Most of the items we use every day – from toothbrushes, smartphones, and clothing accessories to televisions, computers, or kitchen appliances – are made in some form or another using plastic. Not to mention the many plastic parts that are invisible but essential to the movement of your car or the operation of your machine. Most of these parts are completed using the injection molding process. The molds required usually use hardened or heat-treated tool steel or hard metal. These molds are difficult to manufacture, and those with complex structures are even more difficult to process. For tools used in machining mold cavities and machining cooling or hydraulic flow channels and supply systems, aggressive cutting affects the performance and thus challenges process reliability. Tool breakage, especially during deep-hole drilling, is a typical problem. Due to the hardness and toughness of the workpiece material, the cutting tools will quickly show signs of wear, negatively affecting the dimensional accuracy and surface quality of the machined parts.
Therefore, machining tools that can significantly improve process reliability are well worth investing in, especially in the field of mold manufacturing, where even a small investment can yield a big return. It is not easy to choose the right tool according to production needs and working conditions, both to meet delivery time and quality regulations and at the right cost.
Deep Hole Drilling and Internal Thread Processing
One of the most difficult processes in manufacturing injection molds (especially the mandrel holes for modular injection mold installations) is drilling deep holes. Many Walter customers have experienced the joy of success when using DC170 Supreme as a pilot drill and deep hole drill within 30xDC. The unique design of its land increases the strength of the backside of the drill tip, which is where the cutting force is greatest and the temperature is highest. This method can accurately increase the stability of drilling in the area and ensure drilling efficiency. Even when the drill bit is subjected to extremely high mechanical loads, such as for bevels or cross holes, Walter’s DC170 ensures reliable processes. The radial land takes away the extra heat generated during the cutting process through the chips; at the same time, the drill bit base material and coating also have high heat resistance: carbide is more temperature-resistant than traditional drill bits, and the TiAIN/AICrN coating (material: WJ30EJ) further increases the thermal hardness of the drill bit. The special orientation of the drill lands keeps the cut continuous, minimizing vibration. The direct effect is that the drilling dimensional accuracy and surface quality are extremely high. Compared with traditional methods, the results achieved in the same time are really very different.
In addition, joints used to connect coolant pipes to machine tools often require the same high-hardness materials. The TC685 Supreme thread milling cutter from Walter guarantees excellent process reliability and optimal tool life. The base hole, threads and chamfers (if any) are completed in one go. The geometric groove of the tool end milling edge generates stable axial force, which can improve milling stability and reduce deformation. This reduces the need for radius correction and greatly reduces tool wear. The 15° helix angle and internal cooling design starting from the M6 thread ensure reliable chip removal, thus ensuring the reliability of machining of tough materials and deep threads.
Injection Molding: Tool Applications
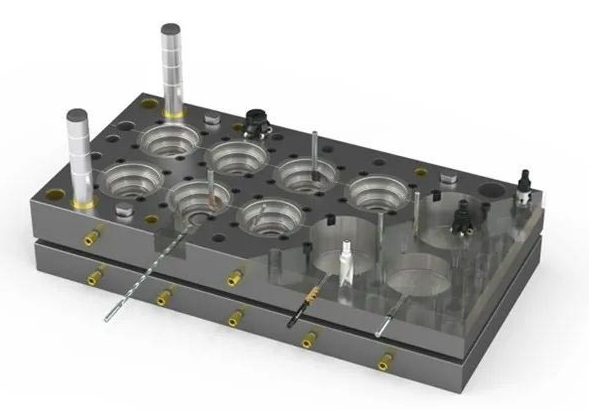
Die-cast aluminum: wheel hub production
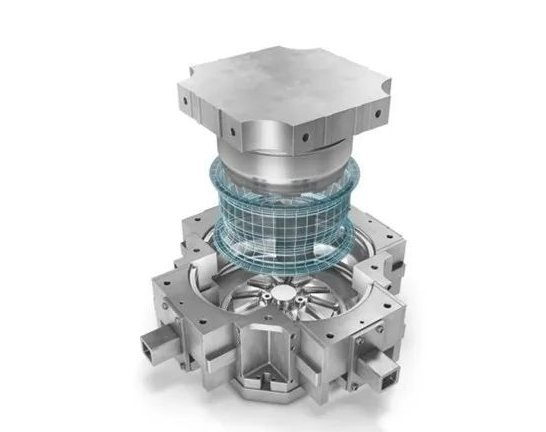
Stamp: washing machine backsplash
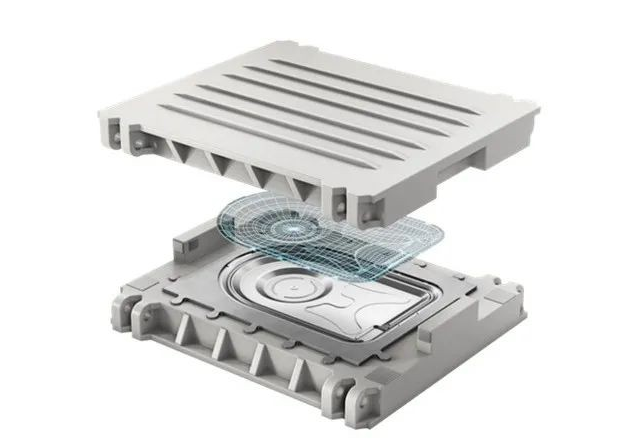
Forging Die: Crane Hook
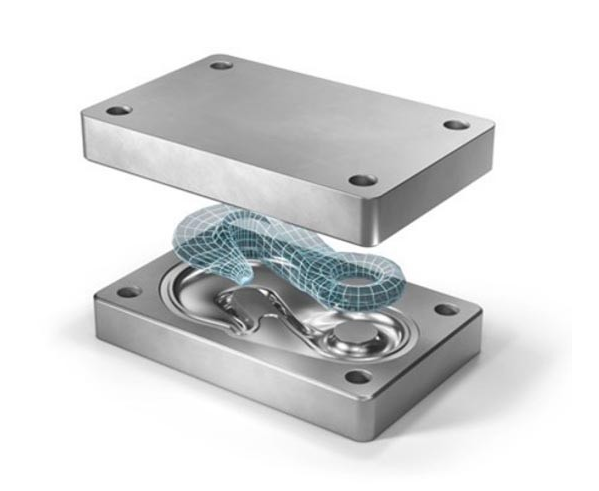