With the rapid development of society and the progress of science and technology, the performance and requirements of many new technologies for metal castings are constantly too high. Copper and copper alloys are widely used in various industries, especially in new technology and new materials industries, because of their special physical and chemical properties. Due to its high precision, copper die casting can produce parts with complex structure, high production efficiency and suitable for mass production.
Under the rapid development environment of high demand and high requirements, the market demand and scale will continue to increase. However, due to its high temperature (900-1100 degrees), high density and high requirements for equipment, molds, material melting and other processes, it also has a certain technical bottleneck. Especially in pure copper die casting and some special copper alloy die casting, it should be continuously invested in research and development in order to break through and keep up with the development. In this article, we talk about the relationship between copper die casting processing quality and die.
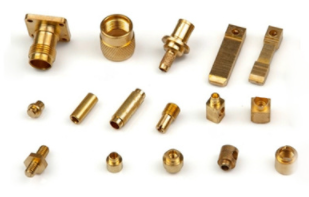
Relationship between copper die casting processing quality and die:
1. The mold structure should be reasonable, and the structure of mold parts should also be reasonable.
From the point of view of strength, the mold parts are designed as a whole, solid and durable, and are not easy to be damaged and deformed in use. However, if the shape of die-casting parts is complex and the mold parts are also complex, it will make the mold processing difficult and the machining accuracy is not high. If the mold parts are made into a combined type, the processing is greatly simplified, it is easy to obtain high machining accuracy, and then high-quality die castings can be obtained.
2. Determination of cavity number
When determining the number of cavities, we should consider the equipment capacity, the difficulty of mold processing, the size of production batch, the accuracy requirements of castings, etc.
3. Design of gating system
The gating system is not only the channel for liquid metal to fill the die casting mold, but also regulates the flow speed and pressure transfer of molten liquid, exhaust conditions, thermal stability of die casting mold and other factors. Therefore, the design of gating system must analyze the structural characteristics, technical requirements, alloy types and characteristics of castings, and also consider the types and characteristics of die casting machine, so as to design a reasonable gating system.
4. Exhaust system design
The mold shall be equipped with overflow groove and exhaust channel with sufficient overflow range, which is very important to ensure product quality.
5. Mold temperature
The temperature of the die-casting die is an important factor affecting the quality of the casting. Improper die temperature not only affects the internal and external quality of the die-casting, but also affects the dimensional accuracy of the casting and even the deformation of the casting, resulting in the cracking of the die-casting die, the formation of network burrs on the surface of the casting that are difficult to remove, and the appearance quality of the die-casting.
Generally, the mold is not heated by gas or electricity, but by preheating and cooling device. These devices use oil as the medium to preheat and cool the mold as required.
6. Determination of size of formed parts
When calculating the size of die-casting parts, the shrinkage of die-casting materials should be in line with the reality, otherwise the products produced will be unqualified.
7. Determination of parting surface position
The position of parting surface will affect mold processing, exhaust, product demoulding, etc. Usually, the parting surface will leave a trace line on the product, which will affect the surface quality and dimensional accuracy of the product. Therefore, when designing the position of parting surface, in addition to taking into account the problems of product demoulding, mold processing and exhaust, the position of parting surface can be placed where the product surface quality requirements are not high or the dimensional accuracy is not high.
8. The mold cannot be deformed
Often due to unreasonable die structure or improper selection of die materials, the die is cracked and deformed in use, resulting in unqualified products. Therefore, appropriate measures must be taken in the design to ensure the quality of products.