Surface forming, roughness, and internal quality are the three most important factors in die casting production. Coatings play an important role in this process. Die casting production is a dynamic thermodynamic process in which the surface of the mold cavity is subjected to high-pressure, high-speed, and high-temperature erosion of molten metal. Therefore, the correct selection and reasonable use of coatings is a very important process, which has a significant impact on the lifespan of the mold, the quality of the casting, production efficiency, and the subsequent surface coating of the casting. Spraying coatings is precisely to form a film on the surface of the mold cavity, Isolate from molten metal. Choosing high-quality die-casting coatings will play a good role in product quality, mold protection, and mechanical maintenance.
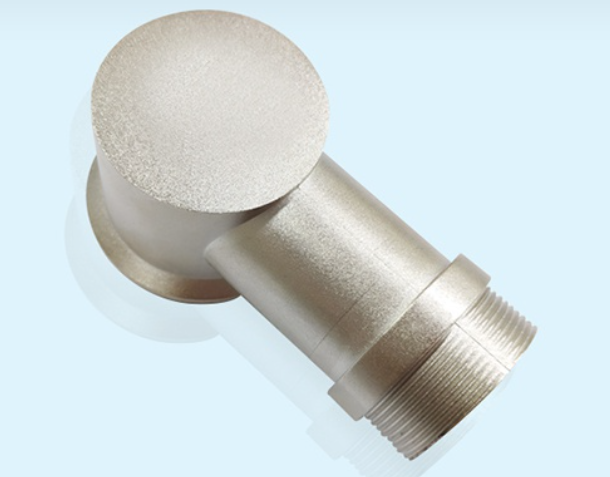
Pressure Casting Coating Guide: How To Choose & Use It
1. Ensure smooth filling of molten metal, reduce instantaneous thermal diffusion during the filling process, facilitate forming and welding, prevent mold sticking and welding, achieve a bright, smooth and flat surface of the casting, and improve the quality of the casting.
2. Avoid the erosion and adhesion of molten metal on the surface of the mold, reduce the instantaneous thermal conductivity and temperature of the mold, and extend its service life.
3. During mold opening, it is beneficial for the smooth demolding of the casting.
4. Reduce the friction and wear of the top rod, core and other moving parts in the mold, and extend the life of the mold.
5. Performance requirements for die-casting coatings: Die casting molds are now mostly made of H13 steel, and aluminum zinc alloy has a strong wetting effect on them, resulting in a strong adhesion trend. Therefore, there is a high demand for die-casting coatings.
Selection and Use of Coatings in Pressure Casting
When the evaporation point is low at 100-150 ℃, the diluent can quickly evaporate odorless and does not precipitate or decompose harmful and irritating gases, without increasing the gas content in the mold cavity.
2. After the dilution evaporates, it can form a thin film layer at high temperatures, but it is not easy to accumulate and does not cause corrosion to molds and castings.
3. Stable performance, no sedimentation within the specified shelf life, less volatile in the air, less environmental pollution, and low price.
Types and Selection of Coatings
Die casting coatings are divided into mold coatings (also known as release agents) and punch coatings.
1. There are various types of mold coatings, which should be determined based on the type of die-casting alloy, mold structure, casting shape, surface quality of the mold cavity, and operating technology. Aluminum alloy has the strongest adhesion to the mold surface, thus requiring higher requirements for coatings. However, magnesium alloy is sensitive to coatings due to its strong oxidation and high tendency for hot cracking, and special attention should be paid when selecting.
2. Due to the large mating surface between the punch and the pressure chamber, fast movement speed, and high working temperature, the selected coating should not only be effective, but also be able to fill the mating gap and provide isolation at high temperatures.
3. High temperature agent is used for demolding the top rod and moving the mold; Protective grease for formwork; Protective oil is used for mold rust prevention; High temperature resistant protective layer is used for pouring buckets, gates, internal gates, and other parts.
Composition and characteristics of water-based coatings
The basic components of water-based coatings are mineral oil, paraffin, additives, and more than ten other raw materials that are emulsified. Among these components, as long as there is a 1% change in the formula of one raw material, the products produced will be different. Different models should be selected based on the quality of the castings. Especially when zinc alloy products require surface treatment, paraffin-free release agents should be selected. As shown in the table below, water-based release agents for die-casting first appeared in the 1960s. Due to their safety, hygiene, small gas generation, ability to provide external cooling to the mold, improve the surface finish of the casting, and overall productivity, water-based release agents are quickly widely used. They are made by emulsification with refined oil and various additives.
Spraying process
1. The comparison concentration (dilution ratio) of the coating (release agent) provided by the manufacturer is within a certain range (such as mixing 100 to 200 times water). The concentration is too low and the isolation film is too thin to resist the erosion of liquid metal thermal stress, resulting in mold sticking, difficulty in ejection, and strain; However, if the concentration is too high and the isolation film is too thick, it will affect the surface quality of the casting and cause coating accumulation in the mold cavity. After demolding, it will enter the liquid metal, leading to the formation of pores, and excess coating will also block the exhaust channel.
The dilution ratio of the coating is an important process parameter, which should be compared based on the size, structure, and thickness of the casting. The dilution ratio of large parts, thin wall parts and complex parts should be lower, and the dilution ratio of small parts and simple parts should be higher. The most appropriate dilution ratio and spray amount can be determined through pressure test, and the concentration can be checked and verified with a colorimeter.
3. The atomization effect depends on the pressure of the spraying device (such as the spray gun) pipeline. Good atomization should be sprayed out in a fine mist shape, while poor atomization is like a faucet spraying water. Good atomization can evenly spread the coating on the surface of the mold cavity.
4. Mold temperature is the main parameter that affects the adsorption of paint on the surface of the mold cavity. When the mold temperature is low (140 ℃), the sprayed coating quickly cools to below the vaporization point of water, and the coating cannot deposit on the surface of the mold to form an isolation film, which is also easy to cause porosity and looseness in the casting; If the mold temperature is too high (exceeding 389 ℃), spraying paint will evaporate and rebound on the surface of the mold, without any wetting effect or the formation of an isolation film. The best temperature control for the mold in production is between 180 and 240 ℃. When the mold temperature is below 270 ℃, spraying for 1 second can form an isolation film. Only when the wetting temperature is reached can the mist like coating truly come into contact with the surface of the mold cavity, ultimately forming an isolation film.
5. To ensure the formation of a uniform isolation film on the surface of the mold, the spraying distance and spraying time should be optimized while mastering the above techniques. If the spraying distance is too small, the spraying flow will be too high, causing the mold to rebound and cause loss; If the spraying distance is too large, the atomized coating will fuse into droplets, and the impact force when falling will damage the uniformity of the isolation film. The ideal spraying distance is 100-200mm, and the spraying time is 0.1-3s to form sufficient isolation film.
For products with stable product quality, automatic spraying operation should be adopted; For test specimens and new products that do not use forming processes, manual spraying should be used. When using automatic spraying, the appropriate spraying angle should be selected based on the complexity of the mold (pay attention to areas that are not easy to spray). When manual spraying is used, operators should be required to operate according to regulations to avoid arbitrary operation that may lead to waste products.
The volatilization time, whether in manual or automatic spraying, should generally not be less than 20 seconds for the production and opening of molds (try to use copper pipes with die-casting model cavity shapes to spray release agents and compressed air to assist in blowing). In order to verify the degree of gas volatilization at different times, die-casting can also use X-ray to detect the porosity content and distribution of castings.
After removing the residual release agent from the casting, immediately remove the mold cavity, blow air to remove chips, and remove the residual release agent.
If you’re looking for the most professionable metal electrophoresis finishing services, Junying provides cheap color EPD surface treatment for metal castings!