Based on their chemical make-up and processing methods, aluminum alloys may be classified as either cast or wrought. Based on their technical and service capabilities, wrought aluminum alloys may be classified into four distinct groups: antirust aluminum, duralumin, super duralumin, and forged aluminum.
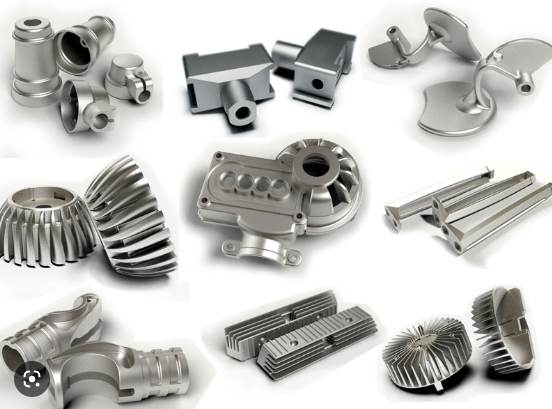
Aluminum that resists corrosion
Manganese and magnesium, both of which are found in Al Mn and Al Mg alloys, are the primary alloying components in rust-proof aluminum. We classify this aluminum alloy as one of the non-age-strengthening varieties. Once forged and annealed, it becomes a single-phase solid solution with excellent corrosion resistance and flexibility. Solution strengthening makes aluminum stronger when manganese is present, although manganese’s primary function is to increase the alloy’s resistance to corrosion. Manganese-containing alloys have high corrosion resistance because their second phase MnAl6 has chemical characteristics similar to aluminum’s. Magnesium has a stronger solution strengthening effect and does less harm to aluminum alloy’s corrosion resistance.
Aluminum that is resistant to rust has a high pressure tolerance and may be reinforced by cold pressure processing. Aside from its high weldability, it is also poorly machinable (because it is too soft). Pipes, tanks, nails for willows, and other low-stress components like these are often made from rustproof aluminum.
Duralumin
With only a little of manganese added to the mix, hard aluminum is essentially an AU Cu Mg alloy. There are other phases formed besides solid solution strengthening, such as CuA12( Phase), Al2CuMg (S phase), etc. Manganese is added to alloys to increase their resistance to corrosion; it also has a little solid solution strengthening effect, but due to its low precipitation propensity, it does not speed up the aging process. Duralumin of any kind may be aged to increase its strength, however the flexibility and corrosion resistance will suffer. The alloy’s strength will increase in proportion to the amount of copper and magnesium it contains. Duralumin is classified as willow joint (2A01, 2A10), medium strength (2Al1), separated strength (2A12, 2A06), or heat-resistant (2A07) according on the alloying degree, mechanical qualities, and technical features of the alloy (2A02).
Among deformed aluminum alloys, duralumin is now one of the most popular choices for aircraft construction. After heat treatment, its maximum strength may reach 500MPa, and it has excellent age hardening properties. Several airplane load-bearing parts are fabricated using this material.
Duralumin has a low resistance to corrosion, particularly in saltwater. Because of its greater steel content, intergranular corrosion is more likely to occur, since the electrode potential of copper-containing solid solutions and compounds is further from the grain boundary.
Superduralumin
The Al Cu Mg Zn system, including alloys like 7A04, is the primary component of super hard aluminum. The MgZn2 with a strong strengthening effect ( Phase) and the Al2Mg3Zn3 make up its aging strengthening division (T phase). Quenching and aging increase strength at room temperature
Strongest deformed aluminum alloy with tensile strengths above 600 MPa. This alloy has lesser heat resistance than duralumin and is more susceptible to stress corrosion and fatigue.
Aluminized steel
Alloys in the Al Mg Si Cu system and the Al Cu Mg Ni Fe system include wrought aluminum. This kind of aluminum alloy has high thermoplasticity and may be used to make a wide variety of forgings for the aviation industry, particularly those that are big in size and have complicated geometries due to the low presence of individual alloy components. Mg2Si, Al2CuMg, CuAl2, and other compounds may be produced by adding copper, magnesium, silicon, and other components to the alloy. The addition of iron and nickel to forged aluminum alloy raises the alloy’s service temperature, thus the name. 6A02, 2A50, 2B50, and 2A14 are the most prevalent types of aluminum alloys used for forging. In most cases, it is quenched and aged artificially before being made available.
Small amounts of transition group elements including manganese, chromium, germanium, and titanium are often added to aluminum alloys so that they can function at temperature separation. Recrystallization temperatures may be raised dramatically by dissolving these components into the matrix. In order to stop recrystallization and grain expansion, the scattered second phase must be precipitated. The temperature at which ice recrystallizes is another indicator of durability at high temperatures.
Wrought aluminum alloys with an excessive quantity of alloy elements will suffer a drastic reduction in alloy process fluidity and corrosion resistance, and may even be impossible to process using pressure. Consequently, the w (Cu) in wrought aluminum alloys is often between 5% and 8%, the w (Mg) is typically between 2.5% and 5%, the w (Zn) is typically between 3% and 8%, and the w (Si) is typically between 0.5% and 1.2%. Impurities including iron, silicon, and others are bad for wrought aluminum alloys.
Forgings in a wide range of forms and categories is possible since most wrought aluminum alloys are very malleable. Many forging processes, including as free forging, die forging, upset forging, roll forging, rolling, spinning, ring rolling, and extrusion, may be used to create aluminum alloy satin components. Aluminum alloys have a wide range of compositions, each of which results in a different flow stress. In each alloy, the maximum flow stress is around double the minimum (that is, the required forging load is about twice different)
Even though carbon steel has a higher flow stress than certain aluminum alloys, some low strength aluminum alloys, such as 1100 (equal to industrial pure aluminum 1200) and 6A02, have lower flow stresses. In contrast to carbon steel, the flow stress of high-strength aluminum alloys, notably Al Zn alloys like 7075 (LC4) and 7049 (LC6), is much greater. Flow stresses in several other aluminum alloys, such 2219 (LY16), are quite close to those in carbon steel. Though it is true that aluminum alloy is more challenging to forge than carbon steel and many alloy steels, it is evidently simpler to forge than nickel or cobalt based alloys and titanium alloys, particularly when isothermal die forging technique is used.
Based on its technical plasticity and mechanical qualities, wrought aluminum alloys may be classified into one of three groups. Medium strength and plasticity alloys include 2A14, 2B50, 2A70, 2A80, 2A02, 2A06, 2A11, 2A16, 2A17, 5A06, etc.; high strength and low plasticity alloys include 2A14, 2A12, 7A04, etc.; industrial pure aluminum is a good example of an alloy with both low strength and high plasticity. This diagram contrasts the relative ease with which 10 typical aluminum alloys may be forged.
The relative forgeability is calculated by considering the difficulty in obtaining specified deformation criteria and the likelihood to develop fractures, as well as the deformation string produced by each energy absorption unit of each of the 10 alloys in their respective forging temperature range. As the temperature rises, the forgeability of various aluminum alloys improves, as seen in the figure, although the effect of temperature is not uniform among alloys. For instance, as shown in the figure, the malleability of 4032 alloy with free silicon content is highly temperature dependent, whereas the malleability of high strength Al Zn Mg Cu system 7075 and other alloys is least impacted by temperature. A wide range of forgeability is seen in the figure for the different aluminum alloys.
The plasticity and resistance to deformation of aluminum alloys are significantly affected by differences in the kinds and amounts of alloy elements in different alloys, as well as the qualities, quantity, and distribution features of strengthening phases. Even while certain wrought aluminum alloys, such 1100 and 3003 (LF21), are far more malleable than the alloys shown in the figure, they are not useful in forging production because they cannot be reinforced via heat treatment. Poor fluidity is connected to the malleability of aluminum alloy and is another distinguishing feature of this material.
“Fluidity” refers to the alloy’s capacity to fill the forging die cavity when subjected to an external force. What matters most are the alloy’s resistance to deformation and its coefficient of external friction. Better fluidity is achieved by decreasing both the deformation resistance and the external friction coefficient. Because its deformation resistance is higher than that of steel and its external friction coefficient is bigger at the forging temperature, high-strength aluminum alloy has poor fluidity.