How Is Cutting Tool Broken When Processing Zinc Alloy Die Castings
Blade failure and its adverse effect on zinc alloy die casting are similar to athletes wearing a pair of high-quality running shoes. Just as shoes bear the weight of athletes, blades repeatedly bear great stress, resulting in wear and loss. If not solved, wear will make athletes feel pain and reduce the machining accuracy and productivity of die casting plants. However, die casting factories can analyze the tools used to prolong the tool life and predict the use of tools as much as possible, so as to maintain the accuracy of zinc alloy die castings and reduce the decline of equipment performance. Early blade inspection is essential to determine the root cause of failure because it is easy to observe and report at this time. If these important steps are not taken, it is possible to confuse different types of failure modes. In order to facilitate blade inspection, a stereomicroscope can be used. The stereo microscope has good optical characteristics, sufficient illumination and at least 20 times magnification, so it is very beneficial to identify the failure modes leading to premature wear of the blade.
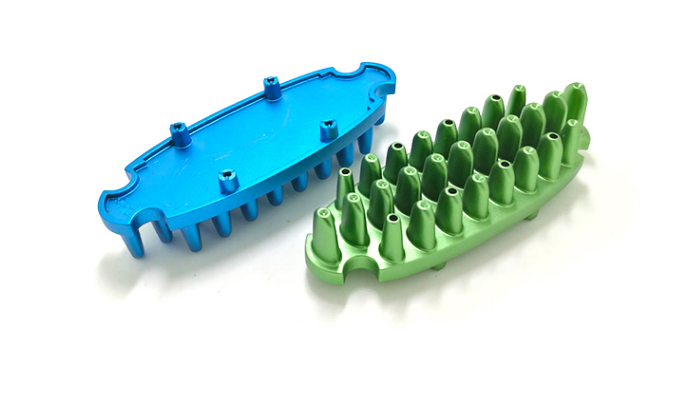
Causes To Tool Broken When Processing Zinc Alloy Die Castings & How To Prevent
1. Flank Wear
Normal wear of any type of material can cause blade failure. Normal flank wear is the most popular form of wear because it is the most predictable type of tool failure. The wear of the flank is generally very uniform. It gradually appears with the wear of the machining material and the cutting edge, which is similar to the blunting of the cutting edge.
Normal flank wear occurs when hard fine inclusions or work hardened materials in zinc alloy die castings cut into the blade. The causes of this wear include abrasive wear during low-speed cutting and chemical reaction during high-speed cutting.
When identifying the normal flank wear, it will be found that a relatively uniform wear mark is formed along the cutting edge of the blade. Sometimes, the metal on the zinc alloy die casting will scratch the cutting edge, exaggerating the apparent size of the blade wear mark.
In order to slow down the normal flank wear, it is important to adopt the hardest blade material grade without micro collapse, and use the lightest cutting edge to reduce cutting force and friction.
On the other hand, the rapid wear of the flank will reduce the tool life and cannot reach the typical cutting time of 15 minutes. Rapid wear often occurs when cutting wear-resistant materials, such as nodular iron castings, aluminum alloy die castings, zinc alloy die castings, superalloys, precipitation hardening (PH) stainless steel after heat treatment, beryllium copper alloy and tungsten carbide, and when cutting non-metallic materials, such as glass fiber, epoxy resin, reinforced plastics and ceramics.
Signs of rapid flank wear are similar to normal wear. In order to correct rapid flank wear, it is important to select a more wear-resistant, harder or coated cemented carbide blade material grade and ensure that appropriate coolant is used. Reducing the cutting speed is also very effective, but it does not meet the production needs, because it will have an adverse impact on the machining cycle of zinc alloy die castings.
2. Crater
Crescent depression is common in high-speed machining of iron-based or titanium based alloys. It belongs to the thermal / chemical problem that the blade dissolves into the chip of the workpiece.
Diffusion wear and abrasive wear cause crescent depression. When machining base and titanium base alloys, the heat in the workpiece chip will dissolve and diffuse the components of cemented carbide into the chip, resulting in “crescent depression” on the top of the blade. The crater will eventually increase enough to cause micro collapse and deformation of the flank, and may even lead to rapid flank wear.
3. Thermomechanical Failure
Severe temperature fluctuation and mechanical shock may cause thermomechanical failure. The stress crack will form along the blade edge and eventually cause the cemented carbide part of the blade to fall off.
Thermomechanical failure is most likely to occur in milling operations, sometimes in intermittent turning, end face machining and machining operations with intermittent coolant of large quantities of parts. The sign of thermomechanical failure is the presence of multiple cracks perpendicular to the cutting edge. It is particularly important to identify this failure mode before the micro collapse begins. Thermomechanical failure can be prevented by using the coolant correctly, or if you want to completely eliminate this failure in the processing process, you can use a more impact resistant material grade, reduce the groove shape generated by heat and reduce the feed rate.
4. Edge Deformation
Excessive heat and mechanical load are the root causes of blade deformation. In the case of high speed and high feed, or when machining hard steel, work hardened zinc alloy die castings and superalloys, a large amount of heat is often generated.
Excessive heat will soften the cemented carbide adhesive or cobalt in the blade. When the stress between the blade and the workpiece causes blade deformation or tool tip depression, mechanical load will be generated, which will eventually break the blade or cause rapid flank wear.
The signs of edge deformation include the deformation of cutting edge and the machined workpiece does not meet the dimensional requirements. The edge deformation can be controlled by the following methods: rational use of coolant, use of more wear-resistant material grade with lower adhesive content, reduction of machining speed and feed rate, and use of groove type with reduced cutting force.
5. Groove Wear
When the rough surface of zinc alloy die casting is abraded and the depth of the cutting area on the cutting tool is engraved, groove wear will occur. Cast surface, oxidized surface, work hardened surface or irregular surface can cause groove wear. Although abrasive wear is the most common culprit, micro avalanches may also occur in this area. The cutting depth line of the blade is usually under tensile stress, so it is easy to be affected.
This failure mode becomes significant when groove wear and micro collapse begin to appear at the cutting depth of the blade. In order to prevent groove wear, the key is to change the cutting depth in multi stroke machining, use tools with large rake angle, increase the cutting speed and reduce the feed rate when machining superalloys, and carefully increase the grinding at the cutting depth to prevent chip deposition, especially when machining stainless steel and superalloys.
6. Mechanical Rupture
When the force on the cutting edge exceeds its inherent strength, the blade will break mechanically.
In addition to normal flank wear, mechanical fracture can be avoided by correcting all other failure modes. Using a more impact resistant material grade, selecting a stronger blade groove, using a thicker blade, reducing the feed rate and cutting depth, verifying the clamping rigidity, and checking whether the workpiece contains hard inclusions or is difficult to cut in are effective corrective measures.