Filling Time Of Zinc Alloy Die Casting Process & Temperature Control of Die Casting Mold
When producing high-quality zinc alloy parts, precise control of the die casting surface temperature is critical. In this guide, we talk about the filling time of zinc alloy die casting process and temperature control of die casting mold.
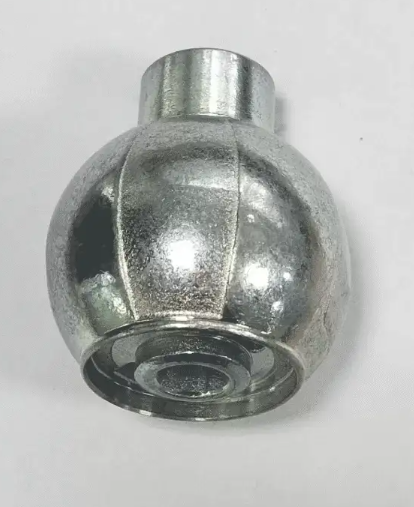
Filling Time Of Zinc Alloy Die Casting Process & Temperature Control of Die Casting Mold
1. Filling Time
T= (q/v charging Ag)
Where, it is the filling time (s), q is the metal volume (M3), V, Ag is the filling speed (m/s), and Ag is the sectional area of the inner gate (cm2).
In die casting production, liquid metal is required to fill the mold cavity as soon as possible to obtain clear contour and good surface quality. According to the characteristics of zinc alloy die casting workpiece, the filling time is within 6~40 ms. If it is a mechanical workpiece or requires electroplating, the filling time is less than 20 ms, and the workpiece to be painted is less than 40 ms.
2. Pressure maintaining time
When the metal liquid fills the mold cavity, the injection cylinder shall continue to work, so that the punch continues to exert pressure on the metal, so that the metal liquid crystallizes under pressure, and the volume shrinkage of the die casting during solidification is continuously compensated by the liquid, so as to finally obtain a casting with dense structure. The holding time depends on the wall thickness of the casting and the solidification time at the inner gate, and one strand is greater than 0.5 s. If many voids and cavities are found in the center of nozzle material, it indicates that the pressure maintaining time is not enough and the hammer return is too early. If there are voids and cavities at the wall thickness of the casting or near the inner gate, the pressure holding pressure may be too low. When the holding time is not enough, the surface of the pressed castings is often not beautiful, and the machine process parameters need to be adjusted.
3. Mold retention time
Once the injection is completed, the molten metal in the mold cavity begins to solidify. When the casting is taken out, it must wait until the casting temperature is reduced to a certain degree and has a certain mechanical strength, so that the ejection can not be deformed and damaged. The mold retention time refers to the time from the end of the pressure holding time to the opening and ejection of the casting. If the mold retention time is too long, the mold holding force formed due to the solidification shrinkage force will increase, resulting in difficulties in core pulling and ejection, which is easy to cause cracking of castings; If the ejection time is too short, the castings are easy to deform, crack and blister on the surface; Generally, within 5~10 s, it depends on the size, wall thickness, shape and mold temperature of the casting. It can also be judged whether the die-casting is deformed to determine whether the mold retention time is appropriate.
4. Mold temperature
Die casting mold temperature is an important parameter affecting the quality of die castings. In a die casting cycle, the mold temperature changes.
Die temperature range of die casting mold: 160 – 220 ℃
Castings to be electroplated: 180 – 220 ℃
The mold temperature is too low, and the liquid metal solidifies too early in the process of filling the mold cavity, which is easy to cause defects such as surface return cold lines and flow marks. If the mold temperature is too high, it is easy to stick the mold, and local workpieces are welded with the mold. High mold temperature will make the casting cool slowly and the grain is coarse, which is easy to produce shrinkage and porosity, resulting in the reduction of mechanical properties.
Mold temperature directly affects the spraying effect of coating.
Mold temperature is directly related to casting cycle and cooling water volume. The temperature balance of die-casting mold is controlled by setting cooling water circuit and adjusting cooling water volume.
During the production process, attention should be paid to keeping the die casting cycle consistent so as to stabilize the mold temperature of the die casting mold.