New Technologies For Die Casting Processes - Vacuum, Extrusion, Low Pressure & More Die Casting New Technologies
In recent years, the problems of gas porosity and shrinkage holes in die castings have become more severe, which is why the need for good strength, high density, weldability, heat treatment and distortion in die castings has become more prevalent. In addition to vacuum die casting, new technologies such as squeeze casting and semi-solid die casting have been developed, which are generally called high density die casting. In this article, we introduce some advancements in die casting technology & new technologies for die casting processes, covering vacuum die casting technology, oxygen die casting technology, semi-solid die casting technology and more.
New Technologies For Die Casting Processes
1. Vacuum Die Casting Technology
The vacuum die-casting method is to evacuate the gas in the cavity (because it is unnecessary to create a vacuum normally necessary to create a die cavity when casting) to reduce the pressure in the cavity, so that the alloy melt could fill the cavity under pressure and dense die castings is obtained under solidification. Vacuum die casting requires special equipment, that is, a vacuum die casting machine. The vacuum system of vacuum die casting machines is roughly divided into two categories. One is vacuum die-casting in the die-casting mold cavity, and the other is vacuum die-casting by placing the die-casting mold in a vacuum hood. Vacuum die-casting is actually not absolute vacuum die-casting. Generally, the pressure used for vacuum die-casting is from 50.7kPa to 16 kPa. Too low vacuum cannot obtain the effect of vacuum die-casting. Of course, too high vacuum is better, but it reduces the die-casting speed. The sealing of the vacuum system is important. If air leaks at the connection part between the injection chamber and mold and between the injection chamber and injection piston, the die casting speed will be reduced and the vacuum effect will be weakened, even resulting in waste. The vacuum die-casting device will increase the complexity of the equipment, making the production cost higher. However, this disadvantage can be compensated by the advantage of vacuum die-casting.
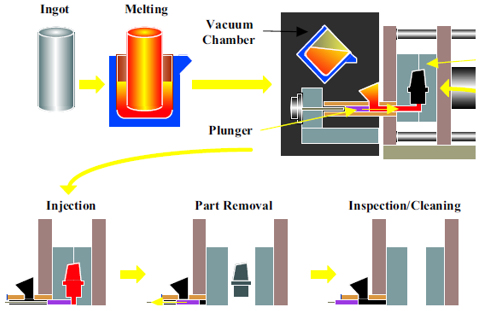
Vacuum die casting advantages:
– It greatly improves the surface finish and reduces the cost of finishing treatment.
– The vacuum process enables the cavity to be filled better, which enables thinner sections to be casted, expanding the application range of die casting.
– The mechanical properties of vacuum die-casting parts are improved, which is essential for long-term used parts. The reason is that the vacuum conditions improve the compactness of the castings and reduce the gas porosity. It is one of the important features of vacuum die-casting. This has obvious advantages for castings that are difficult to discharge and for large-scale cavities with partially concentrated bubbles due to metal flow.
2. Oxygen Die Casting Technology
Oxygen die casting technology uses oxygen to fill the pressure chamber and the cavity instead of air before the molten aluminum alloy liquid filling the cavity. On the one hand, oxygen is discharged through the discharge groove when the filling is carried out. On the other hand, alumina particles are generated by the chemical reaction between the injection molten aluminum and non-discharged oxygen, which are dispersed in the die casting, so that no gas porosity are generated in the die casting. Oxygen die-casting has characteristics of eliminating or reducing gas porosity, improving the quality of castings. The mechanical strength is increased by 10%, and the elongation is 1.5-2 times higher than the previous die casting part. Because there is no porosity in the die casting, it can be heat treated to further increase the strength and yield limit, significantly improving the impact performance. Die-cast part can work in an environment of 290-300e. Compared with vacuum die casting, oxygen die casting has advantages of simple structure, easy operation and low investment.
It takes two ways to add oxygen, one is from the pressure chamber and the other is from a device set on the die-casting mold. Generally, vertical die-casting machines mostly add oxygen from the back punch, while horizontal die-casting machines usually create oxygen holes on the die-casting mold. The two main process factors of oxygen addition time and oxygen addition pressure should be strictly controlled in oxygen die casting. In addition, the gating system and exhaust system must be reasonably designed; the injection speed must be correctly selected and the non-volatile coating must be selected to ensure the quality of die casting. Oxygen die-casting can be used to die-cast parts with high strength, high density and high temperature. It is a promising die-casting process.
3. Semi-Solid Die Casting Technology
Semi-solid die casting technology stirs the molten metal when the molten metal is solidified, obtaining a substance of about 50% or higher solid phase composition at a certain cooling rate, and then shaping the substance through die casting. At present, there are two processes for semi-solid die casting, that is rheology forming process and thixoforming process. The former is to send the molten metal to a specially designed injection molding machine barrel. The molten metal is sheared by a spiral device to become a semi-solid slurry after cooling, and then die-cast the semi-solid slurry. The latter is to send the solid metal particles or scraps to the spiral injection molding machine, and the semi-solid metal particles are die-casted under the conditions of heating and shearing. Compared with full molten metal die casting, semi-solid die casting has the following advantages:
(1) Since 50% of the latent heat of melting of the semi-solid metal has been lost during stirring, the pouring temperature is reduced, and the thermal shock to the pressure chamber, die casting cavity and die casting machine is greatly reduced. Therefore, the service life of the die casting mold is improved.
(2) The viscosity of semi-solid metal is higher than that of liquid metal and the flow rate at the inner gate is low, so there is less splashing, no turbulence and less air involved during filling. Because the semi-solid metal shrinks small, gas porosity and shrinkage cavity not easily occur on the die casting, resulting in good quality of the casting.
(3) The semi-solid metal is transported to the pressure chamber like a soft solid, and the operation is simple and convenient. The emergence of semi-solid die casting points out a new way to solving the problem of short service life of ferrous metal die casting molds, and it has a certain effect on improving the quality of castings and the working conditions of the injection system of die casting machines.
4. Extrusion Die Casting Technology
Extrusion die casting is also called liquid metal molding. Its castings have good compactness, good mechanical properties and no pouring risers. Some Chinese enterprises have already applied it in actual production. Squeeze die casting technology has excellent process advantages. It can not only replace traditional die casting, squeeze casting, low pressure casting and vacuum die casting processes, but also be compatible with counter-pressure casting, continuous casting and continuous forging and semi-solid rheological casting processes. Experts believe that extrusion die-casting technology is a cutting-edge new technology, covering multiple process fields, having rich contents, better innovation and extremely challenging.
5. Low Pressure Casting Technology Of Electromagnetic Pumps
The last new development of die casting technology is lectromagnetic pump low-pressure casting, which is a newly emerging low-pressure casting process. Compared to gas low-pressure casting technology, electromagnetic pump low-pressure casting is completely different concerning pressure adding technology and the materials it is transferring. As a method, electromagnetic pumping low pressure casting uses non-contact electromagnetic force to directly act on the molten metal, which greatly reduces the oxidation and inhalation problems caused by the impure compressed air and excessive partial pressure; realizes the smooth delivery and filling of the molten aluminum; and prevent secondary pollution caused by turbulence. Due to the fact that the electromagnetic pump system is completely controlled by digital computer, and this process is absolutely precise and accurate every time. By this process, you can produce a certain type of nanoparticles. They can be a lot better than the normal particles. This process has obvious advantages in terms of yield, mechanical properties, surface quality and metal utilization. With the deepening of research, this process has become more and more mature.