Mold coating refers to the application of specialized coatings on the surfaces of molds used in tooling production. These coatings offer several advantages in improving the performance and lifespan of the molds. Mold coatings should be based on the specific mold build, production life of the tool, and the requirements of the molding application. Not all coatings are suitable for every situation, and the selection should be made considering factors such as expected production lifespan, material compatibility, and cost-effectiveness. Today, we’re going to talk about the best mold coating!
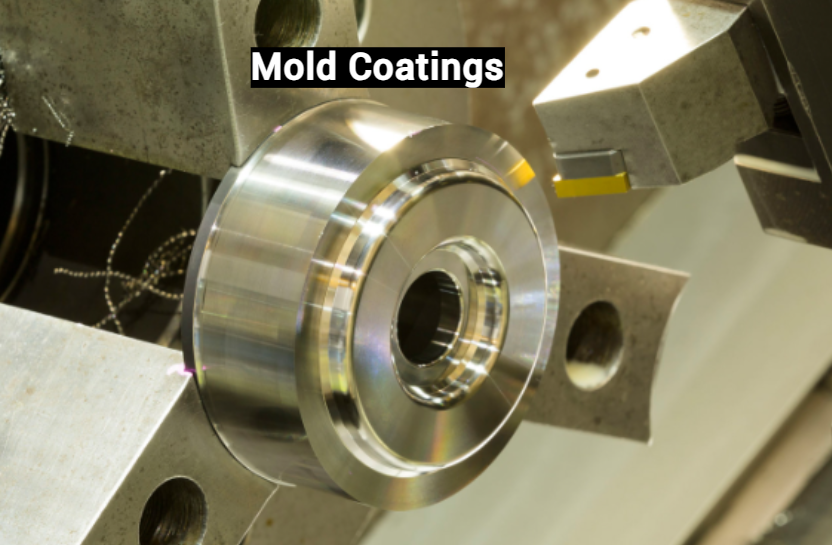
What Are The Advantages Of Mold Coating?
Slip Properties or Coefficient of Friction: Mold coatings can enhance the coefficient of friction, reducing it from 0.45 up to 0.05 microns. This improvement allows for smoother movement and operation of the tools without the need for additional mold release agents.
Increased Hardness Surface: Coating the mold surfaces with specialized materials can significantly increase their hardness. This higher hardness level improves wear resistance and extends the lifespan of the mold components.
Wear Resistance: Mold coatings enhance the mold’s ability to withstand wear caused by repeated use and contact with materials. The coatings provide a protective layer that prevents the mold surfaces from deteriorating quickly.
Corrosion Protection: Mold coatings offer corrosion resistance, protecting the mold surfaces from degradation caused by environmental factors or corrosive materials used in the molding process.
Six Types Of Mold Coatings
- Thermal Spray: The melted metal or alloy material is sprayed onto the mold surface using a spray gun, forming a layer of hard coating. Common thermal spray materials include carbide, ceramics, and metals.
- Plating Treatment: Electroplating or chemical methods are used to form a layer of metal or alloy coating on the mold surface. Common plating materials include nickel, chromium, titanium, tin, etc., which can improve the mold’s wear resistance and corrosion resistance.
- Physical Vapor Deposition (PVD): A thin film layer is formed on the mold surface through physical vapor deposition technology. Common PVD coating materials include TiN, TiCN, and TiAlN, which can enhance the mold’s hardness and wear resistance.
- Chemical Vapor Deposition (CVD): A chemically reactive coating is formed on the mold surface through chemical vapor deposition. Common CVD coatings include silicon carbide, boron nitride, etc., which can improve the mold’s hardness and wear resistance.
- Oxidation Treatment: A layer of oxide film is formed on the mold surface to improve its corrosion resistance and surface hardness. Common oxidation treatment methods include anodizing, phosphating, etc.
- Polymer Coating: Polymer materials are sprayed or coated to form a wear-resistant and corrosion-resistant coating. Common polymer coating materials include polyimide, polyurethane, polyether, etc.
How to Choose the Best Coating for Mold?
Choosing the best mold coating involves considering several factors that are specific to your mold, production requirements, and material compatibility. Here are some steps to guide you in choosing the most suitable mold coating:
Identify your specific needs: Determine the primary goal or problem you want to address with the mold coating. Are you looking to improve release properties, increase hardness, enhance wear resistance, or provide corrosion protection? Understanding your specific needs will help narrow down the options.
Consider the molding material: Different molding materials may have varying requirements in terms of surface finish, coefficient of friction, and release properties. Consult with the material supplier or review their design guides to understand their recommendations for mold coatings that work well with their specific materials.
Evaluate environmental factors: Consider the operating environment in which the mold will be used. Factors such as temperature, humidity, exposure to chemicals, and potential for corrosion should be taken into account. Some coatings may be more suitable for high-temperature applications, while others may offer better resistance to corrosive materials.
Assess coating properties: Look for coatings that offer the desired properties for your application. This may include low coefficient of friction, high hardness, excellent adhesion, wear resistance, chemical resistance, or specific surface finishes. Research different coating options and compare their technical specifications to find the ones that align with your requirements.
Understand coating application methods: Different coating technologies and application methods exist, such as physical vapor deposition (PVD), chemical vapor deposition (CVD), thermal spray, or plasma coating. Each method has its own advantages and limitations. Consult with coating suppliers or experts to understand the suitability of each method for your specific mold and production process.
Consider cost-effectiveness: Evaluate the cost of the coating itself, as well as any additional costs associated with surface preparation, application, and maintenance. Determine if the benefits provided by the coating justify the investment in terms of extended tooling lifespan, improved production efficiency, and reduced downtime.
Seek expert advice: Consult with mold coating suppliers, coating experts, or industry professionals who have experience in mold coatings. They can provide valuable insights and recommendations based on their expertise and knowledge of specific coating products and applications.