Surface finishing can effectively improve the functional and aesthetic value of the die casting parts by enhancing their properties and appearance. What are the common surface finishing methods used for metal castings? Let’s get into the die casting surface treatment method types and tips.
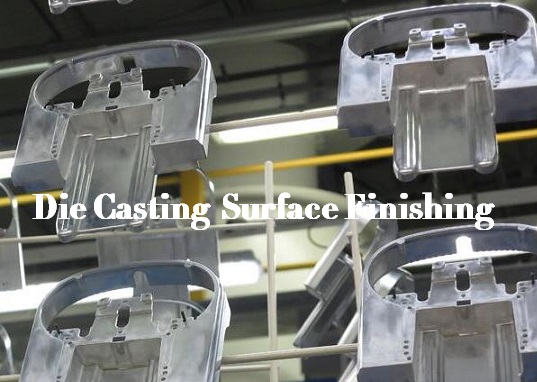
What is Surface Treatment?
Surface treatment is a method of artificially forming a surface layer with different mechanical, physical, and chemical properties from the substrate. The purpose of surface treatment on die castings is to meet the requirements of corrosion resistance, wear resistance, decoration, or other special functions of products.
For metal castings, common surface finishing methods are mechanical grinding, chemical treatment, surface heat treatment, spraying, plating, sandblasting, etc. Surface treatment is used to clean, deburr, and degrease the workpiece surface.
In the process of manufacturing, transportation and storage, the surface of workpieces often contains oxide scale, rust, molding sand, welding slag, dust, oil and other dirt. To ensure that the deep layer can be firmly attached to the workpiece surface, the workpiece surface must be cleaned before coating. Otherwise, it will not only affect the adhesion and corrosion resistance between the coating and metal, but also make the base metal continue to corrode even with the protection of the coating, so that the coating will peel off and affect the mechanical properties and service life of the die cast parts.
In order to provide a good workpiece surface, ensure the piece achieve the following conditions before surface treatment:
1. No oil stain and moisture
2. No rust and oxide
3. No adhesive impurities
4. No acid, alkali and other residues
5. The workpiece surface has a certain roughness
Surface Finishing (Treatment) Methods and Tips for Die Casting Parts
1. Manual treatment
Handle the part surface with manual tools such as a scraper, wire brush or grinding wheel. The rust and scale on the workpiece surface can be removed by hand, but the manual treatment has high labor intensity, low production efficiency, poor quality, and incomplete cleaning.
2. Chemical treatment
It mainly uses the acid-base or alkaline solution to react with the oxide and oil on the workpiece surface to dissolve it in the acid or alkaline solution, so as to remove the rust, oxide scale and oil on the workpiece surface, and then clean the brush roller made of nylon or 304 stainless steel wire.
3. Mechanical treatment
It mainly includes the steel wire brush roller polishing method, shot blasting method, and shot blasting method. The polishing method is that the brush roller rotates at high speed on the upper and lower surfaces of the strip in the direction opposite to the movement of the rolled piece driven by the motor to brush off the iron oxide scale. The brushed iron oxide scale is washed off by a closed circulating cooling water washing system. Shot blasting cleaning is to accelerate the shot by centrifugal force and shoot it to the workpiece for removal Method of rust cleaning.
Shot blasting is divided into shot blasting and sandblasting. The surface treatment with shot peening has a great striking force and an obvious cleaning effect. However, the treatment of thin plate workpiece by shot peening is easy to deform the workpiece, and the steel shot strikes the workpiece surface (whether shot blasting or shot peening). The metal base material is deformed. Since Fe304 and Fe203 are not plastic, they are stripped after crushing, and the oil film is deformed together with its material, shot blasting and shot peening cannot completely remove the oil stain on the workpiece with oil stain.
Junying offers an extensive range of surface finishing services for your die castings made of different metal materials.