Introduction To Die Casting: What Is It, Features, Structure, Common Defects & More
With the rapid development of automobile, electronics, communication and other industries, driven by the trend of global economic integration, the focus of global die casting production has gradually shifted to China, coupled with China’s unique advantages in labor and resources, the domestic die casting industry shows a trend of rapid development, but some people are unfamiliar with the word die casting. Here is an introduction to die casting, characteristics, structure, composition, classification and common defects of die casting.
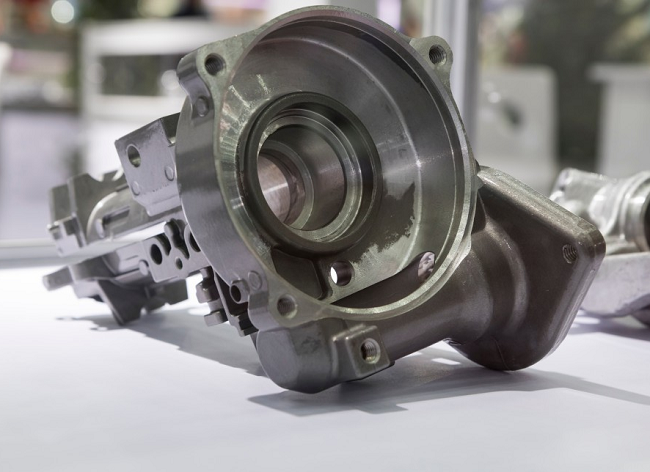
What Is Die Casting?
Die casting is a casting method in which molten alloy liquid is poured into the pressure chamber, the cavity of steel mold is filled at high speed, and the alloy liquid solidifies under pressure to form castings. The main characteristics of die casting different from other casting methods are high pressure and high speed.
Die casting machine, die casting alloy and die casting mold are the three elements of die casting production. The so-called die casting process is the organic and comprehensive application of these three elements, so as to produce castings with good appearance, internal quality and size in line with the requirements of drawings or agreements stably, rhythmically and efficiently.
Features Of Die Casting
(1) The casting has high dimensional accuracy and low surface roughness.
(2) High casting strength and surface hardness.
(3) Wide range of die casting (lamps, lighting, motor vehicle furniture, office supplies, bathroom hardware, electrical accessories, clothing, building materials, tableware, toys, gifts, mechanical hardware).
(4) High productivity.
(5) High metal utilization.
The Main Problems Currently Existing In Die Casting
1. As the alloy liquid pressed into the mold is generally rapidly cooled and solidified under non vacuum conditions, if the casting is improper, the casting is easy to produce defects such as pores and water marks.
2. High temperature heat treatment and welding cannot be carried out for products produced by ordinary methods.
3. At present, it is difficult to die cast some concave parts and high melting point alloy castings.
4. Die casting equipment is expensive, and mold manufacturing requires a certain period, so it is not suitable for single piece or small batch production. Only in mass production can it have good economic benefits.
How To Reasonably Select Die Casting Alloy
(1) It can meet the performance requirements of die castings.
(2) Low melting point, small crystallization temperature range, good fluidity at temperatures above the melting point and small shrinkage after solidification.
(3) It has sufficient strength and plasticity at high temperature and low thermal brittleness.
(4) Good physical and chemical properties, such as wear resistance, conductivity, thermal conductivity, corrosion resistance, etc.
(5) good processing performance.
Composition And Classification Of Die Casting Machines
1. Closing mechanism
2. Injection mechanism
3. Hydraulic system
4. Electrical control system
5. Parts and base
Classification of die casting machine:
– Hot chamber die casting machine: Zinc, magnesium, etc.
– Cold chamber die casting machine: Zinc, magnesium, aluminum, copper, etc.
– Vertical die casting machine: Zinc, aluminum, copper, lead, tin.
The difference between hot chamber and cold chamber is whether the injection system of die casting machine is immersed in metal solution.
It can also be classified as horizontal and vertical. The horizontal is lying horizontally and the vertical is vertical. The hot chamber die casting machine must be horizontal, and the cold chamber die casting machine may be vertical or horizontal, but the vertical die casting machine must be cold chamber.
Structure Of Die Casting Mold
– Steel (hot working steel) selected for die casting die: H, high-quality steel, SKD, DAC, FDAC.
– Mold structure: Mold base, mold kernel, guide column, guide sleeve, thimble, cylinder, splitter, gate sleeve, slider, inclined guide column, oil pressure core pulling.
– Die processing equipment: Milling machine, CNC machining center, wire cutting, spark machine grinder, lathe welding, repair equipment.
Post-Treatment Equipment And Processes Of Die-Casting Products
– Post processing equipment: Polishing machine, shot blasting machine, vibration grinder, punch drilling machine, tapping machine, CNC machining center, surface treatment.
– Surface treatment process: Spraying, baking, electroplating, anodizing, infiltration, oil spraying and sand blasting.
Common Defects Of Die Casting Products
1. Surface defects: Water marks, sand holes, cold shuts, bubbles, cracks, shrinkage, carbon deposits, discoloration of burrs, oxidation, die sticking and strain.
2. Internal defects: Insufficient filling and mechanical properties.
3. Dimensional defects: deformation, dimensional deviation.