Aluminium-Silicon has become a kind of alloy with the most varieties and the most widely used among the cast aluminum alloys. It is suitable for casting large, thin-walled, complex parts. What are the properties and applications of Al-Si cast alloys? Let’s see the common types and casting properties of Al-Si alloy.
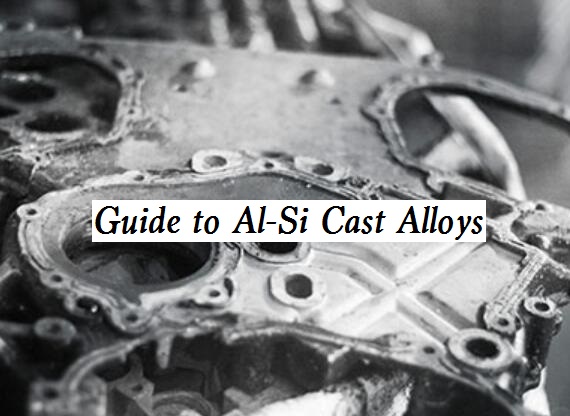
Aluminium-Silicon (Al-Si) Alloy Properties and Applications
Aluminum silicon alloy is a forging and casting alloy mainly composed of aluminum and silicon. Generally, the silicon content is 11%, and a small amount of copper, iron, and nickel are added to improve the strength. AI Si alloy is widely used in the automobile industry and machine manufacturing industry to make some parts under sliding friction conditions because of its lightweight, good thermal conductivity, certain strength, hardness, and corrosion resistance. Al Si alloy is also widely used in aviation, transportation, construction, and other important industries. It is also used to manufacture low and medium-strength castings with complex shapes, such as cover plates, motor shells, brackets, etc.
The alloy is a typical eutectic alloy with a simple phase diagram and no intermediate compounds. It has the advantages of good casting performance, high specific strength, and low price. Aluminum is the third main group element, while silicon is a semiconductor element, and the solid solubility between them is very small. When silicon content is low, Al Si alloy has good ductility and is often used as deformation alloy. When silicon content is high, Al Si alloy melt has good filling property and is often used as casting alloy.
Types of Al-Si Cast Alloys
Generally, the Si content (mass fraction) of Al Si cast alloys is 5%~25%, which can be divided into eutectic, hypereutectic, and hypoeutectic types.
– Eutectic Al-Si alloy (Si content is 10%~13%): as for the Si content of Al Si binary eutectic point, at present, many pieces of literature think that the Si content of eutectic point is 12.5%. Eutectic Al-Si alloy has excellent casting properties, but poor mechanical properties and machinability. Generally, a certain amount of Mg, Cu, and Mn are added for strengthening and toughening modification.
– Hypereutectic Al-Si alloy (Si content generally exceeds 15%): the piston of the internal combustion engine and other components requiring thermal stability at high temperature is mostly made of hypereutectic alloy. This is because the engine piston produced by hypoeutectic or eutectic Al-Si alloy will “bite the cylinder” due to the increase of temperature and volume expansion during operation, resulting in the failure of the engine to reach the rated power and reduced service life.
– Hypoeutectic Al-Si alloy (Al Si alloy except eutectic and hypereutectic): the Si content of Hypoeutectic Al Si alloy commonly used in industry is generally 6%~8%, and other strengthening elements are added for strengthening and toughening treatment. Common ones are Al Si Mg alloys and Al Si Cu alloys. Al Si Mg alloys mainly use the Mg2Si phase formed by Mg and Si as the strengthening phase, and Al Si Cu alloys mainly use Cu as the strengthening phase α- High solid solubility in al results in solution strengthening and dispersion strengthening of al2cu strengthened phase precipitated during heat treatment.
Al-Si Alloys Casting Properties
The casting performance of metal indicates the ability to obtain accurate shape and sound internal castings during the casting process. The general measurement indicators include fluidity, shrinkage, segregation tendency, etc. Al Si alloy has become the most widely used type of cast aluminum alloy precisely because its casting performance is significantly better than that of Al Cu, Al Mg, Al Zn, and other alloys.
– Fluidity: Al Si alloy has excellent fluidity, especially eutectic alloy. The thermal brittleness of the alloy decreases with the increase of alloy element content, but zinc and magnesium tend to improve the thermal brittleness. Although the alloys with eutectic composition have the best fluidity, the alloys with eutectic content between 20%~90% have the best casting performance because they have the appropriate solidification temperature width under the condition of ensuring fluidity, while the alloys with complete eutectic composition crystallize at constant temperature and tend to form shrinkage cavities.
– Shrinkage: silicon significantly reduces the solidification shrinkage of aluminum, and other alloy elements have little effect on the shrinkage. Therefore, the shrinkage of alloys containing 6%~12%si is about 3%~4%, while that of alloys containing 20%~24%si is only 1%~2%.
– Segregation tendency: most Al Si alloys have a narrow solidification range and are not easy to produce segregation, but the quenched castings have obvious surface segregation.