Final Inspection Of Mold Heat Treatment Of Aluminum Alloy Die Casting
In the mold production of aluminum alloy die casting, the quality inspection of the final heat treatment usually includes the inspection after quenching, surface quenching and tempering. Here’s everything about the final inspection of mold heat treatment of aluminum alloy die casting.
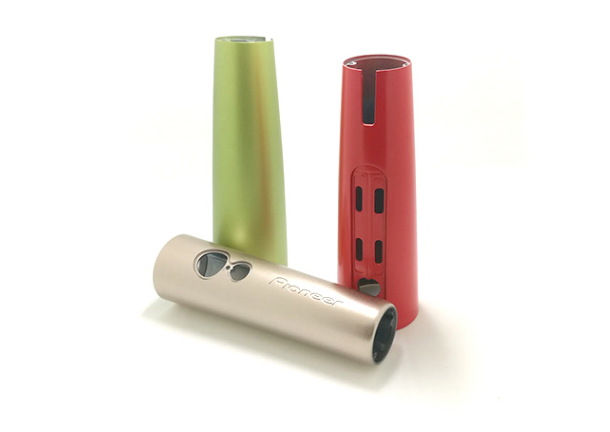
Final Inspection Of Mold Heat Treatment Of Aluminum Alloy Die Casting
1. Deformation. The quenching deformation shall be checked according to the requirements. If the deformation exceeds the regulations, it shall be straightened again. If it cannot be straightened for some reason and the deformation exceeds the machining allowance, it can be repaired. The method is to quench and temper the mold parts of aluminum alloy die casting after soft straightening to meet the requirements. Generally, the deformation of mold parts of aluminum alloy die casting after quenching and tempering shall not be greater than 2 / 3 to 1 / 2 allowance.
2. Cracking. No crack is allowed on the surface of any aluminum alloy die casting mold parts, so the heat-treated parts must be 100% inspected. The stress concentration parts, sharp corners, keyways, thin-walled holes, thickness junction, protrusion and depression, etc. should be inspected.
3. Overheating and overburning. Overheating and overburning are detected by metallographic microscope. After quenching, the mold parts of aluminum alloy die casting are not allowed to have coarse needle martensite overheating structure and grain boundary oxidation overburning structure, because overheating and overburning will reduce strength and increase brittleness, which is very easy to crack.
4. Oxidation and decarburization. The oxidation and decarburization of aluminum alloy die casting mold parts with small machining allowance should be controlled strictly. Decarburization is not allowed for cutting tools and abrasives. When serious oxidation and decarburization are found in quenched parts, the heating temperature must be too high or the holding time must be too long, so overheating inspection must be carried out at the same time.
5. Be soft. Soft spots will cause wear and fatigue damage of mold parts of aluminum alloy die casting, so there shall be no soft spots. The causes are mostly improper heating and cooling, uneven structure of raw materials, banded structure and residual decarburization layer, etc. when soft spots appear, they shall be repaired in time.
6. Insufficient hardness. Generally, when quenching mold parts of aluminum alloy die casting, the heating temperature is too high, too much residual austenite will cause the reduction of hardness, low heating temperature or insufficient holding time, insufficient quenching cooling speed and improper operation will cause the lack of quenching hardness. The above conditions can only be repaired.
7. Salt bath furnace. High and medium frequency and flame Quenched Aluminum alloy die casting mold parts shall not be burned.
After the final heat treatment, the surface of aluminum alloy die casting mold parts shall be free of corrosion, bump, shrinkage, damage and other defects.