CNC machining center is commonly used for mold making, which has a high level of automation and can be controlled by programming, it is more complex than ordinary lathes and mills. In the process of mold making, how to use the CNC machining center correctly? Below are some key points you should know.
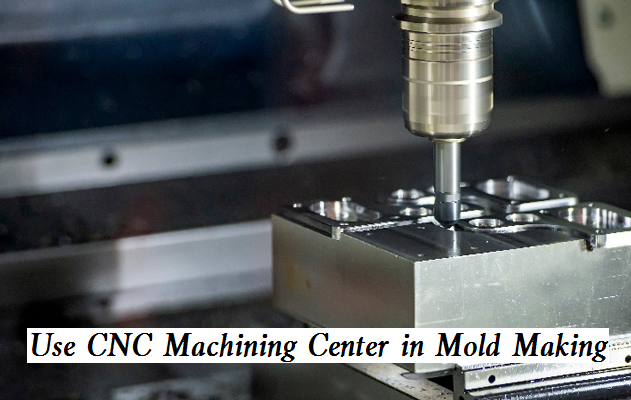
How to Use CNC Machining Center Properly in Mold Making
Mold is a variety of tools used in industrial production to obtain required products by die casting, injection molding, blow molding, extrusion, forging molding, stamping, and other methods. In short, a mold is a tool used to make shaped objects.
In order to ensure the quality and accuracy of products in the process of mold production, CNC machining centers should strictly follow the operating instructions. Before use, equipment should be checked and unqualified products should be handled in a timely manner, which can reduce losses and extend the service life of the equipment.
1. When the ball nose milling cutter is milling curved surfaces, its cutting speed at the tooltip is very low. If the ball end milling cutter is perpendicular to the surface to be machined to mill a relatively flat curved surface, the surface quality cut by the ball nose milling cutter tip is relatively poor, so the spindle speed should be appropriately increased, and cutting with the tooltip should also be avoided. Compared with traditional machining methods, CNC machining has higher requirements for tools. It requires not only good rigidity and high accuracy, but also stable size, high tool life, and convenient installation and adjustment to meet the requirements of high efficiency of NC machine tools. The tool materials used on CNC machine tools are usually suitable for high-speed cutting, and indexable inserts are used.
2. Avoid cutting vertically. There are two kinds of flat bottom cylindrical milling cutters. One is that the end face has a central hole, and the end edge is not at the center. The other is that there is no central hole on the end face, and the end edges are connected and pass through the center. When milling curved surfaces, the end milling cutter with a central hole must not feed vertically downward like a drill, unless a process hole is drilled in advance. Otherwise, the milling cutter will be broken. If the end cutter without a central hole is used, it can feed vertically downward, but because the blade angle is too small and the axial force is large, it should also be avoided as far as possible.
3. In case of poor heat treatment, cracks, uneven organization, and other phenomena found in the milling of curved parts, the processing should be stopped immediately to avoid wasting working hours.
4. CNC machining centers generally need a long period when milling complex curved surfaces of mold cavities. Therefore, the machine tools, fixtures, and tools should be properly checked before each start of milling to avoid midway failures, affecting the machining accuracy, or even causing waste products.
5. When the CNC machining center is milling the mold cavity, the filing allowance shall be properly controlled according to the roughness of the machined surface. For parts that are difficult to mill, if the machined surface roughness is poor, more filing allowance shall be reserved appropriately; For easy machining parts such as plane and right angle groove, the surface roughness value shall be reduced as far as possible to reduce the filing workload and avoid affecting the accuracy of cavity surface due to large area filing.