Surface roughness is an important factor to consider in metal castings, as it can affect the functionality, appearance, and durability of the final product. What are common surface roughness values for casting parts? How to get a smooth surface finish on cast aluminum?
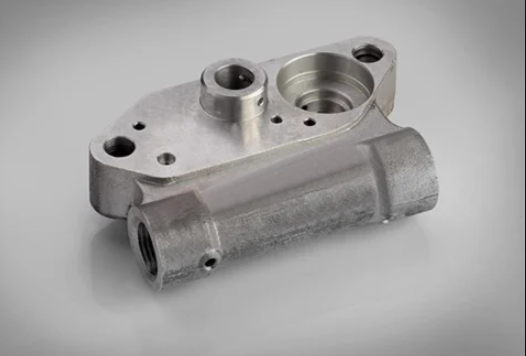
What is the Surface Roughness Value for Die Casting?
The surface roughness value for die casting is different based on several factors such as the casting material, casting process, mold design, and finishing techniques used. In general, the surface roughness value for die casting can range from 1 to 25 micrometers (µm) or 40 to 1000 microinches (µin).
Die casting is capable of producing a relatively smooth surface finish, with surface roughness values typically falling within the range of 4 to 8 µm (160 to 320 µin). However, in some cases, surface roughness values of up to 25 µm (1000 µin) may be acceptable or even desirable, depending on the specific application and requirements.
What is surface roughness in cast aluminum?
Surface roughness in cast aluminum refers to the texture or unevenness of the surface of an aluminum casting. In cast aluminum, surface roughness can be influenced by several factors, including the casting process, the quality of the mold, and the type of finishing used on the surface. Surface roughness can also be affected by the composition and quality of the aluminum alloy used in the casting.
In general, a smooth surface with low roughness is desirable for aluminum castings, as it can improve the appearance, corrosion resistance, and overall quality of the product. However, in some applications, a certain level of surface roughness may be required for functional or aesthetic reasons. To achieve the desired surface roughness in cast aluminum, various finishing techniques can be used, such as polishing, grinding, sandblasting, and chemical etching. These techniques can be used to remove surface irregularities and create a smooth, uniform surface finish.
Does Aluminum Casting Have a Good Surface Finish?
The surface finish of aluminum castings can vary depending on a number of factors such as the casting process, the quality of the mold, and the finishing techniques used. In general, aluminum casting can achieve a good surface finish that is smooth and uniform.
Aluminum casting processes such as die casting and permanent mold casting are capable of producing castings with a good surface finish. These processes involve the use of high-pressure molten metal injection into a mold to produce a smooth, detailed surface finish.
Other factors that can impact the surface finish of aluminum castings include the quality of the mold and the casting material. High-quality molds made from steel or graphite can produce smoother, more precise castings with better surface finish. Additionally, the quality and composition of the aluminum alloy used for the casting can also affect the surface finish. Finishing techniques such as polishing, grinding, sandblasting, and chemical etching can also be used to improve the surface finish of aluminum castings. These techniques can remove any surface irregularities, burrs, or imperfections to produce a smooth, uniform surface finish.
How to Get a Smooth Surface Finish on Aluminum Castings?
To achieve a smooth surface finish on aluminum castings, the following techniques can be used:
– Proper mold design: The mold used for casting the aluminum should be designed to create the desired surface finish. A smooth and detailed mold surface can transfer to the casting surface and produce a smooth finish.
– Control of casting parameters: The temperature, pressure, and speed of the casting process should be optimized to minimize turbulence and metal velocity, which can create surface defects.
– Post-casting finishing: After casting, the surface of the aluminum casting can be improved through various finishing techniques. These include:
– Sanding and filing: Sanding and filing the surface of the casting can remove any rough spots or high points and create a smoother surface finish.
– Polishing: Polishing the surface of the casting using abrasive compounds and buffing wheels can produce a high-gloss surface finish.
– Vibratory finishing: Vibratory finishing uses abrasive media to remove any surface imperfections and create a smooth finish.
– Shot blasting: Shot blasting uses a high-velocity stream of abrasive particles to remove any surface impurities and create a smooth finish.
– Anodizing: Anodizing is a process that involves coating the surface of the aluminum casting with a protective layer of oxide. This can not only improve the surface finish but also provide additional protection against corrosion.