Process and Principle of Die Casting Deplating | Diecasting-mould
Many zinc alloy die-casting factories will encounter the phenomenon of electroplating spalling in the process of producing zinc alloy die-casting parts. Die casting is no exception. In this guide, we discuss the process and principle of deplating die casting.
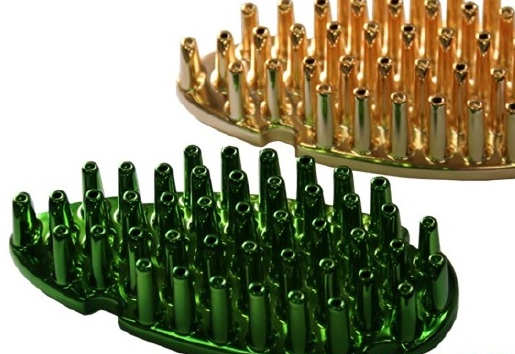
Process and Principle of Deplating Die Castings
The deplating process of hanger coating must meet the following requirements: first, the coating shall be removed quickly and completely; second, the hanger itself shall not be corroded. Like the deplating of unqualified parts, the deplating of hanger coating can also be divided into two methods: chemical deplating and electrochemical deplating. Due to the different structural shapes of hangers, the anodic oxidation method is generally used to remove the metal coating on hangers according to their structural characteristics.Method of Deplating
Chemical and electrochemical methods. It is usually preferred according to the chemical properties of the coating and the substrate.
There are two kinds of traditional chemical methods for removing cu/ni coatings: concentrated nitric acid (adding sodium chloride) oxidation method and nitro compound (anti dye salt) method. The former has low cost and fast removal rate, but it produces a large amount of nitrogen oxide gas, and is easy to cause over corrosion of the base metal; The anti staining salt, i.e. sodium m-nitrobenzene sulfonate, has no corrosion to the matrix, but needs to be removed at high temperature, with long time and low efficiency; Moreover, if it is used with the highly toxic substance sodium cyanide at the same time, the operation is improper and the harm is also very serious. Now this method is basically combined with potassium thiocyanate and ethylenediamine.
Development direction of stripping
The electrochemical method for removing the coating is to use some base metals for anodic passivation in alkaline solutions or solutions containing chromium compounds, or to add corrosion inhibitors and other substances in acidic solutions, so that only the coating metal is dissolved due to anodic oxidation. In recent years, a combined stripping bath containing complexing agents has been developed with high dissolution efficiency.
Although the deplating of unqualified parts is only a supplementary link in electroplating production, the deplating of hanger coating in automatic production line is as important as the electroplating process of each coating. Once the hanger coating is not removed cleanly, it will directly affect the composition of plating solution and the quality of plated parts. Therefore, it is very important to maintain the good effect of electrolytic stripping solution.