complete the entire process, from mold creation to trial production, within 35 days. This is in stark contrast to the industry norm, which typically took 60-90 days. With a mold first-trial pass rate exceeding 95%, significantly surpassing the industry average of approximately 60%, molds produced by the enterprise are practically ready for immediate use. This eliminates the need for extensive post-production debugging, drastically reducing delivery time.
This achievement is largely attributed to the pioneering use of digital and intelligent tools. Within the enterprise’s R&D office, engineers utilize software such as UG, Pro/E, Solidworks, and more to generate 2D/3D mold models, presenting all internal and external parameters with utmost clarity. Furthermore, Flow-3D software aids in mold flow analysis, providing a dynamic visualization of the mold’s internal processes during die-casting mold. This enables the analysis of design rationality across different stages, including filling, pressure retention, cooling, and more. Before embarking on product project development, a comprehensive review and confirmation process with clients ensures the enhancement of structural designs, effectively preparing for both mold development and product processes.
Digitalization and intelligent tools serve as the company’s pride and differentiating edge. As early as February 2013, the enterprise introduced the EM3 mold ERP management system, transitioning from traditional “apprenticeship” mold manufacturing methods to standardized, modular, and automatically scheduled production.
In recent years, the enterprise has further incorporated MES (Manufacturing Execution) systems, PLM (Product Lifecycle Management) systems, and more software for mold structural design and die-casting process simulation analysis. These technologies collectively cater to the rapidly expanding domestic new energy vehicle market.
“Since 2015, our unwavering focus has been on the new energy vehicle market, driving continuous upgrades across all aspects of research and production,” the company revealed. “Moving forward, we anticipate our market share to exceed 35%, solidifying our position as one of the primary players in the new energy vehicle component sector.”