At present, the casting level of aluminum ingots is relatively high, which improves the stability of aluminum ingot performance and makes it more widely used. The characteristics of die-casting aluminum ingots meet the requirements of the die-casting process. Moreover, the use of advanced equipment has improved the quality and output. Today, the price of aluminum ingots has increased and is applied in automobiles, machinery, and other industries. The manufacturer pays attention to the improvement of equipment to promote the quality level of the die-casting aluminum ingot.
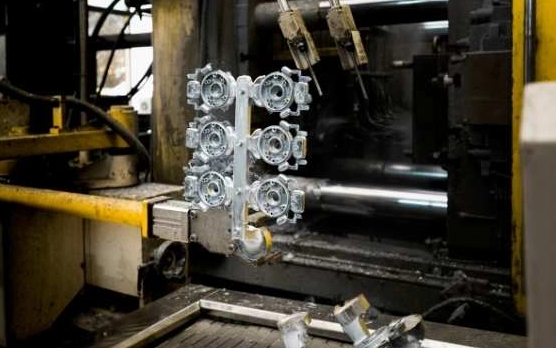
1. To improve the stability of the chain, the frequency conversion speed regulation device is adopted to make the transmission system more efficient. At the same time, the price of lifting ZL102 aluminum ingot is high, the speed rigidity of the motor is high, and crawling and other phenomena are avoided. The chain runs more stably and the vibration is relatively small, so as to reduce the impact on the aluminum ingot.
2. Pay attention to the improvement of the cooling effect. By improving the structure of the cooling water pan, speed up the cooling speed of aluminum liquid, widen the water tank, speed up the circulation speed of cooling water, making the cooling effect more obvious and saving time.
3. Pay attention to improving the accuracy of a sprocket.
Market of aluminum die casting
Aluminum die casting production process, first addition molding, rolling, and surface treatment. Aluminum dies casting with better quality seems to usher in the so-called peak season of die casting industry in August and September. At present, the survival situation of die-casting aluminum alloy ingot production enterprises is not optimistic. Recently, a random survey of 20 die-casting aluminum alloy ingot production enterprises shows that in fact, the situation is not optimistic. Aluminum die casting with good quality accounts for about half of the die-casting aluminum alloy ingot enterprises, and the operating rate of the higher industry is only about 80%. At the same time, most die-casting aluminum alloy ingot manufacturers ADC12 offer about 16100-16400 / ton, and due to the large capital gap of downstream die-casting enterprises, the accounting period is generally long, while the trading volume of cash and spot transactions is generally, and the stainless steel modeling ceiling is not ideal; In addition, due to the continued weakness of downstream demand and fierce market competition, prices continued to decline.
All aspects of die casting equipment: in recent years, customers choose aluminum alloy very strictly. Aluminum is also their dependence, which is needed by every household. The die cast aluminum display screen is mainly used for dynamic display and composition of colorful background to enrich and increase stage elements. The newer die-casting aluminum display screen is not only a simple upgrade of the traditional display box but also an integrated optimization and update in terms of structure and performance. It is a compact indoor rental display screen made of high splicing precision and convenient disassembly, assembly, and maintenance.
When the speed of die-casting aluminum is increased, the high level and temperature gradient of die-casting ingot liquid cavity are increased, there will be a liquid cavity section that cannot be fed at the bottom of the liquid cavity center, resulting in very large shrinkage stress, and the hot cracking tendency of die-casting aluminum ingot will increase. Die casting aluminum display screen adopts one-time molding die, which ensures the flatness of the box, effectively controls the tolerance range and basically solves the problem of box splicing; Humanized design, more convenient and lightweight installation, and the box is easy to assemble. As well as in the modern office, furniture aluminum accessories are indispensable. The characteristics of various forms and novel styles of aluminum profiles have been widely favored by the public. Do you know about aluminum profiles?
Advantages and disadvantages of aluminum materials
There are two kinds of aluminum materials: large diameter aluminum pipe and alloy aluminum pipe. It is mainly made of aluminum ingots with a purity of more than 92% of the extruded water of aluminum profiles and then added with metal elements that can increase the hardness, strength, wear-resistance, and other properties, such as silicon, magnesium, carbon, sulfur, etc., which are later manufactured into “alloy” by the process. The raw materials of die-casting alloy are aluminum ingots and alloy materials with a purity of about 92%, which are melted in the furnace and molded in the die-casting machine. Advantages: high strength, high hardness, easy fabrication, and convenient connection. Die casting aluminum office furniture aluminum profile factory extrusion director shape can be designed like toys, novel style, convenient for connection in various directions; The hardness and strength are higher and the safety is more guaranteed.
Die casting process
The die casting process adopts the process method of high-speed injection of molten aluminum into the die casting die and pressure maintaining cooling forming. It has the advantages of high production efficiency, low cost, good surface quality, and high dimensional accuracy. The disadvantages are also obvious: the mold cost is high, the density is not high, and shrinkage porosity is easy to occur inside, Moreover, there are many internal pores and slag holes (because the aluminum liquid is wrapped with a large amount of air to form pores and slag holes when it is injected at high speed), and the mechanical strength and elongation are low (this is because the die castings cannot be subjected to T6 heat treatment to increase the strength.
The reason why T6 heat treatment cannot be performed is that there are a large number of pores inside. The low elongation is because the iron content of the die-casting aluminum alloy is too high, and the higher the iron content, the lower the elongation). The airtightness is poor. The die castings often need to be vacuum sealed to block the shrinkage and porosity of the castings. In addition, the production of some inner cavities is complex Products, such as teapots with small mouths and large stomachs. The gravity casting process adopts dissolved and customized aluminum tapping oil, which can solve the problem of copper-aluminum alloy/aluminum tapping teeth stained with debris and rotten teeth.
Customer a: I’m an aluminum alloy tapping. Why do I always get scraps? Customer B: I attack teeth with copper and aluminum. There will be a problem with rotten teeth. How can I solve it? Similar to the above problems, customers of aluminum tapping and die-casting aluminum tapping still encounter more. When they use extrusion tapping or cutting tapping, what are the reasons for these problems? The hardness and melting point of the above materials are very low.
When the tooth hole temperature rises slightly, generally at 50-80 degrees, the material softens and approaches the melting point. When tapping with extrusion wire, due to the large torque and friction (the torque is four times that of cutting), a lot of heat energy will be generated, and the temperature in the hole rises, which is easy to reach the melting point of aluminum alloy… And other materials. At this time, The thread extruded by the tap is due to the increase of temperature.
All aspects of die casting equipment: in practical application, many people know that radiators are useful. Do you know how to distinguish between die casting radiators and profile radiators? We explain it in three points as follows:
1. The profile radiator is extruded, so the structure of any section in the tensile direction is the same;
2. Profiles generally have right angles and sharp edges; Die-castings do not,
3. Die-casting radiator has an obvious draft angle.
4. What are the advantages of an aluminum profile radiator compared with the die-casting radiator?
5. In the extrusion process of the aluminum profile radiator, the extruded aluminum can obtain a more intense and uniform three-dimensional compressive stress state in the deformation zone than rolling and forging, which can give full play to the plasticity of the processed aluminum.
6. The surface treatment of aluminum profile in electroplating and anodizing is easier, and the die casting is relatively difficult.
7. Aluminum profile radiator has a high aging rate, low defect rate, and lower cost in mass production. And aluminum die-casting plate automatic sandblasting machine. The company has always been committed to adopting new materials and new processes to improve the quality of our cleaning equipment.