Until recently, metal surface processing has been limited to only four technologies. Metal surfaces have a great degree of smoothness because to these four processes. The surface of components must today not only be brilliant, but also robust, wear-resistant, corrosion-resistant, and most importantly, environmentally friendly and safe.
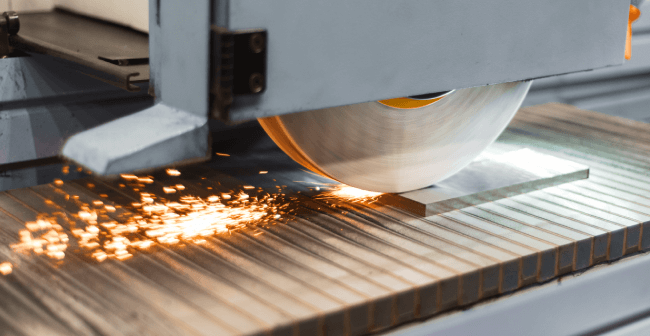
Metal may be polished in a number of ways
1. Polishing eliminates flaws from the surface and brightens it.
2. When removing and covering up certain machining flaws in aluminum alloy, blasting is often utilized. It may also be used to meet the aesthetic needs of a particular client’s completed product. Glass and tungsten sand, among other forms of sand, are among the materials used to express diverse emotions. Similar to ground glass, fine sand molds exhibit high-end items in a similar manner.
3. Electroplating may be used as a last step after polishing. The electroplating operation that came before this one may be seen in action here.
4. Reprocessing occurs after mold creation, and the process is known as “pattern reprocessing”. Adults have a very uniform texture.
5. Another word for rubbing lines is wiredrawing. Performance is like a smooth, uninterrupted line on the surface of a car. In contrast to the rubbing pattern, which is shown in straight lines, the vehicle pattern is depicted in a ring shape
6. Metal nameplates with inclined or straight filiform stripes representing the product or company name appear often. The batch blossoming process is shown in this way.
7. The results of edge trimming are similar to those of polishing and electroplating, despite the fact that they are achieved via different processes. This piece was created via mechanical processing, which resulted in a stunning light effect.
8. Oxidation may enhance the material’s physical properties and provide the desired color effect.
9. It takes a lot of time and effort to cut a diamond by hand.
Wires are often used in this manner.
Spiral lines, threads, ripples and spirals may all be used in wiredrawing in addition to the more traditional straight lines.
Straight line wire drawing is the mechanical drawing of straight lines on metal plates. For metal plates, it may be used to remove scratches, and for aluminum plates, it can be used to add decoration. Continuous wire drawing and interruptive wire drawing are two types of straight wire drawing. On an aluminum plate, a horizontal and straight-line action with a stainless steel brush or a cleaning cloth may make continuous silk lines (such as manual grinding under the condition of existing device or grinding on aluminum plate with a planer clamping a steel wire brush). It is possible to produce different thickness lines by varying the stainless steel brush’s wire diameter. Intermittent silk lines are often handled by brushing or texturing equipment. The assembly is finished by using two sets of differential wheels that rotate in the same direction. Unlike the rubber rollers at the bottom, the grinding rollers at the top rotate much more slowly. As they pass between the two sets of rollers, aluminum or aluminum alloy plates are brushed with fine, intermittent straight lines.
Brushing an aluminum plate with a high-speed copper wire brush creates an irregular matte wire pattern without any discernible lines. For this kind of processing, aluminum or aluminum alloy plates must fulfill strict surface requirements.
Brushing or texturing equipment is used to generate the bulk of corrugations. Grinding aluminum or aluminum alloy plate to form wavy lines with the axial movement of the top pair of grinding rollers.
In order to achieve the optical rotation, a cylindrical felt or stone grinding nylon wheel on a drilling machine is used to rotate and polish aluminum or aluminum alloy plates. The most popular uses of this instrument are circular signs and small decorative dials.
A little motor with circular felt connected to its shaft is positioned at a 60-degree angle to the table’s edge. A polyester sheet with straight edges adhered to the carriage, which features a fixed aluminum plate for pressing tea, restricts the thread’s width. Carriage’s linear movement in combination with felt’s rotation creates thread lines that spin and wipe across metal plate.
Sandblasting
Sandblasting is often used to remove material from metal surfaces. Some faults must be rectified or covered up while machining aluminum alloy. Products may seem less appealing if these defects are present.
The only method to remove Jinxiu, deburring, oxide layer, or surface pretreatment is to impact the accelerated abrasive particles on metal. This technique may modify the metal surface’s smoothness and stress condition. Glass sand, steel balls, carborundum, silicon carbide, and more are all popular sand materials.
Sandblasting has several benefits
Sandblasting is often done using air pressure spray guns and impeller shot blasting. Additionally, it may be used to remove burrs that arise after other processes like as die casting, stamping and flame cutting. There are a variety of thermal processes that may be used to remove the deoxidized skin that develops on the surface of cast iron or steel and the sand particles that are left over from the casting process. Remove the previous protective layer before applying the new one to achieve a lustrous surface while also hiding any casting imperfections, like as cracks or cold lines. Consequently, the surface is constantly roughened and sprayed with oil and other liquids. When high-stress metal components, such as springs and connecting rods, are repeatedly impacted locally, deformation and reinforcing occur. This strengthening effect can only be achieved using shot blasting equipment that uses round abrasives, such as stainless steel shot, or highly powerful sand blasting machines. To evaluate the machine’s surface strengthening influence and establish if the deformation meets the parameters, Almen test workpieces may be shot blasted or sandblasted.
Spray gun idea based on air pressure
Direct pressure cylinders and indirect injection are the two most common methods of supplying the spray gun with air pressure. Using the direct pressure cylinder, the pressure tank receives atmospheric pressure (about 6–7 bar). The disadvantage is that abrasive must be supplied to the pressure tank while the machine is not in operation. You may use a double pressure cylinder design if you need to do continuous sandblasting for a long time without stopping. In an indirect injection procedure, the abrasive is inhaled utilizing high-speed air flow. Abrasive addition doesn’t disturb ordinary manufacturing, and the equipment is simple, thus it’s the most common approach to use.
The sand blasting chamber type is the simplest of the several types of sand blasting machines. Rubber gloves and a spray cannon switch allow you to see sand pour out of the item while you hold it in your hands. Spray cannons like this one are often used in impeller shot blasting. Spray guns and workpieces typically have a distance of 150-200mm and a processing diameter of 30mm, respectively. Dry and wet sand blasting methods are also available. Dry and direct pressure vacuums, for example, are two different types of pressure vacuums. This absorbs abrasive instantly for on-site repair. Wet pressure is an indirect injection technique that may result in a more detailed surface texture when using a combination of water and fine abrasive. In contrast, there are significant disadvantages to using wet sand blasting. It is impossible to utilize steel shot as an abrasive on a ferrous metal workpiece, hence the treatment time is longer. As long as the process parameters are properly handled, the effects of most wet sandblasting may be replicated using dry sandblasting.
This is the underlying premise of shooting
Shot blasting relies heavily on the rotational speed of the impeller. Pre-accelerated by regulator and impeller pusher, the abrasive is delivered to the high-speed region of the blades, where it is discharged at high velocity. The vehicle can reach speeds in excess of 100 miles per hour. Due to the large area covered by shot blasting, the energy efficiency is much larger than that of a spray gun. The shot blasting machine’s heart, the impeller, is driven by an electric motor. A single disc impeller or a double disc impeller may be made by any company.
While a four-to-eight-blade impeller is common, the double disc impeller is a heavyweight, but the blades are easy to load/unload and the abrasive dispersion is exact. Either a straight or an arced blade may be used. Blades with a straight body are simple to load and unload, and they don’t need a handle to do so. However, despite its cheap cost and poor throwing speed, this blade type is often used because to its narrow cleaning range (see figure below). While loading and unloading the curved blade might be a hassle, its large cleaning area and high throwing speed make it well worth the effort.
When selecting where to place an impeller in a shot blasting chamber, there are a number of extra considerations to keep in mind. Area covered, distance from workpiece, mobility of workpiece, secondary rebound coverage and the simplicity with which maintenance and replacement may be carried out are all elements to consider. Slanted impellers and many modest power impellers are more versatile and effective than a single high-power impeller, according to experience. The shot-blasting process’s impeller and lining steel plate are especially subject to wear, hence their lifespan is crucial. With 48hrc steel sand, the high chromium cast steel impeller has an approximate service life of 800 hours, while the steel shot has an approximate service life of 1500 hours. With a service life of up to 4000 hours, the impeller is built to last.
Adsorption of oxygen in the atmosphere (coloring)
Aluminum and aluminum alloys are becoming more popular since they are less expensive to manufacture and lighter in weight than other metals. In order to protect aluminum and aluminum alloys against chemical reactions, a variety of techniques are available, such as electroplating, spraying, organic protection, and oxidation treatment. Anti-environmental pollution measures are commonly referred to as “oxidation treatments.”
It is possible to break down alkali oxidation into chemical and electrochemical processes (commonly known as anodic oxidation). Aluminum and similar alloys may be electrochemically oxidized, a process known as anodic oxidation, to increase their corrosion resistance and aesthetic appeal. What you’re seeing here is electroplating done backwards, if you will. Electrolytic circuit anode is the workpiece. You don’t need to cover aluminum with a coating of material if you want to protect it against corrosion (metal).
Because of its thinness, softness, and lack of wear resistance, the chemical oxide layer’s corrosion resistance is poorer than that of the anodic oxide film. The bottom layer for painting and plastic spraying is often used because of its great adsorption capacity. Aluminum anodic oxide film outperforms chemical oxide film in terms of overall performance, which explains why it is so widely used. Among its attributes are the following:
Corrosion resistance of a substance. Film thickness and quality seals directly affect service life.
The ability to stand up to wear and tear. The substrate has an HV100 hardness rating, whereas the typical anodic oxide layer has an HV300 rating and the hard film has an HV500 rating. Consistently high hardness and wear resistance.
It’s only for show. It not only retains the metal’s brilliance and texture, but it may also be dyed in a variety of vibrant hues.
Electroplating layer adhesion to the organic layer. An excellent method for enhancing the surface layer’s adhesion and corrosion resistance.
Insulation of electrical conductors. Aluminum is an excellent conductor, while oxide film is a high-resistance insulator in the film world. The breakdown voltage of the insulation may reach 30200 volts/um, while the volume resistivity is 109 ohms/cm3 at ambient temperature. It may attain a temperature of 1013 /cm3 at 3250 °C.
Transparency is essential in this regard. Higher aluminum purity results in a film that is more transparent.
Usefulness. Functional particles may be placed in micropores using the porosity of an oxide layer as a template.
It’s possible to get a wide range of shades from aluminum anodizing
Apply a protective oxide coating to the aluminum’s surface by submerging it in the proper electrolyte and connecting it to the anode. As a result of these modifications, In this case, 2 Al + 3 [O] = Al2O3.
Alkali washing is used in the oxidation of aluminum. Washing in water, Bleaching with Chromic Anhydride, Washing in Water, Oxidation of Aluminum, Washing in Water, Dyeing, Washing in Water, Sealing, and Drying