Zinc alloy die castings are mainly composed of zinc and supplemented by aluminum. Its chemical stability is poor, so it needs to be protected by other metal layers, including the electroplating layer. The pretreatment is very important for the following electroplating, so in this article, follow us to learn about everything to notice for pre-plating of die casting zinc alloy and the process to do it.
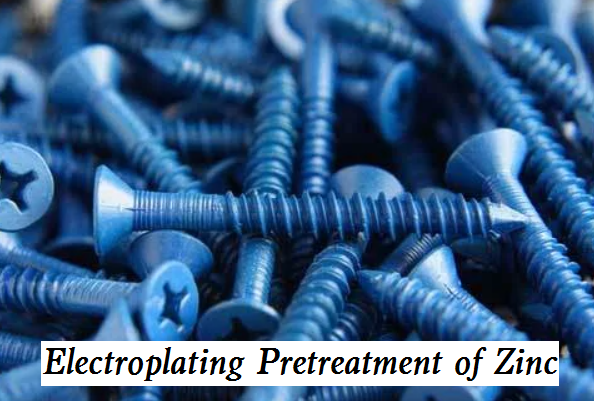
Tips for Electroplating Pretreatment of Zinc Alloy Die Castings
The ratio of zinc to aluminum content of zinc alloy die castings shall be understood before electroplating. If the aluminum content is too high, the oxidation of the surface layer will be accelerated, resulting in a decrease in the coating adhesion. If the aluminum content is too low, the toughness of the parts will be affected, and the parts are prone to fracture during use. However, in the process of pretreatment, the pretreatment is often equated with the pretreatment of other metal materials, or one of the processes is ignored, resulting in a large number of reworking or scrapping of plated parts. Due to the particularity of zinc alloy die castings, it is difficult to rework, which is the reason for the high scrap rate of zinc alloy die castings in the electroplating process.
1) Understand the characteristics of zinc alloy die castings
The surface of zinc alloy die castings is very similar to that of steamed buns. There is a smooth and dense metal layer with a thickness of 0.02~0.10 um. Below it is a loose and porous structure. Therefore, during mechanical polishing, it is strictly prohibited to polish through its smooth and dense layer to avoid the exposure of loose and porous internal materials, which may lead to blistering, peeling, and other undesirable phenomena of the coating.
2) Know about the chemical properties of zinc alloy die castings
In the process of die casting, the influence of technological factors will cause the zinc-rich and aluminum-rich parts in the same zinc alloy die casting part. Strong base preferentially dissolves the aluminum-rich phase, and strong acid preferentially dissolves the zinc-rich phase. If strong alkali or acid is used during degreasing or etching, the coating will blister and peel during electroplating, seriously affecting the yield. Therefore, zinc alloy die castings should not be degreased and etched in strong acid or alkali.
3) Meet the size requirements of zinc alloy die casting pre-coating
The zinc alloy die castings shall be pre-plated with the primer after the pre-plating treatment. Generally, copper is plated in a cyanide copper plating bath without NaOH, or nickel is plated in a neutral nickel plating solution. Tubular parts shall be deposited in a pyrophosphate bath. The thinner the copper layer is, the faster the copper diffuses into the zinc alloy.
4) Do not leave the parts in the bath or atmosphere for a long time
The pre-plating treatment of zinc alloy die castings is to remove the oil stain on the surface of the parts and the oxide film formed by oxygen oxidation of the parts after they have been in the air for a long time so that the metal ions in the plating solution can be directly deposited on the pure surface. After the pretreatment, the parts should be put into the bath for electroplating immediately. It is not allowed to stay in the atmosphere or in the bath for a long time to prevent the surface from being oxidized again or forming hydrates on the surface, which will affect the adhesion of the coating.
Electroplating Pretreatment Process of Zinc Alloy Die Castings
1) Mechanical polishing
Polishing is to use a polishing wheel and polishing paste to slightly cut and grind the surface of parts to level the surface of parts and improve the surface finish. For zinc alloy die castings, the linear speed of the polishing wheel is generally 20~25 m/s. The polishing wheel should be oiled frequently and less, and the red polishing paste should be used first, then the white polishing paste. Polishing is generally manual operation, the application force of both hands is uniform, and the force should not be too large, not to mention the cutting point of the polishing wheel should not stay on a certain part, in order to prevent polishing through the smooth and dense outer surface layer of zinc alloy die castings, thus affecting the electroplating quality.
2) Degreasing
The forming of zinc alloy die castings depends on the mold, and the mold should be regularly coated with mineral oil and other mold-protecting agents during the die casting process. The parts will also be stained with a little grease in the process of discharge and operation after die casting. These greases should be cleaned before plating, otherwise, the adhesion between the coating and the substrate will be affected. In the zinc alloy degreasing solution, strong alkaline chemical raw materials cannot be added for convenience, and only weak alkaline compounds can be used for degreasing under certain conditions. In order to completely remove oil and prevent greasy residues in deep recesses of complex parts, electrochemical degreasing can be used to improve the degreasing effect of deep recesses, thus making up for the shortcomings of chemical degreasing. Table l lists several formulas and process specifications applicable to chemical and electrochemical degreasing of zinc alloy die castings.
3) Etching
After the chemical and electrochemical degreasing of zinc alloy parts in the degreasing solution, the oil stain on the surface has been removed, but there is still a slight oxide film produced at the source, which will affect the adhesion between the coating and zinc alloy. Although strong acid can easily remove oxide film, due to the characteristics of zinc alloy, it is not suitable for use, and only a very thin weak acid can be used for etching. The etching time shall be determined by visual inspection: when the parts are immersed in the etching solution, the reaction of the parts in the solution shall be observed by visual inspection. Once there are tiny bubbles on the surface of the parts, the parts shall be taken out immediately, and the next process shall be started as soon as possible after cleaning.
4) One-step degreasing and etching
Immerse the zinc alloy parts in concentrated H2SO4 for a moment, and then immediately transfer them to the cleaning tank for cleaning after taking them out, and then remove the gray-black powder film in the stripping solution. This is a one-step method. It is well known that pure H2SO4 molecules cannot ionize hydrogen atoms to react with zinc alloy under anhydrous conditions. This is why concentrated sulfuric acid can be transported in iron drums. Therefore, the parts are not allowed to enter the concentrated H2SO4 with water. However, concentrated H2SO4 has strong oxidation, dehydration, carbonization, and other characteristics, so it can remove oil stains and organic impurities on the surface of parts to achieve the oil removal function. When the part leaves the concentrated H2SO4 and enters the cleaning tank, a small amount of concentrated H2SO4 remaining on the part surface will immediately ionize out of H and react with the zinc alloy surface, and the original mild oxide film on the zinc alloy surface will be etched by dilute H2SO4, thus realizing the one-step completion of oil removal and etching.
5) Remove the gray-black powder film
There is a slight gray-black powder film formed after H2SO4 oxidation and carbonization on the part surface after one-step degreasing etching, which shall be removed in the stripping solution. Antidye s in the stripping solution has an adsorption function, which can adsorb the gray-black powder film on the surface of the part, making the zinc alloy surface appear pure zinc alloy. NaCN in the stripping solution plays an active role on the surface of zinc alloy, while trace HNO3 can make the anti-dye function continuously.
Preplating
Before nickel plating or acid-bright copper plating on zinc alloy, a layer of pre-coating shall be deposited in the plating solution with low corrosivity and strong covering ability. For example, a layer of copper is deposited in a cyanide copper plating bath without NaOH, or a layer of nickel is deposited in a neutral nickel plating bath. Tubular work shall be deposited in a pyrophosphate bath. The thickness of the deposited layer shall not be less than 6 pm, otherwise, when the part is transferred to the highly acidic plating bath, due to the complex geometry of the part, local corrosion will occur at the part where the current enters a small amount at the moment of power on, resulting in scrapping of the plated part. After pre-plating, other metal layers can be plated according to customer requirements. Because the unit price of the nickel plating plate is too high, it is unnecessary to use it as pre-coating.