Investment casting is a versatile manufacturing process used to create complex and precise metal components. One critical aspect of investment casting is the surface treatment of the cast parts to enhance their corrosion resistance and overall performance. Passivation is a widely employed technique for stainless steel hardware in investment casting. This article explores the importance of passivation, its benefits, and the process involved in achieving passivated hardware in investment casting.
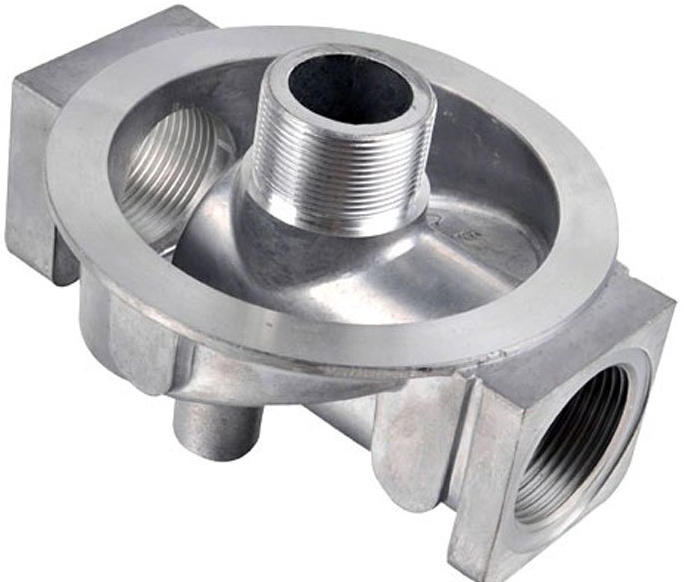
Passivated Hardware in Investment Casting: Enhancing Corrosion Resistance and Performance
- Understanding Passivation
Passivation is a chemical process that enhances the corrosion resistance of stainless steel by creating a thin protective oxide layer on the surface of the metal. This oxide layer acts as a barrier, protecting the underlying material from corrosion, rust, and other environmental factors. Passivation is especially crucial for stainless steel hardware components used in demanding applications or corrosive environments.
- Benefits of Passivation in Investment Casting
Passivation offers several key benefits for hardware components produced through investment casting:
a. Corrosion Resistance: Passivation significantly improves the corrosion resistance of stainless steel hardware. The oxide layer created during the process acts as a barrier against corrosive substances, extending the component’s lifespan and reducing the risk of failure due to corrosion.
b. Aesthetic Appeal: Passivation enhances the visual appearance of stainless steel hardware by providing a clean and uniform surface finish. This is particularly important for components used in industries where aesthetics are essential, such as architectural, automotive, and consumer goods.
c. Durability and Longevity: Passivation strengthens the protective properties of stainless steel hardware, making it more durable and resistant to wear, pitting, and staining. This extends the lifespan of the components, reducing the need for frequent replacements and maintenance.
d. Compatibility with Regulations: In certain industries, such as food processing, medical, and aerospace, passivation is often a requirement to comply with regulatory standards and ensure the safety and quality of the components.
- Passivation Process for Investment Cast Hardware
The passivation process typically involves the following steps:
a. Cleaning: Prior to passivation, the investment cast hardware must be thoroughly cleaned to remove any surface contaminants, such as oils, dirt, or residues from the casting process. This ensures that the passivation solution can effectively interact with the surface of the metal.
b. Acid Bath: The investment cast hardware is immersed in a passivation solution, usually a nitric acid-based mixture. The specific composition and concentration of the solution may vary depending on the stainless steel alloy used and the desired results.
c. Immersion Time: The hardware remains immersed in the passivation solution for a predetermined period, allowing the chemical reaction to take place and the oxide layer to form on the surface. The immersion time is carefully controlled to achieve the desired passivation level without affecting the dimensional accuracy or mechanical properties of the components.
d. Rinsing and Drying: Once the desired passivation time is reached, the hardware is thoroughly rinsed with clean water to remove any residual passivation solution. It is then dried to prevent water spots or contaminants from affecting the surface finish.
- Quality Control and Inspection
Passivated hardware components undergo rigorous quality control measures to ensure the effectiveness of the passivation process. This may include visual inspections, corrosion resistance testing, and adherence to specific industry standards or customer requirements. Quality control protocols help verify that the passivated hardware meets the desired corrosion resistance specifications and performance criteria.
Passivation is a vital step in investment casting to enhance the corrosion resistance, durability, and aesthetic appeal of stainless steel hardware components. By creating a protective oxide layer, passivation significantly extends the lifespan and reliability of investment cast parts, particularly in demanding environments. Adhering to proper passivation procedures, quality control measures, and industry standards ensures that investment cast hardware achieves optimal performance, and meets the requirements of various industries. The benefits of passivation, such as improved corrosion resistance, enhanced durability, and compliance with regulations, make it an essential process for stainless steel hardware in investment casting.
- Passivation Methods
There are different methods of passivating stainless steel hardware in investment casting, depending on factors such as the specific stainless steel alloy and the desired level of corrosion resistance. Some common passivation methods include:
-
Immersion Method: This is the most widely used method, where the hardware is immersed in a passivation solution for a specific duration. The solution chemically reacts with the stainless steel surface, creating the protective oxide layer.
-
Electrochemical Method: This method involves applying an electric current to the stainless steel hardware while it is in contact with a passivation solution. The electric current enhances the formation of the protective oxide layer, further improving the corrosion resistance.
-
Citric Acid Method: An alternative to traditional nitric acid-based solutions, citric acid passivation is gaining popularity due to its lower environmental impact. It offers similar passivation results while being safer to handle and dispose of.
- Passivation Standards and Certifications
Several industry standards and certifications govern the passivation process for stainless steel hardware. The most commonly referenced standard is ASTM A967, which provides guidelines and requirements for passivation treatments. It covers aspects such as solution composition, temperature, immersion time, and testing methods to ensure consistent and effective passivation results.
In addition to ASTM A967, there may be specific industry or customer-specific standards that must be followed. Compliance with these standards ensures that the passivated hardware meets the required corrosion resistance specifications and quality expectations.
- Advancements in Passivation Techniques
Advancements in passivation techniques continue to improve the performance and efficiency of the process. Research and development efforts focus on optimizing passivation solutions, reducing process time, and enhancing the uniformity of the oxide layer formation. These advancements aim to provide even higher levels of corrosion resistance and prolong the lifespan of investment cast stainless steel hardware.