Shot blasting is a common surface treatment method used in the production of aluminum die castings to improve the surface finish, remove oxide scales, and eliminate surface defects. Shot blasting involves blasting abrasive particles at a high velocity onto the surface of the die-cast component. This process can offer several benefits when used in aluminum die-casting manufacturing processes. However, like any surface treatment method, shot blasting has its advantages and disadvantages. Here’s a closer look at the advantages and disadvantages of shot blasting in aluminum die casting.
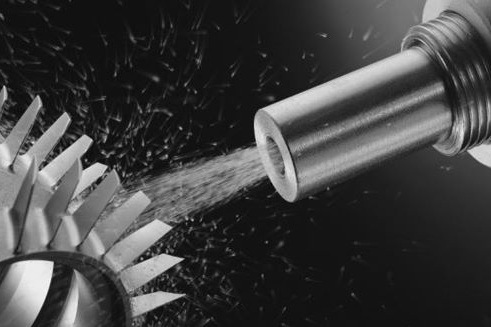
Advantages of Shot Blasting in Aluminum Die Casting
- Improved Surface Finish
Shot blasting is an effective method of producing a uniform surface finish on the die-cast components. The high-velocity abrasive particles can remove surface imperfections and blemishes, resulting in a smooth surface suitable for further finishing processes such as painting or coating. - Reduced Oxide Scales
Oxide scales can form on the surface of aluminum during die casting, resulting in poor surface quality. Shot blasting removes the oxide scales, creating a cleaner, smoother surface for finishing and improved aesthetic appeal. - Consistent Surface Profile
Shot blasting can create a consistent surface profile across a large batch of die-cast components. This ensures that all components have the same surface finish, ensuring uniformity in appearance and quality. - Improved Adhesion of Surface Coating
Shot blasting improves the surface adhesion of coating or painting applied to the die-cast component, resulting in better adhesion and a prolonged lifespan of the coating. This improves the corrosion resistance of the component, increasing its durability, and reducing maintenance costs.
- Improved Fatigue Resistance
Shot blasting can also improve the fatigue resistance of aluminum die-casting components by introducing compressive stresses on the surface of the casting. This can help to prevent crack initiation and propagation, which can extend the component’s lifespan. - Versatility
Shot blasting is a versatile surface treatment method that can be used on a wide range of aluminum die-casting components, regardless of their size, shape, or complexity. This method is particularly useful for large or irregularly shaped components that cannot be treated using other surface treatment methods.
Disadvantages of Shot Blasting in Aluminum Die Casting
- Impact on Tolerance
Shot blasting can have an impact on the dimensional tolerance of the die-cast components. The abrasive particles can remove material from the surface, causing slight dimensional variations in the final product, which can be detrimental to some applications with tight tolerances. - Abrasive Particles Residue
After shot blasting, some abrasive particles may remain on the surface of the die-cast components, which can lead to problems such as abrasion or wear. This can be minimized by proper cleaning, but appropriate cleaning procedures are necessary to ensure that the components are free of residue particles. - Safety and Environmental Concerns
Shot blasting produces dust and noise during the process, which can pose risks to operators’ safety in the manufacturing setting. Furthermore, shot blasting generates waste materials, such as used abrasive particles, which can require proper disposal and handling to minimize environmental impact. - Cost
Shot blasting can be a costly process, primarily due to the cost of the equipment, abrasive materials, and maintenance. The expenses associated with shot blasting may make it prohibitively expensive for some manufacturing operations or smaller production runs.
- Impact on Surface Integrity
The impact of the abrasive particles during shot blasting can create small surface pits or craters on the surface of the die-cast component. While these imperfections are usually minor, they can impact the component’s surface integrity and may need to be addressed through additional finishing processes. - Potential for Warping
In some cases, shot blasting can cause warping of the die-cast component, particularly if the component is thin or has a complex shape. This is because the process can generate localized stress that can deform the component. Careful consideration must be made to the design and manufacturing process to prevent or minimize this issue. - Selecting Proper Abrasive Materials
Selecting the proper abrasive material is also important for optimizing the shot blasting process. The type, size, and shape of the abrasive particles can have a significant impact on the surface finish, dimensional accuracy, and wear resistance of the component. Choosing the wrong abrasive material can lead to poor or inconsistent results.
Shot blasting is an effective method of improving the surface finish, removing oxide scales, and eliminating surface defects in aluminum die casting. However, the technique has its advantages and disadvantages. Before using shot blasting, careful consideration must be made to ensure that the process meets the production requirements and quality standards needed for the desired application. This includes assessing the impact on dimensional accuracy, surface quality, fatigue resistance, warping, safety, environmental concerns, and cost-effectiveness. By understanding the advantages and disadvantages of shot blasting, manufacturers can determine if this surface treatment solution is right for their specific production needs and goals.