Several common squeeze castings and their uses in the car sector are illustrated. Squeeze casting has been shown to be the most effective manufacturing method to enhance the qualities of castings via studies of common components. When producing components with high performance criteria that can’t be reached by conventional casting processes, it might be used as a partial replacement for forging. It is possible to use aluminum alloy in lieu of some of the cast iron and cast steel in vehicle production without sacrificing quality in the resulting castings.
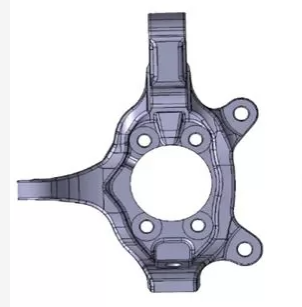
Squeeze casting allows liquid metal to solidify under high pressure or in conjunction with slight plastic deformation, eliminating defects like shrinkage cavity and porosity in the casting, resulting in a fine and dense casting structure, and allowing the mechanical properties of the casting to be greatly improved through heat treatment, bringing it close to or even on par with die forging. Potential for usefulness is high.
Squeeze casting technology is becoming increasingly used in automotive structural components due to the rise of new energy vehicles and the demand for lightweight automobiles. Some chassis components, including control arms, connecting rods, engine supports, wheel edge supports, etc., are manufactured from aluminum alloys to replace low-pressure and differential-pressure casting in order to provide high-performance complicated structural elements. Automobile manufacturers are increasingly looking to metal mold gravity casting to meet the rising need for high-reliability structural components.
One use is in the steering knuckle of a car.
The steering knuckle serves several purposes as a vital safety component of the chassis, including connection, bearing, and steering. The first production model SUV to have a steering knuckle made from aluminum alloy squeeze casting. The initial manufacturing method was sand casting of ductile iron and it weighed 4.5 kg. The steering knuckle is made with a squeeze casting method using A356 aluminum alloy. The strength of the foundational structure is evaluated in light of eight common operating scenarios for passenger car chassis components. According on the findings of the CAE study, the structure has been fine-tuned. To conclude, Figure 1 displays the finalized mathematical model and castings of the aluminum alloy steering knuckle. The weight is 2.19 Kg, a decrease of 56.6% from the original cast iron. CAE findings for eight typical operating circumstances of the optimization mathematical model for the steering knuckle are shown in Table 1. Under technical conditions, the stress distribution must be smaller than 230 MPa, which is the yield strength of A356 material.
For the pilot run, we employed a Yubu HVSC-800PL horizontal squeeze casting machine, and for the mold design, we went with an indirect extrusion process arrangement. The results show that the final liquid phase area in the solidification process is located below the center of the front wheel of the part, and the hot spot of the casting is also concentrated here, which may lead to the danger of shrinkage cavity or porosity. A combination of water cooling and local extrusion is used to enhance the circular hole linking the center and the hub, allowing for more consistent mold filling and better feeding of solidification. Aside from the need to add an exhaust slit to the mold and adjust the extrusion pin clearance, the trial production process worked smoothly because of the thorough planning and analysis done at the outset.
Squeeze casting knuckle undergoes T6 heat treatment, which includes a solution temperature of 530 °C, thermal insulation for 480 minutes, water cooling at 40 degrees Celsius, an aging temperature of 180 degrees Celsius, and further thermal insulation for 360 minutes. Taking a small piece of the casting body and analyzing its mechanical characteristics.
V2 is used in the support arm of car airbags.
The air bag support arm is the core supporting part of the automobile wheel drive axle, as shown in Figure 2. It is connected with the automobile body, the shock absorber air bag module, and the drive system. It can bear the rear load of the automobile, support the drive axle, and cushion the shock absorption air bag. Under the driving state of the automobile, it bears a variety of shock absorption loads. The main failure mode is fatigue failure.
The automobile airbag support arm was originally mainly made of nodular cast iron. In order to realize the lightweight of the automobile, foreign countries began to develop high-performance aluminum alloy airbag support arm, upgrading from iron castings, steel castings to aluminum alloy forgings, so as to realize the lightweight of airbag support arm products. The aluminum alloy air bag support arm is used for the minibus of a new energy vehicle. The mechanical property requirements are: the tensile strength of the body sample>300 MPa, the yield strength>210 MPa, and the elongation after fracture>8%.
In the early stage of development, the product was broken in the bench test. After the improvement of the product structure, see Figure 3. The product boundary at ① moved 5 mm to the left in the direction indicated by the arrow, and the transition arc was removed at ② to form a straight line. The bolt mounting hole surface was raised by 5 mm. The overall stiffness of the improved parts has been strengthened, and the stress condition is more reasonable. See Table 3 for the test results of mechanical properties sampled from the product body. After the multi wheel bench test, the product performance fully meets the design requirements.
Application in automobile control arm
It is an aluminum alloy control arm part with a maximum overall dimension of 320 mm × 154 mm, with an average wall thickness of 12 mm. The structure is optimized according to topology, the skeleton is extracted, and combined with the assembly requirements, the bar structure with arc shaped bending shape is finally designed. The assembly force relationship exists in three positions. The stress and deformation of the optimized structure meet the design requirements. The overall mass of aluminum alloy casting is 2.5 kg. From the structural characteristics of the casting, the casting has simple structure and moderate wall thickness, which is suitable for squeeze casting. There is no shrinkage cavity or porosity defect found in other parts of the squeeze casting control arm, except that there is micro shrinkage porosity in some parts of the large hole.
The microstructure diagram of the control arm casting under the extrusion specific pressure of 100 MPa shows that the metallographic structure of the control arm is: α+ Eutectic, under the condition of squeeze casting, the existence of extrusion force increases the solidification speed of the casting α The grain of the phase has been refined to a certain extent. Take samples from the control arm casting body for mechanical property test. The mechanical properties of each position of the casting are equivalent, the tensile strength is greater than 300 MPa, the yield strength is greater than 230 MPa, and the elongation is greater than 8%. Meet the design requirements. After 1 million bench tests, all performance indexes of the product fully meet the technical requirements, of which the stiffness index is higher than the original steel casting.
Application of the software in the left and right mounting brackets of commercial automobile engines
The 110 type engine support of a commercial vehicle is shown in Figure 11. It has a long life cycle and high performance requirements. The bench test parts must be able to withstand 250 kN without damage. The average wall thickness of the part is 25 mm, and the maximum wall thickness is 55 mm, which is produced by UBE HVSC 8000kN indirect squeeze casting machine. The support is made of A356.2 aluminum alloy. The mechanical properties measured by sampling from the thickest part of the product according to the design requirements are the thick and large section of the support. It can be seen from the polished corrosion map that the casting is free of any shrinkage pinholes, slag inclusion and other casting defects. Figure 16 shows the comparison of the fracture surface of the modified squeeze casting part and the metal mold gravity casting part. The fracture grain of the squeeze casting part is smaller than that of the metal mold gravity casting part. After 1 million fatigue bench tests, no permanent deformation, cracks and other problems were found. In the destructive test, the product was broken under the action of 365.7 KN force, and the index was greater than the specified value of 250 KN, close to 1.5 times.
Several typical examples of squeeze casting parts in automobile manufacturing are given, which can replace some forging parts that have high performance requirements and cannot be achieved by other casting methods. It has become the consensus of the industry to replace some cast iron and cast steel with aluminum alloy in the automobile manufacturing industry. With the development of new energy vehicles and the need for lightweight vehicles, advanced squeeze casting technology will be more and more widely used in automotive structural parts, and the application market of squeeze casting will be wider