There are tons of metals and alloys that can be die cast to produce various parts, what are common zinc die cast materials, and which one to choose? In this article, let’s go through seven different types of die cast zinc alloys, along with their properties and applications.
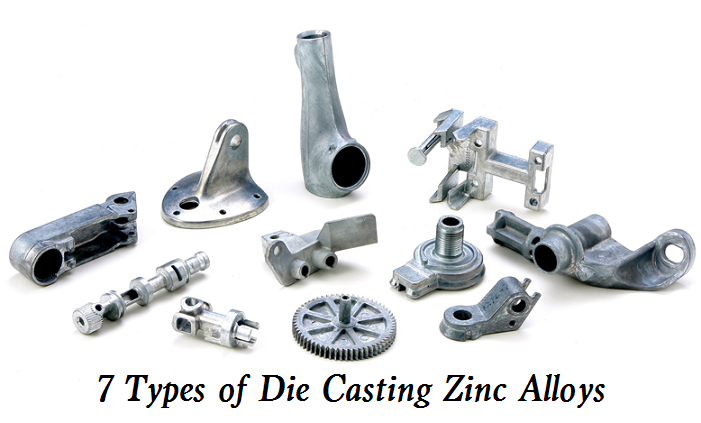
7 Types of Die Casting Zinc Alloys: Properties, Characteristics & Applications
Below is the list of 7 types of alloys used in zinc die casting services.
1) Zinc Alloy 2
Zinc Alloy 2, also known as Kirksite or Zamak 2. It is the strongest alloy in this family. However, due to the high copper content, there will be aging characteristics with the passage of time. This change includes a slight volume increase after 20 years, and the extensibility and filling cohesion ability have decreased. Although Zamak 2 is a good mold material, it is rarely used by die manufacturers. Its creep performance is higher than that of other zinc alloys, and it still maintains high hardness and fastness after aging.
2) Zinc Alloy 3
Zinc alloy 3 or Zamak 3 is the preferred material for zinc die, and is the most popular zinc alloy in North America. Its balanced physical and chemical properties are the most desirable, especially suitable for die-casting tools. Its solid shape is stable and anti-aging, which is why most molds use it as raw material. The finished product of zinc alloy 3 is of good quality and suitable for electroplating, painting, and chromic acid application. It is a standard average die casting material. If higher hardness materials are required, other types of zinc alloys should be considered.
3) Zinc Alloy 5
Zinc alloy 5 or Zamak 5 is the most commonly used zinc alloy in Europe. Because of the high copper content, the hardness and firmness are stronger, and after losing part of the scalability (continuous extension), the extensibility is stronger than that of the Zamak 3 zinc alloy. This reduction in elongation will affect the shape of the metal in the second process, such as bending, mortising, swaging, and crimping, which should be considered by the designer. Because of the high market share of Zamak 3, part engineers usually replace Zamak 5 with Zamak 3 when strengthening parts. However, if you are making products that require high elongation performance, we still recommend you use Zamak 5. Although the creep indexes of Zamak 3 and 5 zinc alloys are similar, Zamak 5 does have stronger creep resistance, and both types of alloys are suitable for arc machining. When the temperature rises beyond the normal ambient temperature, and there are special design requirements for the structural bearing capacity of the parts, Zamak 5 is relatively a better choice.
4) Zinc Alloy 7
Zamak 7 (ASTM AG40B), or zinc alloy 7 improves the die-casting property, ductility, and surface quality. Most Zamak 7 zinc alloys are used for metal components, and when there are special requirements for mold forming in its subsequent assembly operations, such as crimping or piling. Stronger die-casting property, also suitable for thin wall pressing. Some molds require stronger die-casting performance, especially for complex and fine parts, but this does not mean that it requires special pressing requirements. In order to avoid excessive sparks in the process of cutting tangent, accurate die size and parameters are essential. The high-quality extensibility of Zamak 7 is also reflected in the production process, but more is reflected in the correction and smoothing operation in the second process.
5) ZA-8
The approximate aluminum content percentage of the numerical index shows that ZA alloys are significantly richer in aluminum than Zamak alloys. ZA-8 or zinc aluminum alloy was originally made for the permanent die-casting alloy with high-quality finished products and electroplating characteristics. It is especially used as a decorative material. Although this alloy is not as good as other alloys in die-casting properties, it has the best hardness, firmness, and deformation resistance. As far as the chemical performance is concerned, the hardness, firmness, and deformation resistance of ZA-8 zinc alloy are stronger than those of other hot-dip zinc alloys. This is the only ZA alloy that can be used for hot chamber die casting.
6) ZA-27
As ZA-27 zinc alloy has high aluminum content, it can only be used for cold chamber die casting. This kind of alloy has the highest hardness and the lowest density in the ZA family. ZA-27 provides the strongest design bearing capacity compared with other zinc alloys for commercial use in the heating environment. Its bearing capacity and wear resistance are also very high.
7) ACuZinc5 Zinc
ACuZinc5 zinc alloy is developed by General Motors. Due to the increase in copper content and the decrease in aluminum content, its hardness, firmness, and deformation resistance have been significantly improved. The bearing capacity of ACuZinc5 zinc alloy is also very good.