Solidification in die casting is a process in which the liquid metal transfers to the solid phase with the liberation of latent heat of fusion. How will it affect the casting product? What should you know about it?
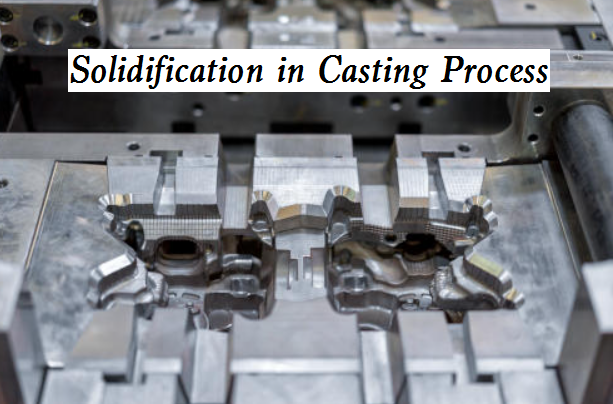
What is Solidification? - Principle of Metal Solidification
When you pour the molten metal into the mold cavity, the solidification process starts from the sides of the casting mold, then moves towards the molten metal because the sides of the mold provide sufficient cooling to the molten metal. Then the molten metal solidifies in the form of randomly oriented crystals, the region where the crystals are formed act as the production area and is called Nucleus, when the molten metal solidifies further, the crystals will change to long columnar crystals and have their axis perpendicular to the sides of the mold.
In the solidification process of castings, there are three areas on the cross-section, namely the solidified solid area, the solidification area where liquid and solid phases coexist, and the liquid phase area where solidification has not started. The width of the solidification zone has a great influence on the quality of castings, and its width determines the solidification mode of castings.
The narrower the crystallization temperature range of the alloy, the narrower the solidification area of the casting, and the more inclined to layer-by-layer solidification. For example, in sand casting, the solidification of low-carbon steel is layer by layer, while the crystallization temperature range of high-carbon steel is wide and becomes paste solidification.
Casting Temperature in Solidification
The temperature gradient of castings mainly depends on:
1) Properties of casting alloys. The better the thermal conductivity and the greater the latent heat of crystallization of the casting alloy, the stronger the ability to cast to a uniform temperature and the smaller the temperature gradient.
2) The better the heat storage capacity and thermal conductivity of the mold, the stronger the chilling capacity of the casting, and the greater the temperature gradient of the casting.
3) Increasing the pouring temperature will reduce the cooling capacity of the mold, thereby reducing the temperature gradient of the casting.
The smaller the crystallization temperature range of the alloy, the greater the temperature gradient of the casting section, the more inclined the casting is to be solidified layer by layer, and the easier it is to be cast; Therefore, when casting alloy castings inclined to paste solidification, such as tin bronze and nodular cast iron, appropriate process measures should be taken to reduce the solidification zone.
Casting Shrinkage
The casting alloy experienced three shrinkage stages from pouring to the beginning of the mold to cooling to room temperature:
1) Liquid shrinkage
The shrinkage of liquid alloy from pouring temperature to liquidus temperature is liquid shrinkage. The liquid level of the liquid alloy in the mold drops.
2) Solidification shrinkage
The shrinkage from liquidus temperature to solidus temperature is solidification shrinkage. Eutectic alloy or pure metal is crystallized at a constant temperature, with small solidification shrinkage. However, the solidification shrinkage of the alloy with a certain crystallization temperature range increases with the increase of its crystallization temperature range.
The shrinkage of the above two stages is the basic cause of shrinkage cavity and porosity.
3) Solid shrinkage
Shrinkage from solidus temperature to room temperature is solid shrinkage.
In a word, the sum of the above three stages of shrinkage is the total shrinkage of the casting alloy. Since liquid shrinkage and solidification shrinkage are mainly manifested in the reduction of the alloy volume, they are usually expressed by the volume shrinkage, that is, the shrinkage per unit volume. The solid shrinkage of the alloy mainly shows the size reduction of the casting in all directions, which is usually expressed by the linear shrinkage, or the shrinkage in unit length.