There are various die cast valve covers used in the automotive industry, now we are going to focus on different types of valve covers and the pros and cons of die cast valve covers.
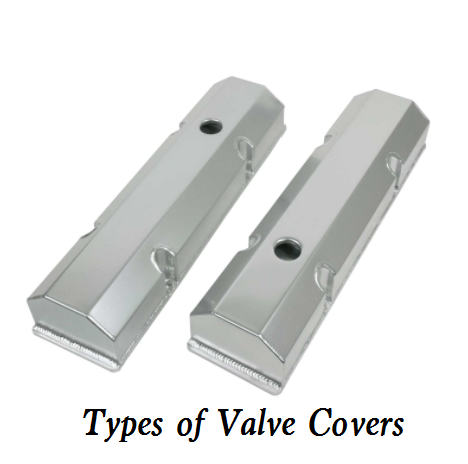
Different Types of Valve Covers
Valve covers can be manufactured using several different processes. Here are some of the different types of valve covers based on the production techniques.
– Stamped valve covers: made by stamping a flat piece of metal, typically steel, into the desired shape. The stamped valve covers may then be painted or powder-coated.
– Die-cast valve covers: made by injecting molten metal, typically aluminum, into a die or mold. The die-casting process produces a valve cover with a smooth surface finish and precise dimensions.
– Billet valve covers: made by machining a solid block of aluminum or other material into the desired shape. The billet material may be anodized or painted for a customized appearance.
– Fabricated valve covers: made by welding or brazing together individual pieces of metal. They may be made from steel or aluminum and can be customized to fit a specific engine.
– Carbon fiber valve covers: made by layering carbon fiber material over a mold and then curing the material in an autoclave. The resulting valve cover is lightweight, strong, and has a unique appearance.
When it comes to their applications, stamped valve covers are suitable for most applications, while die-cast or billet valve covers may be used to achieve a specific appearance. Fabricated valve covers may be necessary for custom engine applications, while carbon fiber valve covers are typically used in high-performance applications where weight reduction is critical.
Pros and Cons of Die Cast Valve Covers
Advantages of Die Cast Valve Covers:
– High accuracy: Die-casting is a highly accurate manufacturing process that can produce valve covers with precise dimensions and consistent quality.
– Smooth surface finish: Die-cast valve covers typically have a smooth surface finish, which makes them look attractive and easy to clean.
– Strength: Die-cast valve covers are generally stronger than stamped valve covers because of the high pressure used in the die-casting process. They can withstand higher loads and stresses without deforming or cracking.
– Corrosion resistance: Valve covers made from aluminum or other corrosion-resistant metals can provide better protection against rust and other forms of corrosion.
– Lower costs: Die-cast valve covers can be produced in large quantities at a relatively low cost, which makes them a cost-effective option for mass production.
Disadvantages of Die Cast Valve Covers:
– Limited design flexibility: Die-casting may not be suitable for complex valve cover designs or those that require intricate shapes or patterns.
– High tooling costs: The tooling used for die-casting can be expensive, especially for small production runs or custom designs.
– Limited material options: Die-casting is typically limited to a few materials, such as aluminum, zinc, or magnesium.
– Surface porosity: The die-casting process can create surface porosity or voids, which may affect the appearance or quality of the valve cover.
Materials of Cast Valve Covers
Cast valve covers can be made from a variety of materials, depending on the specific needs and goals of the engine builder or owner.
– Cast aluminum: Cast aluminum is a popular material for valve covers because it is lightweight, strong, and corrosion-resistant. Aluminum valve covers can also help to dissipate heat and reduce engine temperatures.
– Cast iron: Cast iron is another material used for valve covers, especially in older engines. Cast iron is durable, but heavier than aluminum and may not be as effective at dissipating heat.
– Magnesium: Magnesium is a lightweight material used in some high-performance valve covers. Magnesium valve covers are highly resistant to heat but can be expensive and require special handling to prevent corrosion.
– Zinc: Zinc is a relatively inexpensive material used for valve covers in some applications. Zinc valve covers can be painted or plated for a customized appearance.
– Stainless steel: Stainless steel is a strong and durable material used in some valve covers, especially in high-performance engines. Stainless steel valve covers are highly resistant to corrosion and can provide a distinctive appearance.
The choice of cast valve cover material will depend on factors such as weight, durability, heat dissipation, corrosion resistance, and cost. Aluminum is a common choice for many engine applications because of its combination of strength, lightweight, and corrosion resistance. Magnesium and stainless steel may be used in high-performance applications where weight reduction or distinctive appearance is a priority. Zinc and cast iron are less common but can be suitable for some applications where cost is a concern.