Non-expendable mold casting is a versatile production process and can be used to create a wide variety of shapes and sizes. Let’s get into the basics of non-expendable mold casting and the differences between permanent mold casting and expendable mold casting.
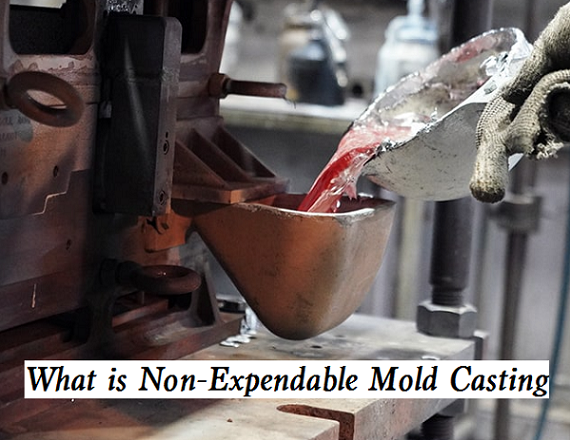
What is Non-Expendable Mold Casting?
Non-expendable mold casting, also known as permanent mold casting, is a casting process in which a reusable mold is used to create a metal part. The mold is typically made of materials such as steel, iron, or graphite and is designed to withstand the high temperatures and pressures involved in the casting process. The process begins with the mold being preheated to a specific temperature, after which molten metal is poured into the mold cavity. The metal is allowed to solidify and cool within the mold, and the mold is then opened to reveal the finished part.
Non-expendable mold casting is commonly used to produce high-quality, high-strength metal parts with excellent dimensional accuracy and surface finish. It is often used for parts with complex shapes, such as engine components, and is suitable for both small and large production runs. The process can be automated for increased efficiency and accuracy.
Applications of Non-Expendable Mold Casting
– Automotive industry: including engine parts, transmission cases, and suspension components.
– Aerospace industry: the aerospace industry relies heavily on permanent mold casting to manufacture high-performance parts for aircraft engines, landing gear, and other components.
– Electrical industry: produce electrical components such as heat sinks, housings, and connectors.
– Industrial machinery: produce components such as pumps, valves, and gears.
– Construction industry: produce architectural components such as railings, balustrades, and other decorative elements.
– Marine industry: manufacture marine parts such as propellers, marine pumps, and other marine hardware.
– Medical industry: production of medical equipment such as orthopedic implants, surgical tools, and other medical devices.
Permanent Mold Casting vs Expendable Mold Casting, What are the Differences?
Both expendable mold casting and permanent mold casting have their advantages and disadvantages, which one to choose is depending on your budget, the part complexity, surface finish, and production volume.
– Mold Material: In expendable mold casting, the mold is made of materials such as sand, plaster, or ceramic, which are destroyed and discarded after each use. In permanent mold casting, the mold is made of materials such as steel, iron, or graphite, which are reusable for multiple castings.
– Mold Preparation: In expendable mold casting, the mold is made for each individual casting, which requires more time and resources for mold preparation. In permanent mold casting, the mold is pre-prepared and can be used for multiple castings, which reduces the time and cost associated with mold preparation.
– Surface Finish: Expendable mold casting typically results in a rougher surface finish due to the nature of the mold material, while permanent mold casting can produce a smoother surface finish due to the use of more durable and precise molds.
– Complexity: Expendable mold casting is generally used for simpler shapes and designs, while permanent mold casting can be used for more complex shapes and designs.
– Production Volume: Expendable mold casting is typically used for lower production volumes, while permanent mold casting is better suited for higher production volumes due to the reuse of the mold.
Non-Expendable Mold Casting (Permanent Mold Casting) Examples & Products
Permanent mold casting is a process that is commonly used for producing a variety of metal parts that require high precision and accuracy. Here are some examples of parts that are commonly made using permanent mold casting:
– Engine components: Permanent mold casting is often used to produce engine components such as cylinder heads, pistons, and connecting rods.
– Automotive parts: Many automotive parts such as transmission cases, wheel hubs, and brake calipers are produced using permanent mold casting.
– Aerospace parts: Permanent mold casting is also used for producing aerospace parts such as turbine blades, compressor blades, and other complex shapes.
– Electrical components: Permanent mold casting can also be used to produce electrical components such as heat sinks, housings, and brackets.
– Industrial machinery parts: Permanent mold casting is often used to produce various industrial machinery parts such as pumps, valves, and gears.
These are just a few examples of the many different parts that can be produced using permanent mold casting.