The fabrication of forgings is a significant source of blanks for machine components for many different industries. Aluminum alloy is produced at a rate second only to steel’s, and it is one of the most commonly utilized nonferrous metals. Forging an aluminum alloy has several benefits. When aluminum alloy is forged, the metal structure is altered, which may greatly enhance the material’s performance. Here we talk about the characteristics of aluminum alloy forging process performance.
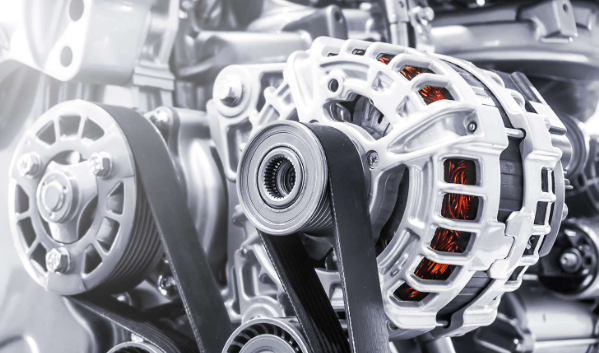
Using a forging method on aluminum alloys
Making forgings is a crucial part of the manufacturing sector. Forging is also often done using aluminum alloy. To the same extent that low carbon steel may be forged, so can aluminum alloy. Large-scale production of safety components like forgings makes good internal quality of aluminum alloy materials essential.
Alloy melting, casting, extrusion, forging, heat treatment, and machining are the typical key production processes for forged aluminum alloy components. Stability in the alloy manufacturing process calls for stringent management of a wide range of variables, including but not limited to: alloy smelting composition ratio, degassing, filtering, casting inverse segregation, extrusion process quality, forging (aluminum alloy forging) metal streamline, heat treatment temperature, time, grain size control, size accuracy, etc.
Characteristics of Aluminum Alloy Forging
1.A limited temperature window in which forging deformation may occur in aluminum alloys
Most aluminum alloys have a forging deformation temperature of between 350 and 450 degrees Celsius, with a range of roughly 100 degrees Celsius. Some alloys can be deformed between 50 and 70 degrees Celsius, and forging operations may be performed in a short amount of time. This will likely cause significant complications in the forging process. Increasing the forging heat and preheating the tools and dies to a higher temperature, as well as heating the blank to the top limit temperature, will allow for a longer forging time.
2. Vulnerable to the speed of change
Forging aluminum alloy requires equipment with a low operating speed and consistent speed because to the material’s sensitivity to speed change rate. In order to avoid forging fractures in the ingot, low-speed, compressive-stress opening of the billet by extrusion, forging, or rolling is often used. There isn’t much wiggle space when it comes to choosing forging equipment, and aluminum alloy die forging is frequently needed to be done on hydraulic press or mechanical press rather than forging hammer type forging equipment.
3. Strict temperature regulations for heating and forging
Due to the limited forging deformation temperature range of aluminum alloys, the forging operation time must be maximized by heating the material to the maximum permissible deformation temperature, which necessitates the use of a high-precision heating furnace and temperature control device.
After bloom, most aluminum alloys have a high plasticity that makes them resistant to forging and cracking. However, significant deformation should be avoided throughout the forging process to prevent excessive overflow, which may have negative effects on the forging’s structure and performance. High-velocity forging (with a forging hammer, for example) and substantial deformation must be used if the procedure is neglected. Overheating, caused by the heat energy translated by a huge quantity of deformation energy, may lead to an unqualified structure and performance in the forging.
4. High thermal conductivity
There is a three to fourfold increase in heat conductivity between aluminum alloy and steel. The blank can be heated in a high-temperature furnace without being preheated, which is an advantage. However, this method also has some drawbacks, including uneven deformation due to a large temperature difference between the forging’s interior and exterior, and the easiness with which this can lead to local critical deformation and, ultimately, coarse grain in the forging’s surface. Rapid heat dissipation and large friction on the blank surface, as well as uneven deformation of the inner and outer layers falling into the critical deformation zone, may be responsible for the common coarse crystal rings on the surface of extruded bars in most aluminum alloys, especially aluminum manganese alloys with extrusion effect. The mold and any tools that may come into contact with the workpiece must be warmed to 300 °C or greater to avoid excessive heat loss.
5. High coefficient of friction and low fluidity
Aluminum alloy has a high friction coefficient with steel dies, and its fluidity is low during deformation, thus it has trouble filling the die groove during the forging process. Increasing the work steps, dies, and fillet radius of the calibrating tool is often required.
6. Strong adherence
The viscosity of aluminum alloy is rather high. Bonding the blank to the die is common in high-deformation forging, however it may lead to faults like peeling and warping in the forging and wear on the die. If the damage is too great, the forging and the die will be thrown away.
7. Sensitivity to cracking is high
Cracks in aluminum alloy are easily seen and heard. Forgings must be scrapped if the fractures produced during the process are not cleaned in a timely manner, since the cracks will quickly develop during successive forging.