When assembling mechanical parts, choosing the right type of hole for fasteners is crucial for strength, durability, and ease of assembly. The three most common types—tapped holes, threaded holes, and clearance holes—each serve distinct purposes in engineering and manufacturing. Read this article, and we’re going to find out the differences between tapped, threaded and clearance holes.
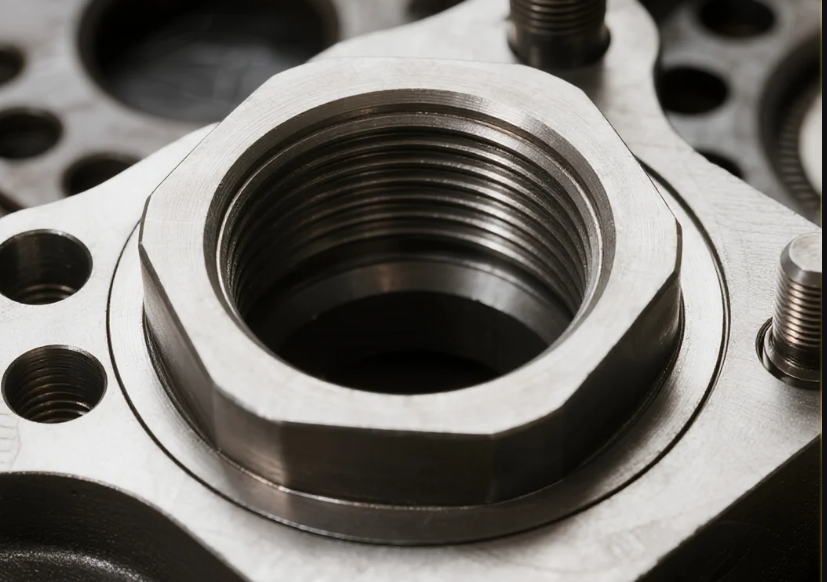
Tapped Hole Meaning – What is a Tapped Hole
Tapped hole definition is a type of hole that has internal threads created by using a tool called a tap, allowing it to securely receive a matching threaded fastener like a screw or bolt. To create a tapped hole, you must first drill a hole with the correct diameter (called the tap drill size), and then use the tap to cut threads inside that hole. Tapped holes are commonly used in metal and plastic components where strong, reusable connections are needed, such as in machinery, automotive parts, and structural assemblies. The threading typically extends the full depth of the hole, making it ideal for through-bolting or deep screw engagement.
Pros:
Strong and secure fastening: Threads provide a tight grip for bolts or screws, making tapped holes ideal for structural strength.
Compact design: Eliminates the need for a nut, saving space in tight or enclosed assemblies.
Reusable: Threads can often be reused multiple times if not damaged.
Precise alignment: Ensures accurate positioning of fasteners in machined components.
Cons:
Thread wear: Over time, repeated use can strip or damage the threads, especially in softer materials like aluminum.
More complex to make: Requires careful drilling and tapping, often with specialized tools.
Limited to certain materials: Weak or brittle materials may not hold threads well.
Repair difficulty: Damaged threads can be hard to fix and may require inserts or re-tapping.
What is a Threaded Hole?
A threaded hole is a hole that has internal screw threads cut into its walls, allowing a bolt or screw to be securely fastened into it. This is typically achieved by drilling a hole of the correct size and then using a tap tool to create the threads inside. Threaded holes are commonly used in metalworking, machining, and mechanical assemblies where components need to be joined together with precise alignment and strong, removable connections. They are essential in applications like automotive parts, machinery, and structural components where repeated assembly and disassembly may be required.
Pros:
Strong mechanical connection: Threaded holes provide a firm grip for screws or bolts, making them ideal for structural and load-bearing applications.
Compact assembly: Eliminates the need for external nuts, which is helpful in tight or enclosed spaces.
Reusable: Threads can be used multiple times if not damaged, allowing for easy assembly and disassembly.
Precise alignment: Ideal for applications requiring accurate positioning of fasteners in machined components.
Cons:
Potential thread wear: Repeated use or over-tightening can strip the threads, especially in soft materials like aluminum or plastic.
Requires precise manufacturing: Creating threaded holes involves extra steps like tapping, which adds time and complexity to production.
Difficult repairs: Damaged threads may require inserts (like Helicoils) or re-tapping to restore functionality.
Limited to specific materials: Some materials are too brittle or soft to hold threads effectively over time.
What is a Clearance Hole?
A clearance hole is a hole drilled slightly larger than the diameter of a screw or bolt, allowing it to pass through freely without engaging the threads. Unlike a threaded hole, a clearance hole does not grip or hold the fastener; instead, it provides space for the screw or bolt to slide through and fasten into a threaded component on the opposite side. Clearance holes are commonly used in assemblies where two or more parts are joined together with bolts, ensuring proper alignment and allowing for easy tightening without interference from surrounding materials.
Pros:
Easy assembly: Allows bolts or screws to pass through freely, simplifying the fastening process.
Reduces alignment issues: Helps align parts accurately when bolting components together.
No thread wear: Since there are no internal threads, there’s no risk of stripping during repeated use.
Supports bolted joints: Works well with nuts or threaded counterparts for strong, removable connections.
Cons:
Requires a second threaded component: Cannot hold a screw or bolt by itself; needs a nut or threaded hole on the other side.
Takes more space: Often requires access to both sides of the assembly, which isn’t ideal for compact or blind installations.
Not self-locking: Without threads, it provides no friction to hold fasteners in place, which may require lock washers or thread-locking compounds.
Tapped Hole vs Threaded Hole: What’s the Difference?
A tapped hole and a threaded hole are essentially the same in function, but the terms emphasize different aspects of the same concept.
A tapped hole refers specifically to the process of creating threads inside a drilled hole using a tool called a tap. It highlights how the threads are formed. A threaded hole, on the other hand, is a more general term that describes any hole that contains internal threads, regardless of how those threads were created (tapped, molded, machined, etc.).
tapped hole vs. threaded hole, key difference:
Tapped hole = How the threads are made (by tapping).
Threaded hole = The final result — a hole with threads that can accept a bolt or screw.
In practice, the two terms are often used interchangeably, especially in engineering and machining, since tapped holes are the most common type of threaded holes.
Tapped Hole vs Clearance Hole: What’s the Difference?
A tapped hole and a clearance hole serve different purposes in fastening. A tapped hole is a hole that has internal threads cut into it, allowing a screw or bolt to be directly screwed into the hole for a secure, fixed connection without needing a nut. A clearance hole is a hole drilled larger than the bolt or screw diameter, allowing the fastener to pass through freely without threading engagement. It is used when the bolt or screw needs to be fastened into a separate threaded part (like a nut or a tapped hole on another component).
Key Difference:
Tapped Hole: Holds the screw or bolt by itself using internal threads.
Clearance Hole: Allows the screw or bolt to pass through; fastening is done by a nut or threaded part elsewhere.
Tapped Hole vs Threaded Hole vs Clearance Hole, Which is the Best
Feature | Tapped Hole | Threaded Hole | Clearance Hole |
Definition | A hole that has been tapped (cut) to form threads | A hole with internal threads for fastening | A hole drilled larger than a screw for free pass-through |
Threaded | Yes | Yes | No |
Purpose | To hold a bolt or screw securely in place | Same as tapped hole (focuses on end result) | Allows a bolt or screw to pass through to fasten elsewhere |
Created By | Drill + Tap tool | Can be tapped, molded, or machined | Drill only |
Requires Nut? | No | No | Yes (or other threaded component) |
Common Use | Fastening into metal or hard material | General threaded applications | When using bolts with nuts or other threaded pieces |
Tool Needed | Drill + Tap | Varies (tap, mold, CNC machine) | Drill |
Thread Damage Risk | Moderate | Moderate | None |
Space Efficiency | High (no nut needed) | High | Lower (usually needs access to both sides) |
Ideal For | Tight, secure, single-sided fastening | General secure fastening | Multi-part assemblies, bolted joints |
Types of Holes in Engineering
In engineering, holes refer to intentionally created voids or openings in a material or component, and they come in various types based on function and geometry. Common types include through holes, which pass completely through a material; blind holes, which only go partway through; and counterbore or countersink holes, which have widened openings to accommodate fastener heads. Tapped holes are internally threaded to receive bolts or screws, while clearance holes are slightly larger to allow fasteners to pass through freely. Slotted holes are elongated to permit movement or adjustment. Each type is designed for specific applications like assembly, fastening, alignment, or fluid passage, and must meet precise tolerances for mechanical reliability.