Near-net shape casting is a metal casting process that produces parts that require little finishing machining after solidification from the cast state. It aims to fabricate castings with final dimensions, surfaces, and tolerances that need only minimal post-casting machining. Today, we’re breaking down everything you should know about near net shape casting.
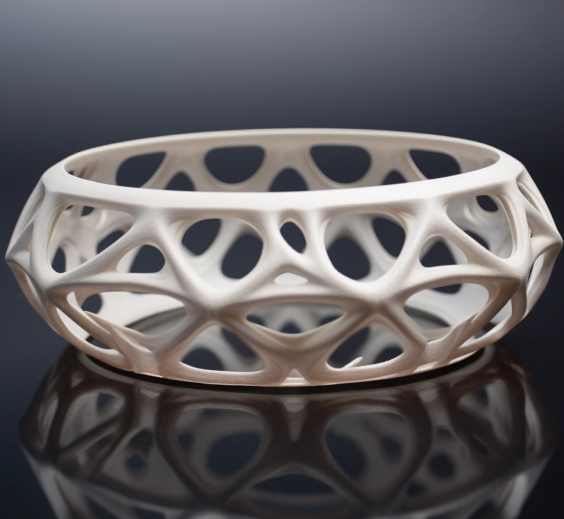
Near Net Shape Process Examples
Near-net shape processes are manufacturing techniques designed to produce parts that require minimal additional machining, thus optimizing material usage and reducing production costs. These processes aim to get as close as possible to the final shape of the part during the initial manufacturing stages. Here are a few examples of near-net shape processes:
- Powder Metallurgy:
- Process Overview: Powder metallurgy involves the compacting of metal powders into a desired shape using a die, followed by sintering to fuse the particles.
- Advantages: The sintering process allows for the creation of complex shapes, and the near-net shape achieved reduces the need for extensive machining.
- Investment Casting:
- Process Overview: Also known as precision casting, investment casting involves creating a wax pattern, coating it with a ceramic shell, melting out the wax, and pouring molten metal into the cavity.
- Advantages: Investment casting can produce intricate parts with excellent surface finishes, often requiring minimal additional machining.
- Metal Injection Molding (MIM):
- Process Overview: Similar to plastic injection molding, MIM involves combining metal powders with a polymer binder, molding the mixture into the desired shape, and then removing the binder through debinding and sintering.
- Advantages: MIM is suitable for high-volume production of small, complex parts with minimal machining needed.
- Near-Net Shape Forging:
- Process Overview: Near-net shape forging involves forging a part close to its final dimensions, minimizing the need for additional machining.
- Advantages: This process is particularly effective for producing components with simple geometries that require strength and durability.
- Thixomolding:
- Process Overview: Thixomolding, also known as semi-solid metal processing, involves injecting metal alloys in a semi-solid state into a mold to create near-net shape parts.
- Advantages: Thixomolding is suitable for producing parts with high precision and complex geometries, reducing the need for extensive post-casting machining.
- CNC Machining with Additive Manufacturing Preforms:
- Process Overview: Combining traditional CNC machining with additive manufacturing, this approach involves using 3D printing to create preforms that are then machined to near-net shape.
- Advantages: The combination of additive manufacturing and CNC machining allows for intricate designs while minimizing material waste.
- Plastic Forming for Metal Parts:
- Process Overview: Utilizing plastic forming techniques like vacuum forming or injection molding to create near-net shape metal parts.
- Advantages: This approach is cost-effective for producing parts with lower tolerances where extensive machining is not required.
How Does Near-Net-Shape Casting Work?
Designing the Part Geometry
The part geometry is designed leveraging CAD/CAM to maximize the final casting dimensions and minimize the need for post-casting machining.
Mold/Die Design
The mold or die cavity and core structures are precisely engineered to control melt flow and facilitate uniform filling for net-shape solidification.
Melting and Injection
The metal alloy is precisely melted and injected into the mold/die cavity using low-pressure die casting or other near-net shape processes.
Solidification Control
Processes like thixomolding solidify the melt in a semi-solid thixotropic state to minimize stresses and shrinkage for net-shape stability.
Minimal Runners and Risers
Feeding systems like risers are optimized to feed the cavity without compromising the final casting shape.
Cooling and Ejection
Precise cooling allows the casting to solidify with the final dimensions, tolerances and surface finishes.
Minimal Finishing
The as-cast surface requires little machining like profiling or milling to achieve functional dimensions.
Heat Treatment (Optional)
Some alloys benefit from heat treatment to refine grain structure and improve machinability.
What’s The Advantage Of Near-Net-Shape Casting?
Reduced machining costs – Only minimal finishing processes like milling are required after casting instead of extensive machining. This lowers post-casting costs.
Less material waste – Near-net shapes minimize the difference between the final part and casting, reducing dross, trimmings and other material waste.
Improved yields – Less machining means more of the casting can be used, increasing material utilization rates and yields.
Higher casting complexity – Undercuts, internal features, and complex geometries that are difficult to machine can be cast integrally.
Reduced tooling cost – Less complex and fewer mold/die components are needed compared to casting crude shapes.
Better mechanical properties – Casting near-final geometry avoids work hardening or heating from machining that can degrade material properties.
Dimensional accuracy – As-cast dimensions and tolerances are closer to CAD specifications, reducing need for final fits.
Surface quality – Surfaces may come as-cast with smoothness allowing for hardening or reduced finishing.
Production efficiency – Higher output and fewer post-casting steps streamline manufacturing flow and increase throughput.
Cost effectiveness – Reduced machining needs make near-net casting competitive versus conventional casting plus machining.
Net shape Vs Near Net Shape Casting
Net shape casting and near net shape casting represent two approaches in the realm of casting processes, each distinguished by the degree of post-casting machining required. Net shape casting epitomizes efficiency, as it refers to a casting process that yields parts demanding little to no additional machining after solidification. In this method, the as-cast part dimensions and surfaces essentially align with the final or “net” shape required for the intended application. While the concept of net shape casting embodies a streamlined and resource-efficient manufacturing process, achieving true net shape can be a formidable challenge, particularly for intricate geometries, using traditional casting methods.
Contrastingly, near net shape casting emerges as a pragmatic compromise, acknowledging the complexities inherent in manufacturing intricate parts. This approach produces parts that necessitate only minimal finishing after solidification, typically involving less than 10% material removal. The as-cast geometry in near net shape casting is remarkably close to the final part shape, but slight adjustments through light machining processes such as milling or grinding may be required to attain the desired functional sizes and tolerances. The pragmatic nature of near net shape casting makes it a more feasible option, especially when dealing with intricate internal features or stringent tolerances that may prove challenging to achieve through true net shape casting.
The key differentiator between net shape casting and near net shape casting lies in the machining requirements post-casting. Net shape casting boasts the advantage of requiring no additional machining, presenting an ideal scenario for efficiency and cost-effectiveness. On the other hand, near net shape casting strikes a balance between machinability and the complexities of part geometry, recognizing that some minimal machining may be necessary to meet the stringent criteria of the final product. Advanced casting methods, such as low-pressure die casting or thixomolding, have emerged as instrumental techniques in pushing the boundaries closer to achieving net shape or near net shape, particularly when dealing with intricate designs or high precision requirements. In essence, the choice between net shape and near net shape casting hinges on a delicate interplay between the desired part geometry, manufacturing feasibility, and economic considerations.