Sheet metal fabrication is a processing technique that applies force to thin sheet metal to deform it and create a three-dimensional shape. The processing methods of sheet metal processing can be roughly divided into manual sheet metal and mechanical sheet metal. Manual sheet metal is formed by manually applying force to the metal plate using tools such as a hammer, while mechanical sheet metal is formed by clamping the material between molds and applying hydraulic and other mechanical forces. This time, we will introduce the basic knowledge of sheet metal processing that designers should know. A commonly used processing method in industrial products, namely mechanical sheet metal, is called “sheet metal processing”, and the parts made from sheet metal processing are called “sheet metal parts”. Read our sheet metal fabrication guide, we talk about the process, materials, forming and differences!
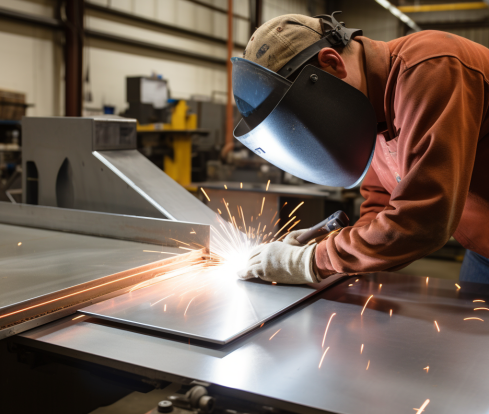
Everything You Should Know About Sheet Metal Fabrication
Metal sheet fabrication processing is called sheet metal processing. For example, using sheet metal to make chimneys, iron drums, oil tanks and kettles, ventilation pipes, large and small elbows, round corners, funnel-shaped shapes, etc., the main processes include cutting, bending, forming, welding, riveting, etc., which require a certain amount of geometric knowledge. Sheet metal parts are thin sheet metal parts, which can be processed through stamping, bending, stretching and other methods. A general definition is a part whose thickness remains unchanged during the processing. Correspondingly, they are cast parts, forged parts, machined parts, etc.
The Process of Sheet Metal Fabrication
There are approximately 8 processes involved in sheet metal processing until it leaves the factory. Let’s take a closer look at each process.
1. Expand/Program
Design drawings are often drawn using 3D CAD, and sheet metal processing must be carried out from a single sheet metal. Therefore, it is necessary to use CAD and specialized software to “unfold” the process into the state of the previous sheet metal before processing. Once the drawing is unfolded, “layout” is carried out, which is to layout the parts so that they can be efficiently obtained from standard size materials without causing waste, and at the same time, a machining program is developed.
2. Punching/cutting
In the process of cutting the outer and inner holes of metal plates, also known as cutting, laser cutting machines and turret punches are mainly used for processing. To roughly distinguish, laser processing machines are good at high-speed cutting of peripheral and large holes, while turret punching machines are also capable of handling a large number of holes and forming processing. There is also a type of “laser punching composite machine” that combines the advantages of both, and each sheet metal factory has different equipment. Therefore, when placing an order, it is best to classify the processing according to the equipment of the processing factory.
3. Deburring
Regardless of the processing method used in the previous process, laser cutting burrs (slag), punch cutting burrs, flash edges, etc. will be generated to a certain extent. The process of removing these is the deburring process. It can be done manually using a manual angle grinder or file, or using a deburring machine with rotating sandpaper for processing.
It is difficult to perform precise dimensional management such as C0.2 and R0.2 in the deburring process of sheet metal machining, just like in cutting machining. In this regard, the drawing indication of “no burrs” is ambiguous, but if it is indicated that “one wishes to remove burrs to the extent that they will not cut their hands”, it seems to be effective. When placing an order, it is best to reach a consensus with the processing plant on the allowable range of burrs.
4. Bending
The general bending process of mechanical sheet metal involves installing molds onto equipment called a bending machine and applying pressure to the cut sheet metal to bend it linearly at a certain angle. In a bending machine, the upper mold (convex mold) is installed on the upper part of the equipment, and the lower mold (concave mold) is installed on the lower part. The upper part of the equipment moves up and down to bend the metal plate, but the angle obtained by bending varies depending on the material batch and rolling direction, so fine adjustments are required each time, making processing difficult. However, it can be said to be one of the most important processes in sheet metal processing, as the difficulty and aesthetics of welding processing in subsequent processes will vary greatly due to the accuracy of the bending process. In addition, “bending machine” is sometimes also known as “bending machine”, “bending machine”, etc., they all refer to the same equipment.
5. Welding
Welding processing is a process of joining metals by heating them to melt and then cooling them. In sheet metal processing, TIG welding and laser welding are mainly used. TIG welding using tungsten electrodes is sometimes referred to as “argon arc welding” because argon gas is used as the shielding gas.
TIG welding can be carried out by adding filler rods to the melt, but on the other hand, due to the input of a large amount of heat into the material, it is prone to deformation. The processing result largely depends on the craftsman’s skills. Laser welding is a processing method that can suppress thermal strain and has the advantage of easy standardization of processing technology. However, since it is based on base metal welding, it is difficult to use this method for parts with overlay welding requirements, and the processing method needs to be changed.
6. Precision machining (including surface treatment)
The precision machining process of sheet metal processing includes removing the thermal strain generated by welding, using a grinder to remove the protruding parts of the weld overlay, using electrolytic polishing to remove burns caused by welding, and surface polishing treatment (grinding, polishing).
7. Assembly
This is the process of combining multiple parts together and mainly using fastening parts such as bolts, nuts, and rivets for assembly. Commonly used in areas that do not require welding strength or require disassembly operations later. Assembly work, also known as “assembly”, covers a wide range of tasks and processes, from small assembly of parts to medium-sized units, as well as the final assembly of the entire machine and equipment. In the sheet metal processing industry, some companies refer to the above welding assembly process as “assembly” (welding assembly).
8. Inspection
In the pre factory inspection of sheet metal processing products, both size and appearance are usually visually inspected. In size inspection, we mainly use calipers, graduated rulers, angle gauges, etc. to check for errors in size, hole position, and accuracy by comparing the drawings with the finished product. In the appearance inspection, we will visually inspect the product for scratches and burrs. Some factories use image measuring instruments or coordinate measuring machines for inspection.
Common Materials for Sheet Metal Fabrication
Galvanized steel plate SECC
The substrate of SECC is a general cold-rolled steel coil, which becomes an electroplated product after undergoing degreasing, pickling, electroplating, and various post-treatment processes on a continuous electroplated production line. SECC not only has the mechanical properties and similar processability of general cold-rolled steel sheets, but also has superior corrosion resistance and decorative appearance. It has great competitiveness and substitutability in the market of electronic products, home appliances, and furniture. For example, SECC is commonly used in computer cases.
Ordinary cold-rolled sheet SPCC
SPCC refers to the continuous rolling of steel ingots into steel plate coils or sheets with the required thickness by a cold rolling mill. The surface of SPCC lacks any protection and is highly susceptible to oxidation when exposed to air, especially in humid environments where the oxidation rate accelerates and dark red rust appears. When using, the surface needs to be painted, electroplated, or other protective measures.
Hot dip galvanized steel plate SGCC
Hot dip galvanized steel coils refer to semi-finished products that have been hot-rolled, pickled or cold-rolled, cleaned, annealed, and immersed in a molten zinc bath at a temperature of about 460 ° C, to coat the steel sheet with a zinc layer, and then subjected to quenching, tempering, leveling, and chemical treatment. SGCC material is harder than SECC material, with poor ductility (avoiding deep drawing design), thicker zinc layer, and poor weldability.
Stainless steel SUS304
One of the most widely used stainless steels, it has higher corrosion and heat resistance than steel containing Cr (chromium) due to its Ni (nickel) content. It has excellent mechanical properties, no heat treatment hardening phenomenon, and no elasticity.
Stainless steel SUS301
The content of Cr (chromium) is lower than SUS304, and its corrosion resistance is poor. However, after cold processing, it can achieve good tensile strength and hardness in stamping processing, with good elasticity. It is mainly used for spring springs and EMI prevention.
Commen Sheet Metal Fabrication Forming Process
Sheet metal (usually made of steel or aluminum) plays an important role in the construction and manufacturing industry. In the construction industry, it is used as a building and shell or roof; In the manufacturing industry, sheet metal is used for automotive parts, heavy-duty machinery, etc. When manufacturing sheet metal parts, manufacturers often use the following forming processes.
Curled Edge
Curling is a sheet metal forming process. After the initial production of sheet metal, there are usually sharp edges with “burrs”, and the purpose of curling is to make the sharp and rough sheet metal edges smooth to meet the project’s usage requirements.
Bending
Bending is another common sheet metal forming process. Manufacturers usually use brake presses or similar mechanical presses for metal bending, where the sheet metal is placed on a mold and the punch is pressed down on it, causing the sheet metal to bend under immense pressure..
Ironing
Sheet metal can also be ironed to achieve uniform thickness. For example, many beverage cans are made of aluminum, and the aluminum metal plate is too thick for the beverage can in its original state, so it needs to be ironed to make it thinner and more uniform.
Laser Cutting
Laser cutting has become an increasingly common sheet metal forming process. Sheet metal is exposed to high power and high density laser, and the heat of the laser causes the sheet metal in contact to melt or vaporize, forming a cutting process. This is a faster and more accurate cutting method that is automatically executed using a computer numerical control (CNC) laser cutting machine.
Stamping
Stamping is a common sheet metal forming process that uses stamping machines and mold sets to drill holes on the sheet metal. During processing, the sheet metal is placed between the punch and the mold, and then the punch is pressed down and passed through the metal plate, completing the punching process.
The processing steps for processing components in the sheet metal workshop include: product preliminary testing, product processing trial production, and batch production of products. During the trial production process of product processing, timely communication and contact with customers should be made to obtain corresponding processing evaluations before proceeding with mass production of the product.
The Difference Between CNC Machining And Sheet Metal
The difference between CNC machining and sheet metal: Sheet metal is a comprehensive cold working process mainly used for plates, profiles, and pipes, while CNC machining is mainly used for pre drawing thick plates and forging blanks, which is the process of changing the external dimensions or properties of workpieces through mechanical equipment. CNC machining mainly deals with high-strength and thick whole structural components; Sheet metal mainly handles complex parts with large dimensions and thin thickness. Most of the drawings for CNC machining are provided by the host factory and do not require design qualifications, so the threshold is relatively low.