There was a surge in the quantity of castings made in West Africa beginning in the 11th century. The process of investment casting became popular among sculptors and painters in the 16th century. Among Benvenuto Cellini’s many impressive creations is a bronze figure of the variable star Perseid Cepheid and the Banshee commander. Today, we break down the history and development of investment casting.
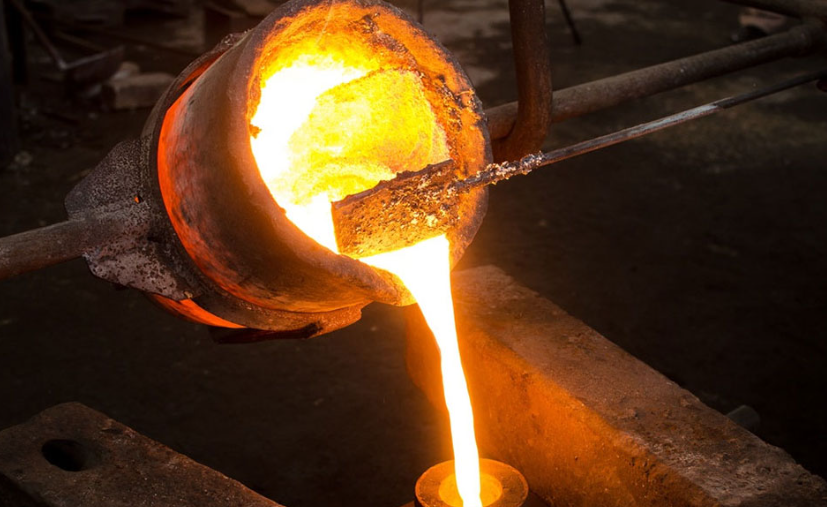
Investment Casting: How It Evolved Over The Years
Eastern Heaven Records, authored by Zhao Xihu during the Southern Song Dynasty (1127-1279 AD) in China, is the first known written record of wax lost castings. There was also VaVrinec Krickes’ “Cannons, Balls, Chasing Cannons, Bell Casting and Preparation Guidance” from the middle of the 16th century, Song Yingxing’s “Enlightenment of the Heavenly Palace” from the Ming Dynasty, and Cai Lini’s thesis from 1568.
Dental investment casting, which combines centrifugal casting technique with dental castings, emerged around the end of the 19th century. Research into the elements that determine the dimensional stability of wax molds and shells, as well as the solidification and shrinkage qualities of particular metals and alloys, started in the early 20th century so that thicker dental components could be manufactured. The components of investment molding were modified in the early 1930s. More than 400 patents were issued in this subject between the years 1900 and 1940. The jewelry business also makes extensive use of investment casting.
Aeroengine components (such turbochargers) subjected to extreme conditions cannot operate to specifications if conventional alloys are employed. At the tail end of the 1930s, Austin Laboratory’s drilling base alloy for surgical transplants was discovered to have good performance at high temperatures and might be utilized for turbochargers. Since this alloy is so challenging to work with, investment casting has emerged as a viable processing option for creating it. The country has quickly advanced industrial technology, joined the aviation and national defense sectors, and applied that technology to other disciplines.
Since the 1940s, when investment casting was first put to use in mass manufacturing, the process has advanced at a rapid clip. In 1996, it was estimated that 50% of the global investment casting industry was located in North America, 25% in Europe, and 20% in Asia. The three largest contributors are the USA, China, and USA together accounting for 95%. 42% are British, 26% are French, 19% are German, 7% are Italian, and 6% are from elsewhere in Europe. The amount of money made by investment casting in the US was $2.61 billion. Sales of investment castings in the United States reached $250 million in 1970 and $1.1 billion in 1980, an increase of 10.4 and 2.37 times, respectively. Progress in the sector is swift.
Investment casting is widely utilized nowadays, notably in the electrical, petroleum, chemical, energy, transportation, light, textile, pharmaceutical, medical, pumps, and valves sectors.
Progress in Investing Casting Technology
Investment castings have advanced rapidly as a result of their technological advancement and development. The technology behind investment casting has come a long way. Water-soluble cores, ceramic cores, improved metal materials and large-scale investment casting technology, titanium alloy investment casting, directional solidification and single crystal casting, filtering technology, hot isostatic pressing, rapid prototyping technology, computer applications in investment casting, and mechanization are all examples of new materials, processes, and equipment that have had a significant impact on the evolution of investment casting.
Investment castings used to only be able to manufacture tiny castings, but with the advancement of technology, this is no longer the case. The biggest investment casting comes in at over 2 meters in outline size, with a wall thickness of less than 2 millimeters. Investment castings, meanwhile, are becoming more precise. Better geometric tolerance is possible, in addition to better linear tolerance, for many components. Recently, investment castings have achieved a surface roughness of Ra0.4um, which is an all-time low.
The mechanical qualities of castings are also increasing in quality as a result of technological advancements and material advancements. Blades for turbines are a nice illustration of this. Advances in materials and technology have led to a notable rise in turbine blade efficiency. Turbine blades (American brands) were made from IN100 and B1900 in the 1960s and ’70s, MM200 and ‘247 in the ’80s, and PWA1480 in the ’90s. Also, as the science of solidification has advanced, turbine blades have gone from being made of equiaxed crystal (EQ) to being made of directionally solidified columnar crystal (DS) to being made of expanded single crystal (SC) blades, making them increasingly crucial. From 980 degrees Celsius, we raise the operating temperature to well over 1100 degrees Celsius.
Titanium alloy, a crucial structural element in contemporary industry, can now be cast utilizing investment casting technologies to provide intermediate housing for aviation engines, compressor housings, and even medical implants. Specifically, the development of large-scale integrated titanium investment casting has allowed for the replacement of assembly elements, the decrease in overall machine weight, an increase in durability, and successful outcomes. The biggest titanium investment casting hub ever made was reportedly 1.918 meters in diameter and 0.591 meters in height and weighted 340 kg after welding in 1992.
There has been extensive use of hot isostatic pressing (HIP) technique in turbine blades and other investment castings. Metal creep and plastic deformation are used in conjunction with high heat and pressure to fix flaws like hot cracks and sloppiness in castings. After processing, the casting’s density may approach the metal’s theoretical density, boosting its performance. HIP can increase the high temperature and low frequency fatigue properties of nickel base superalloys, titanium alloys, and aluminum alloys by a factor of three to ten; it can increase the durability of nickel base superalloy and titanium alloy by a factor of more than two; it can increase the performance of the casting while decreasing the dispersion by a factor of six.
Investment casting is paired with rapid prototyping technology (RPT), which debuted in the 1980s, to reduce the manufacturing cycle and simplify the process. To increase market competitiveness, RPT utilizes solid lithography (SLA), selective laser sintering (SLS), the fused deposition manufacturing technique (FDM), and layered solid manufacturing (LOM) to create plastic, wax, and paper prototypes in place of conventional wax models.
The previous belief that investment in the casting process cannot be automated has been disproved by the advent of mechanization and automation. Utilizing investment casting technology, Japan, the United Kingdom, and the former Soviet Union have been able to effectively manufacture inexpensive vehicles and other civilian components.