The multi-slide, high-speed thermal die-casting equipment is the pinnacle of precision die-casting technology for zinc alloys. When compared to conventional die-casting machines, multi-slide quick series machines can save production and labor expenses by almost half. There is everything you should know about multi slide die casting, including its application and the difference between traditional die casting.
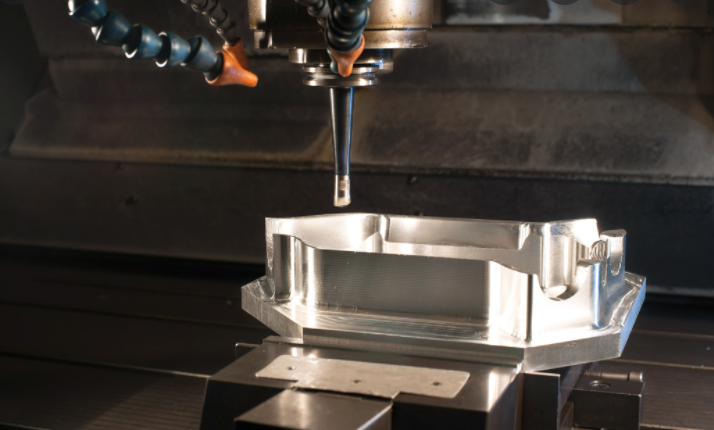
Multi-Slide Die Casting Guide: Applications & Differences Between Conventional Die Casting
The mold core is propelled along a precision cross mold base frame by two or more sliders in a multi slider precision die casting machine. One or more cavities form the ideal cavity and runner profile throughout the core’s various surfaces. With the help of a gooseneck injector, the metal liquid in the nozzle may be forced into the mold cavity. The gate cannot be created because the metal liquid is forced vertically to the intersection surface of the mold core. The mold locking system keeps the die core’s intersecting surface securely in place. The multi slide precision die-casting machine has the potential to decrease labor and material costs by more than half, making it significantly more competitive. It is capable of producing 60 molds per minute at top speed. Molds have a life expectancy of 1.5 million to 2 million cycles, and product tolerances may be held to 0.01 mm. Massive losses, a longer cycle time, and the large runner system are just a few of the problems that might arise when using the conventional die-casting method. Changyuan’s die-casting method is distinguished by its smaller gate, smaller runner optimization, more smoothness, and quicker die-casting speed.
Instances of Die Casting with Multiple Slides
Automotive steering systems, remote key accessories, high-speed iron circuit breaker accessories, and vehicle coupler accessories are just some of the many applications for zinc alloy die castings made using multi-slide die casting technique. Electronics, communications, computing, mobile phones, home appliances, etc. all make extensive use of precision die-casting zinc accessories.
Multi-Slide Die Casting vs. Conventional Die Casting
In 1936, the first multi-slide die casting technology was developed. There have been many advancements in die-casting equipment and technology since then. It might be beneficial to learn why conventional casting with numerous sliding tasks is the best option for your specific endeavor. Multiple sliding is recommended if the die casting weight is less than 400g. Larger sections can be cast using the more common die casting method. Structure, operation, and the type of die used are the primary distinctions between standard casting and multi slide casting.
In the conventional press shaft, each module consists of two parts, thus at least four modules are required. Moreover, it may help you save money even while making assembly graphics for quite complicated gadgets. Each surface mold contains a hole, or core, in the center. To cast a portion of the object, molten metal is fed into the cavity before the form is raised.
For parts weighing 400g or less, our multi-mold casting technique is ideal. Traditional die casting may still be used to produce high-quality components. However, multimode casting tools are superior in terms of reliability and precision.
Our mold is always a focal point of our focus, no matter the method. By making the most of the properties of the constituents, we may avoid the second procedure. Each time, we want to be the first net form. By eliminating the requirement for processing and lowering the overall cost of the component, proper planning is essential.