During the current die-casting process, aluminum alloy die castings and their subsequent processing can not avoid the generation of burrs and edges, and the removal of burrs takes a large number of processing times. What causes burrs during die casting and how to remove aluminum/zinc die casting burrs quickly and efficiently?
Aluminum alloy die castings produced by the die casting process are often accompanied by useless accessories not required by the drawings. The extra part is also known as burr, flash, etc. When aluminum or zinc die castings are processed, they often produce sharp edges and burrs.
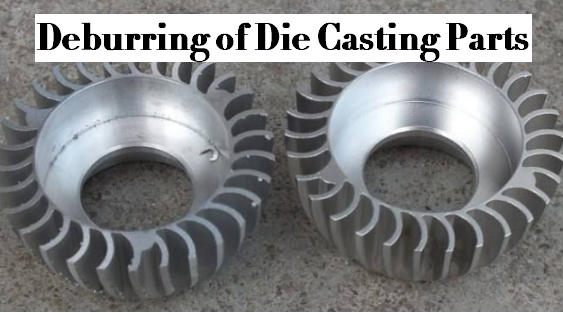
What Causes Burrs During Die Casting Process
Burrs are often seen on the parting surface of die casting dies, and sometimes in the aged cracked die. As for precision aluminum alloy die castings, the reasons for sharp edges and burrs are rough as follows:
1. The customer’s product design structure is too complex or unreasonable, which is difficult to correct through mold design.
2. Defects in structural design of die casting die.
3. During the manufacturing process of die-casting die, illegal operation or unreasonable processing technology, such as heat treatment not in accordance with the specifications, resulting in insufficient hardness, which is easy to cause die meat deformation.
4. Whether the internal metallographic structure of die casting die materials meets the requirements – powerful aluminum alloy die casting factories will check the metallographic structure of die materials. If they do not meet the requirements, they will not be used.
5. Improper selection of aluminum material and poor fluidity.
6. Improper maintenance of die-casting die, failure to clean up the sundries in the cavity according to the operation specifications, or failure to match the die.
7. The selection of aluminum alloy die casting process parameters is not appropriate, such as too high casting pressure – domestic aluminum alloy die casting factories generally prefer high-pressure and high-speed production of aluminum alloy die castings, so the service life of die casting dies will be greatly reduced.
8. During the production of aluminum alloy die casting, the alloy materials on the die surface are not cleaned regularly.
In the process of aluminum alloy die casting, it is normal to generate burrs through the exhaust block, which helps to exhaust the gas in the mold cavity and reduce the internal pores of the product. However, due to poor sealing at other positions of the mold, more burrs are generated with die casting, energy loss and the high-pressure situation of aluminum alloy die castings is lost, which will not only lead to shrinkage in the product and mass scrapping, It will also fly during the die casting process, endangering the personal safety of employees, and measures should be taken to avoid it.
How to Remove Burrs from Die Castings - Deburring Methods of Die Casting Parts
The burrs of aluminum alloy die casting will directly affect the quality of products. Therefore, how to remove it efficiently is a major problem in die casting plants. There are more than 60 methods to remove the burr, here are some of the options.
1. Use the blanking die
When designing the blanking die, the removal of the burr of aluminum alloy die castings are taken into account, and the profiling knife edge is designed. While cutting off the nozzle and slag ladle overflow port, it is cut off together with the product edge, so as to avoid multiple clamping and reduce manual operation, which will greatly improve the efficiency.
2. Deburring manually
The advantages of manual deburring and cutting are less investment at one time and simple and easy purchase of tools – steel file, sandpaper, and other simple abrasives and abrasives; In addition, the requirements for personnel are not high, flexible, and flexible. Its disadvantage is low efficiency and related to the proficiency of workers; After deburring, the surface finish is not easy to master, and the workers who work for a long time are easy to be tired and easy to miss; Some tools have high noise, others are not wear-resistant, and there is a lot of dust and a high-risk factor.
3. Deburring by shot peening
The main function of shot peening is to strengthen the product surface, but it can play the role of knocking off the burr of aluminum alloy die castings. Of course, while reducing the hours of manual deburring, the “side effects” of peeling aluminum alloy die castings also need to be removed.
4. Machining to remove casting burr
For some aluminum alloy die castings, when processing products, add the processing burr program to remove the burr casually, which reduces the labor cost. Therefore, machining can reduce the dependence on labor and improve production efficiency.
5. Ultrasonic deburring of the workpiece
The ultrasonic energy generated by the ultrasonic wave acts on the liquid. If the liquid is in a sparse state, it will be torn into small holes (i.e. the interior is a vacuum). When these holes break, they will produce up to hundreds of atmospheres. Ultrasonic deburring is to remove the burrs attached to the parts by using the instantaneous huge impact force generated by the “cavitation phenomenon”. Ultrasonic deburring is not suitable for all aluminum alloy die castings, mainly for some micro burrs.
6. Electrolytic deburring
Electrolytic deburring is a machining method to remove the burr of metal parts by electrolysis, which is called ECD for short. Electrolytic deburring is similar to EDM. The tool cathode (usually brass) is fixed near the burred part of the machined workpiece, with a gap of about 0.3 ~ 1mm. The conductive part of the tool cathode is aligned with the burr edge, and other surfaces are covered with an insulating layer to make the electrolysis concentrated on the burr part. Electrolytic deburring is suitable for removing the burr of cross holes in hidden parts or parts with complex shapes. It has high production efficiency. The deburring time generally takes only a few seconds to tens of seconds. This method is often used to deburr gears, splines, connecting rods, valve bodies, and crankshaft oil circuit orifices, as well as sharp corners and rounding.
7. Magnetic deburring machine
The magnetic deburring machine uses its unique magnetic field distribution to produce a strong and stable magnetic induction effect, so that the magnetic steel needle (semi-permanent) and aluminum alloy die casting can be fully ground in an all-round and multi-angle, so as to achieve the effects of rapid rust removal, dead angle removal, deburring and cutting edge removal, oxidation film removal and mold burning trace removal.
8. Deburring of aluminum alloy die castings by the thermal explosion
Thermal explosion deburring, also known as electrothermal deburring, is an advanced process recognized by the world machinery manufacturing industry as the most suitable for deburring small workpieces in large quantities. It uses hydrogen and oxygen to mix in the closed working chamber used to treat the workpiece, ignites and burns instantaneously, and has a violent thermochemical reaction with the burr on the workpiece surface in a very short time, so as to achieve the purpose of burr removal.
9. Chemical deburring
In the mechanical manufacturing industry, the requirement of deburring precision parts is very high, among which the deburring requirement of precision parts commonly used in the hydraulic system is the highest. They require removing edges and burrs at the working shoulder of the valve body and valve sleeve and maintaining sharp edges and a small rounding radius. In order to meet these requirements, we must find a good and suitable deburring method – Chemical deburring is one of the good choices.
10. Automatic deburring machine
An automatic deburring machine is a typical mechatronics device. It comprehensively uses the latest research results of many disciplines, such as machinery and precision machinery, microelectronics and computers, automatic control and drive, sensors and information processing, artificial intelligence, and so on. With the development of the economy and the improvement of automation requirements of all walks of life, the technology of automatic deburring machines has developed rapidly, A variety of deburring machine products have emerged.