The speed of die casting has a great influence on forming. Poor speed control will cause many defects in die castings. The casting speed has two aspects, one is the injection speed and the other is the filling speed. Next, let’s see the difference between filling velocity and injection velocity and how to determine the injection speed.
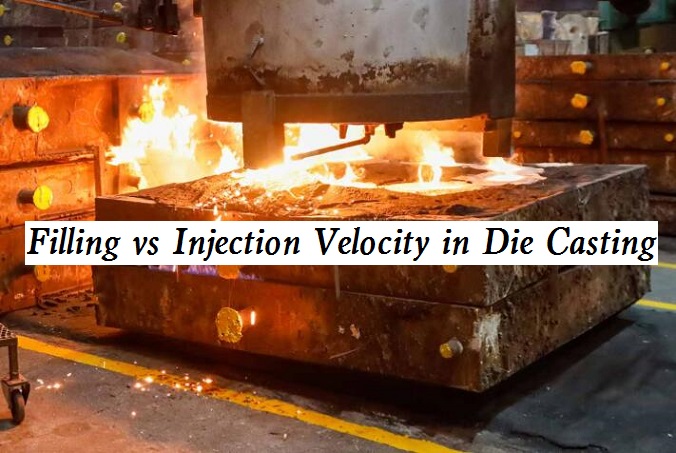
What is Injection Speed in Die Casting?
Injection speed refers to the linear speed of the injection punch driven by the pressure oil in the injection cylinder of the die casting machine. It is the flowing speed of molten metal pushed by the injection punch in the pressure chamber. When the molten metal is poured into the pressure chamber, the filling degree of the molten metal in the pressure chamber is generally about 45% ~ 70%, and the rest of the space is filled with air. The purpose of the low-speed injection is to make the liquid metal flow smoothly and the air can be discharged smoothly. When the liquid metal reaches the inner gate, it can be switched at high speed to make the liquid metal fill under high pressure and high speed. One of the basic characteristics of die casting is rapid filling. In the whole rapid injection stage, the metal liquid enters the mold cavity in the form of the jet at the speed of 30 ~ 60 m/s, and the metal liquid will wrap the gas. In this case, it can be considered where the pores are distributed without affecting the key parts. Because the cross-sectional area of the cavity at the forming part is much larger than the cross-sectional area of the inner gate, when the moving speed of the injection punch is not greater than 0.8 m/s, the liquid metal flows in the cavity in a manner similar to laminar flow, and there will be no entrainment at this stage. Starting from the quick point until the end of filling Liquid metal moves in the form of a jet. This stage is not only the process of wrapping gas but also the part where pores are easy to occur in castings.
What is Filling Velocity in Die Casting?
Filling velocity refers to the linear speed of liquid metal entering the cavity through the gate under pressure. The main function of mold filling velocity is to quickly feed liquid metal into the mold cavity before solidification. It is an important factor to obtain castings with clear contour and high surface quality. The filling speed of liquid metal into the cavity is high. It is beneficial to obtain castings with clear contour and good surface quality. But the disadvantage is that it is easy to cause poor exhaust and great scouring to the mold.
How to Determine Injection Speed?
In addition to the appropriate injection-specific pressure, the speed of the low-pressure die must be selected correctly. The filling rate is determined according to the characteristics of the alloy and the structural characteristics of the casting. When the filling speed is low, the contour of the casting is unclear or even can not be formed. When the filling speed is high, castings with high surface quality can be obtained even with low injection-specific pressure. However, too high mold filling speed will cause many technical defects.
The main factors that affect die casting injection speed are as follows:
1. As the high-speed molten metal flows in front of the air, the low-pressure die blocks the exhaust channel, and the air wraps in the cavity to form bubbles.
2. The molten metal is atomized into the mold cavity and adhered to the mold wall so that the molten metal can not fuse with the molten metal to form surface defects (cold beans or cold insulation), so as to reduce the surface quality of the casting.
3. The high-speed metal flow generates eddy current, which first wraps the air and cold metal entering the mold cavity, resulting in pores and oxide inclusions in the casting.
4. High-speed metal flow washes the die wall and accelerates the wear of die casting mold.
5. When the mold temperature is low, the speed can be low, on the contrary, the speed can be high.
6. Complex castings use high-pressure velocity.
Injection velocity is divided into slow injection velocity and fast injection velocity. Generally speaking, the injection velocity refers to fast injection velocity. The slow injection speed is generally 0.1 ~ 0.5m/s, and the fast injection speed of aluminum alloy is generally 0.1 ~ 1.1m/s. The thinner the wall thickness of the casting, the faster the injection speed is required, the more complex the shape of the casting, the faster the injection speed is required, the larger the projection surface of the casting, the faster the injection speed is required, and the longer the ballast path of the casting, the faster the injection speed is required.