Before melting, the chemical composition of all metal charges must meet the requirements, and the appearance must be clean and free of oil and sediment. In this article, we’ll focus on the cast zinc alloy melting principle and the melting process in gravity casting and pressure casting.
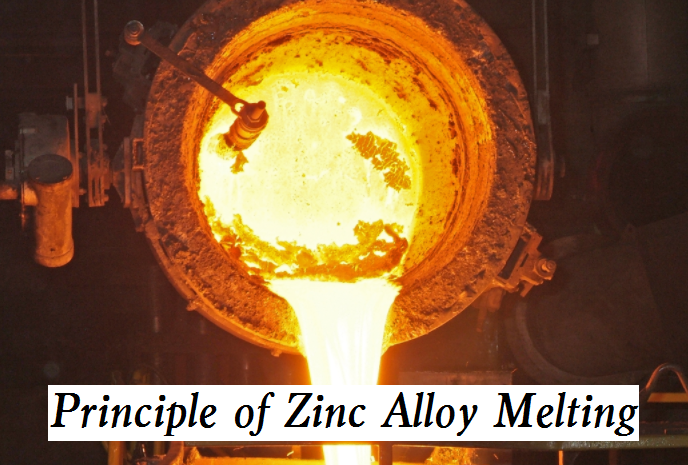
Principle of Cast Zinc Alloy Melting
Before entering the furnace, it should be preheated to 200-3000 ℃, and the new graphite crucible should be slowly heated to 900 ℃ for roasting before use. The old crucible should first be checked for damage, and then the slag and metal attached to the crucible should be removed. Preheat to 500-600t before loading. All tools in contact with zinc alloy liquid must be cleaned, sprayed with paint, and fully dried before use.
The melting process of zinc alloy is simple and easy, without special slagging and degassing treatment, nor the use of special covering agent. Fast melting speed, high melting efficiency and low energy consumption. In order to limit the introduction of harmful impurities, the purity of raw materials is required to be high. In addition, the furnace charge should be separated from aluminum alloy and copper alloy during material preparation. The melting process should be stirred up and down to avoid specific gravity segregation. Melting should be rapid and should not be excessively overheated.
When melting, attention should be paid to keeping the solution clean. The raw materials should be pure and clean. All containers in contact with liquid metal should be painted to prevent impurities on containers or tools from entering the solution; Avoid the existence of water vapor. All tools used should be dried and preheated to remove water vapor, so as to prevent accidents caused by liquid splashing and product pore defects. The preheating temperature is about 200 ℃, and the pouring temperature is strictly controlled.
The melting process of various alloys is basically the same (the selection of steps, specific raw materials, modifiers and refiners are somewhat different), and its process is divided into preparation before melting, loading, melting, adjusting chemical composition, refining, modification, adjusting temperature and pouring. The burning loss rate of various elements must be considered when batching.
Alloy Melting Process of Gravity & Pressure Casting
1. Gravity casting alloy melting
The melting methods of gravity casting alloys include an intermediate melting method and the direct melting method. The intermediate melting method is to melt the added alloy elements into intermediate alloys in advance to prevent oxidation and burning of elements. The direct melting method is a method of directly adding the required component materials.
The melting point of the master alloy made of copper with a melting point of 1080 ℃ and aluminum with a melting point of 660 ℃ can be reduced to 600-65000. The ratio of copper to aluminum is generally (2-3): 4. Generally, resistance melting is used. First, preheat the graphite crucible to about 200 ℃ and paint it 2-3 times, then dry it and put the crushed aluminum ingot into the crucible coated with paint. When heating, you can sprinkle the charcoal powder into the orange cochlea. After the aluminum melts, the preheated electrolytic copper is added to the aluminum liquid, and then the copper block is completely dissolved in the aluminum liquid by continuous stirring.
After the copper is completely dissolved, it can be cut off and refined. Commonly used refining agents are zinc chloride or hexachloroethane. Since the density of the refining agent is smaller than that of the alloy, the bell jar should be pressed down when adding to make the refining agent fully react with the alloy. Generally, the refining agent should be wrapped in paper and then pressed in. After refining, remove the charcoal and slag with a slag raking spoon and pour it into ingots.
The thickness of the cast master alloy ingot is 40-50mm, too thick will increase the difficulty of crushing.
When melting zinc base alloy with master alloy, first put 1/3 of the required mass of zinc ingot into the furnace. Set the temperature at 6500c. After the zinc melts, sprinkle the charcoal powder on its surface.
The weighed aluminum copper master alloy is gradually added to the molten zinc solution and continuously stirred. After the master alloy is completely dissolved, the power can be cut off, and then the preheated magnesium wrapped in aluminum foil is pressed into the furnace bottom with a bell jar, and stirred. Finally, the slag is removed with a refining agent.
Pouring can be carried out when the furnace temperature drops to about 450 ℃.
The specific operation of the intermediate melting method of zinc aluminum alloy: first put the copper into the crucible for heating and melting, then stop heating, and add aluminum blocks into the copper liquid for stirring. When the temperature drops to about 700 ℃, zinc blocks can be put in. After the zinc melts, the magnesium is wrapped and pressed into the furnace’s bottom. During the addition of the alloy, the alloy liquid should be properly stirred to homogenize the composition. After the melting of the alloy, refining and degassing treatment should be carried out, and slag removal should be carried out before pouring. The disadvantages of using this method to configure the alloy are that the melting temperature is high, zinc is very easy to be oxidized, and the resulting zinc oxide is harmful to human health. The specific melting method can be determined according to the specific actual production conditions.
2. Pressure casting zinc alloy melting
The melting methods of pressure casting zinc alloy include a direct melting method and the secondary melting method.
The direct melting method is to preheat the crucible to dark red at about 600 ° C, load copper material and heat it for melting, then deoxidize with 1.5% – 2% phosphor copper, and then add all aluminum. After aluminum melting, add 90% of zinc or 90% of the return charge of the planned charge mass. Raise the temperature to 6500c, press 0.1%-0.13% magnesium and 0.1%-0.13% zinc chloride into the liquid with a bell jar to stir, and finally, add 10% zinc and all the recycled materials.
In the secondary melting method, aluminum and copper are first melted into cu50al5o or cu67a133 master alloy. The melting of the aluminum copper master alloy is carried out in the crucible furnace. After preheating, add 2/3 of all aluminum materials first, and then add 1/3 of all copper materials. The remaining materials are placed on the furnace cover for preheating. After the aluminum melts, spread the covering agent, continue heating to 700-800t to melt all the furnace charge, and then add all the remaining copper material into the site vortex. After all, the copper melts, add the remaining 1 /3 aluminum, and then deoxidize and remove the slag with zinc chloride or hexachloroethane. When melting Zn Al alloy, first put 90% of all zinc materials or returned materials into the crucible, then add Al Cu master alloy and heat it to 65000. At this time, add 0.2% magnesium and 0.1%-0.12% zinc chloride, and then add the remaining 10% zinc or recycled material. Finally, zinc chloride accounting for 0.05% of the burden is added for refining, and the slag can be raked and poured after standing for 5-7min. However, in this process, the melting time and melting temperature should be controlled appropriately. If the melting time is too long or the melting temperature is in the solidification range, a large amount of slag will float on the upper part of the melt, which contains a large amount of aluminum. If the slag is removed, it will inevitably lead to a significant reduction in aluminum content.