How to Select the Best Die Casting Machine - Die Casting Machine Buying Guide
Manufacturers that produce and supply various die casting machines are investing heavily in developing new technologies and manufacturing equipment to maintain their competitiveness. How to select a die casting machine and what should you consider? In this article, we’ll get into key factors that matter the selection or buying of die casting machines.
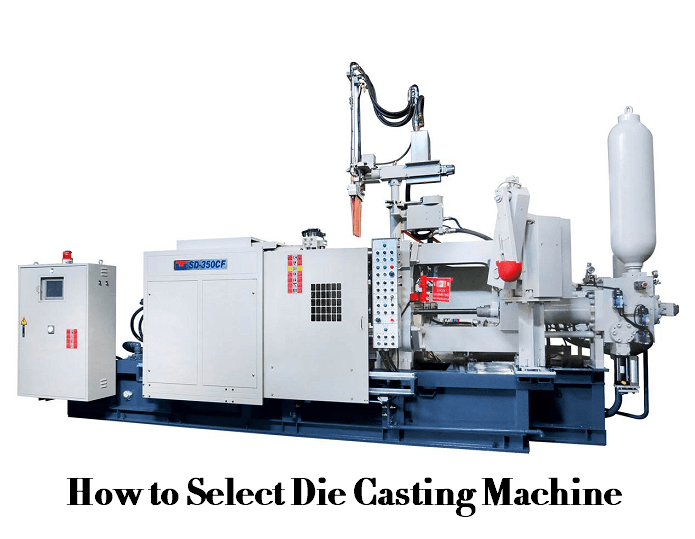
How to Select the Best Die Casting Machine - Die Casting Machine Buying Guide
1) In the actual production, the selection of die casting machine is mainly based on the type of die casting alloy, the size and weight of the casting, then determine the hot chamber or cold chamber die casting machine. Hot chamber die casting machine is usually used for zinc alloy castings and small magnesium alloy castings. Cold chamber die casting machine is mainly used for aluminum alloy, copper alloy and large magnesium alloy castings. The vertical cold chamber die casting machine is suitable for die castings with central radial and cylindrical shapes and with a central runner.
2) According to the material, size, average wall thickness, and net weight of die casting, the model and specification of the die casting machine are selected. The actual process parameters, such as clamping force, pouring amount per time, and injection chamber fullness, can be obtained by calculation, which can be used as the basis for selecting the machine.
3) The size of the die casting mold should match the corresponding installation size on the die casting machine. The main size is the thickness of the die casting mold and the distance between the parting surfaces of the die. It must meet the requirements of the basic parameters of the die casting machine.
– Die casting die thickness (H) shall not be less than the minimum die thickness given in the machine manual, nor greater than the maximum die thickness given.
– After the die casting machine is opened, the distance between the parting surfaces of the die casting die should be greater than or equal to the minimum distance to take out the casting.
Die Casting Machine Selection Tips
1) According to the casting technical requirements, service conditions, and die casting process specifications, the technical parameters and processability of the die casting machine are calculated.
2) According to the technical parameters and process requirements of the die-casting mold, the die casting process parameters and the die casting mold dimensions are calculated.
3) Evaluate the working performance and economic effect of die casting machine, including yield, qualified rate, productivity, stability, reliability and safety of operation, etc.
4) For multi-variety and small batch production, the die casting machine with a simple hydraulic system, strong adaptability, and quick adjustment should be selected. For small variety and large batch production, the high efficiency die casting machine with various mechanized and automatic control mechanisms should be selected. The special die casting machine can be used for the single variety castings produced in large quantities.
5) The shape, size, weight, and wall thickness of casting have an important influence on the selection of die casting machine.
6) The casting weight (including gating system and overflow tank) should not exceed the rated capacity of the die casting machine, but also should not be too small, so as to avoid the waste of power of the die casting machine. The rated capacity of a general die casting machine can be found in the manual.
7) Die casting machine has a certain maximum and minimum distance, so the die thickness and casting height must have a certain limit. If the thickness or casting height is too large, the casting part may not be taken out.