In the automotive aluminum alloy castings, die castings account for the vast majority of the share. Aluminum die casting is an important method for the production of engine cylinder blocks for the car. Why is it widely used and how to improve the quality of die casting engine blocks? Follow us to learn about the advantages and disadvantages of die cast cylinder blocks and the key points for the process.
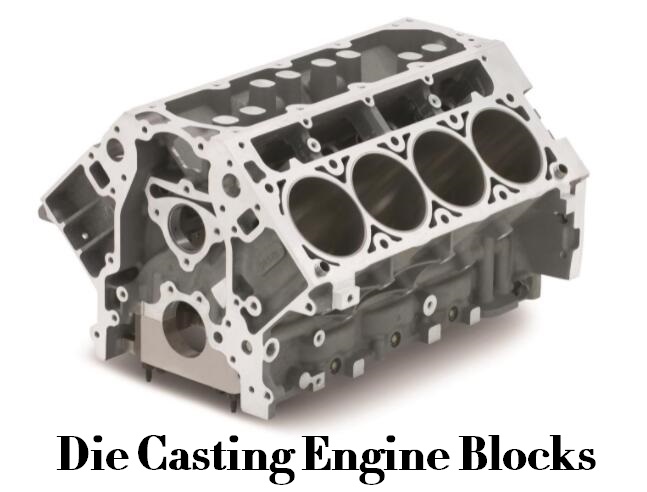
Pros and Cons of Die Casting Engine Blocks
The engine accounts for more than 20% of the weight of the car. Using aluminum alloy instead of cast iron to produce the cylinder block is of great significance to automobile weight reduction. There are many processes to produce aluminum alloy cylinder blocks, but most automobile companies have used die casting services to produce aluminum alloy engine cylinder blocks.
Compared with traditional casting, die cast cylinder block has the following advantages:
1. High efficiency. Among all casting methods, die casting is one of the most productive methods. This is mainly determined by the characteristics of the die-casting process, and will be improved with the further development of mechanization and automation of the production process. The production time of a cylinder block is generally about 3 minutes or less, which is time-saving and labor-saving compared with the traditional low-pressure or sand casting.
2. High precision. It can be used only by processing individual parts.
3. The strength and surface hardness of castings are high.
4. Energy saving. Generally, each piece of equipment can produce about 70000 pieces per year.
5. Small floor area.
6. The process route is short. In the traditional casting process, the production of cylinder block needs to go through many processes, such as molding, core making, pouring, cooling, sand dropping, cleaning, machining, heat treatment, and so on. Die casting only needs to process the mold in advance, take out the cylinder block blank casting from the die casting machine soon after pouring, remove the flash and burr, and then carry out inspection and processing.
Disadvantages of die casting engine blocks:
1. There are many casting defects. Because the filling speed of liquid alloy is very fast, it is difficult to completely eliminate the gas in the mold cavity, which is often retained in the casting in the form of pores. In addition, oxidation inclusions in the filling process of die casting are easy to remain in the product if the design of the slag collector is unreasonable;
2. The initial investment in die casting is high. According to statistics, if the number of cylinders produced is less than 100000, the cost of low-pressure casting or sand casting is lower than that of die casting.
How to Die Cast Engine Cylinder Blocks
1. Firstly, the gating system of cylinder block die casting should be designed reasonably. Generally, the gating system of cylinder block die casting has two forms: unilateral gating system and bilateral gating system. A single side gating system is generally suitable for small cylinder blocks, and a double side gating system is generally used for large cylinder blocks. The gating system shall be gradually reduced along the flow direction of liquid metal to reduce the involvement of gas. The tooth-shaped quench exhaust block has a good exhaust and slag collection effect and is widely used. The thickness of the toothed exhaust duct is roughly controlled below 0.6mm.
2. The quality of cylinder block die castings is very sensitive to the changes of injection process parameters. If the speed is too high, it is easy to increase the gas in the casting, and if it is too low, it is easy to cause poor filling. When the injection pressure is too low, the defects such as porosity and shrinkage cavity in the casting increase. If the pressure is too high, the flash and burr will increase, which will also cause great damage to the die. In the process of die casting, the process parameters should be adjusted very carefully, the appropriate injection speed should be adopted, and the reasonable speed conversion position should be determined, so that the gas in the mold cavity can be discharged as much as possible, so that the residual gas is dispersed inside the casting, rather than penetrating the casting section and forming leakage. In addition, pay attention to pressurization in time and effectively compact the castings before solidification. In fact, due to the large size, complex structure, and large difference in wall thickness, it is difficult to select a good process specification. Generally, the slow injection speed of cylinder block die casting is controlled at about 0.2m/s, the fast injection speed is controlled at 3-5M / s, or the filling speed is controlled at 30-50m / s, and the pressure is generally not less than 70MPa.
3. Cylinder block die casting is more sensitive to die casting temperature. For common alloys, the temperature of molten metal should be controlled between 640 ℃ ~ 680 ℃, and the temperature of mold should be controlled between 150 ℃ ~ 200 ℃ after spraying. In fact, the mold temperature machine has become indispensable auxiliary equipment in cylinder block die casting. At the same time, sufficient cooling/heating pipes shall be set to ensure the effective control of mold temperature. It is recommended to adopt an independent inlet and outlet cooling mode, which is adjustable. The cooling water can directly reach the required cooling parts according to the required flow, so as to give full play to the cooling effect. The temperature difference between moving and fixed mold should not be too large, otherwise, it is easy to increase the thermal stress of the casting and crack.
4. The release agent is very important for cylinder block die casting. A good release agent can not only control the temperature distribution of the mold, but also reduce the friction when opening the mold and avoid sticking the mold. Especially when the mold temperature is high, we should pay more attention to the rational and effective use of release agents.
In addition to the above factors, the quality of alloy liquid can not be ignored. Full attention shall be paid to the quality of alloy liquid to avoid alloy pollution. Degassing and refining treatment shall be carried out if necessary. The vacuum method is also an effective quality assurance measure for cylinder block die casting, but additional processes will be added.