Zamak 7 is a high-purity die casting zinc alloy with increased fluidity and surface finish. In this article, let’s break down this material, covering Zamak 7 composition, properties, uses, and differences between Zamak 3 and 7.
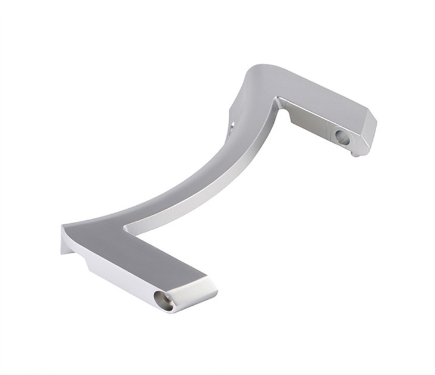
What Is Zamak 7?
Zamak 7 (ASTM AG40B, Z33523), also known as Zinc Alloy 7, is a type of zinc alloy that is commonly used in die casting. It is composed primarily of zinc with small amounts of aluminum, magnesium, and copper. Zamak 7 offers excellent castability, high strength, and good dimensional stability. It is often used in applications that require intricate shapes and thin walls, such as automotive components, electrical housings, and consumer goods.
Zamak 7 Composition
Aluminum: 3.5-4.3%
Copper: 0.25%
Iron: 0.075%
Nickel: 0.005-0.02%
Magnesium: 0.005-0.02%
Lead: 0.003%
Cadmium: 0.002%
Tin: 0.001%
Zinc: Remainder
Zamak 7 Properties
1) Physical properties:
Density: Approximately 6.7 g/cm³
Melting range: 382-390°C (719-734°F)
Thermal conductivity: Approximately 113 W/m·K
Electrical conductivity: Approximately 27% IACS (International Annealed Copper Standard)
2) Mechanical properties (values can vary depending on the specific casting process and heat treatment):
Tensile strength: Typically around 345 MPa (50,000 psi)
Yield strength: Typically around 310 MPa (45,000 psi)
Elongation: Typically around 2%
Uses and Applications of Zamak 7
Zamak 7 is commonly utilized in various applications that require the benefits of a zinc-based alloy.
– Automotive Components: Zamak 7 is used in the manufacturing of automotive components such as powertrain parts, electrical connectors, handles, brackets, and various interior and exterior trim pieces.
– Electrical Housings: It is employed in the production of electrical enclosures, switchgear components, connectors, and other electrical housing applications due to its excellent electrical conductivity and corrosion resistance.
– Consumer Goods: Zamak 7 is utilized in the production of consumer products like door handles, furniture fittings, bathroom fixtures, locks, and various decorative items.
– Industrial Equipment: It finds use in various industrial equipment applications, including pumps, valves, gears, tool parts, and fittings, where its strength, dimensional stability, and corrosion resistance are advantageous.
– Medical Devices: Zamak 7 can be found in the manufacturing of certain medical devices and equipment, where its biocompatibility with human tissue and ease of fabrication are important factors.
Differences Between Zamak 3 and Zamak 7
1. Properties:
Zamak 7 has a higher elongation at break and yield strength than Zamak 3, Alloy has a higher Knoop hardness than Alloy 7.
2. Fluidity and Castability:
Zamak 3: It has relatively lower fluidity and castability compared to Zamak 7. It may struggle with filling intricate and complex molds.
Zamak 7: It has better fluidity and castability compared to Zamak 3, making it well-suited for applications with intricate shapes and thin walls.
3. Applications:
Zamak 3: It is commonly used in general-purpose applications, such as automotive components, electrical connectors, hardware fittings, and various consumer goods.
Zamak 7: It finds application in parts where improved castability and fluidity are required, such as complicated automotive components, electrical housings, and intricate die-cast products.