Effective Measures To Improve The Corrosion Resistance Of Magnesium Alloy
Magnesium alloy die casting has broad application prospects and extremely important economic value in the fields of automobile, electronics, electrical appliances, transportation, aerospace, aviation, national defense and military. However, the electrode potential of magnesium alloy is very negative (- 2.34v), and the oxide film of magnesium alloy is usually porous and porous, with high chemical and electrochemical activity, so its chemical stability is low and its corrosion resistance is poor. In addition, magnesium alloy has low hardness and poor wear resistance. These defects also limit the wide application of magnesium alloys to a certain extent. Widely used. Therefore, how to effectively improve the wear resistance and corrosion resistance of magnesium alloys from the perspective of industrial application has become a key technical problem to be solved in the development and research of magnesium alloys. Read this article to understand the effective measures to improve the corrosion resistance of magnesium alloys.
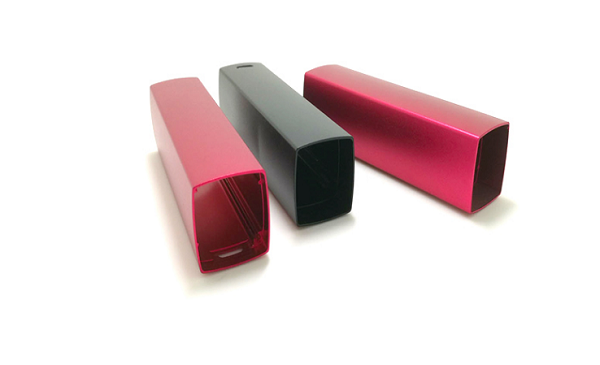
Effective Measures To Improve The Corrosion Resistance Of Magnesium Alloy
Aluminum based amorphous nanocrystalline composite protective coating was prepared on the surface of magnesium alloy in the Engineering College of armored forces by high-speed arc spraying technology, and good results were obtained. High speed arc spraying technology has the characteristics of high quality, high efficiency, low cost, large spraying area and industrial application. It has become one of the important surface protection methods for the preparation of anti-corrosion and wear-resistant coatings. In the process of high-speed arc spraying, the cooling rate of melt sprayed particles is very fast, and it is easy to obtain amorphous nanocrystalline composite coating with high deposition efficiency and low cost. Therefore, the preparation of nanocrystalline composite protective coating on the surface of magnesium alloy by high-speed arc spraying technology has important theoretical significance and application value for solving the problem of corrosion and wear resistance on the surface of magnesium alloy.
Al-Ni-Y-Co composite coating was successfully prepared by automatic high-speed arc spraying technology. The structure of each area of the coating is uniform and compact, showing typical layered structure characteristics. There are no cracks between layers, and there are no obvious pores and cracks in the joint. The main bonding mode between coating and substrate is mechanical bonding, but micro metallurgical bonding also plays a certain role. The porosity is about 1.8%, the bonding strength is 26.8mpa, and the average microhardness is 311.7hv, which is five times that of AZ91 magnesium alloy. The coating is composed of amorphous nanocrystalline phase with dispersion size of 10 ~ 80 nm and a small amount of microcrystalline structure.
The results show that the wear resistance of Al-Ni-Y-Co amorphous nanocrystalline composite coating is 6 times higher than that of AZ91 magnesium alloy, and the wear rate is low. This is because the amorphous phase of the coating is α- A1 equivalent nanoparticle dispersion. These nanoparticles can play the role of dispersion strengthening to a certain extent, prevent the propagation of cracks in the wear process, and make the aluminum based amorphous nanocrystalline composite coating have good wear resistance.
The corrosion test results in 5% NaCI aqueous solution show that the corrosion resistance of Al-Ni-Y-Co amorphous nanocrystalline composite coating is significantly better than that of AZ91 magnesium alloy. The self-corrosion potential of AZ91 magnesium alloy is significantly higher than that of AZ91 magnesium alloy, and the self-corrosion current density is about 1 / 5 of that of AZ91 magnesium alloy. Compared with AZ91 magnesium alloy, the surface morphology after corrosion is smoother and the pitting corrosion is smaller. Magnesium alloy has strong oxidation activity and is easy to oxidize. An oxide film is formed on the surface of magnesium alloy. However, the resistance of this oxide film to chloride ion erosion is very weak and vulnerable to damage. There are amorphous phase, nanocrystalline phase and microcrystalline phase in Al-Ni-Y-Co coating, and there are dispersed nanocrystalline phase on amorphous matrix. The amorphous phase has no grain boundaries and defects and has good corrosion resistance. The existence of nanocrystalline phase can promote the formation of passive film and prevent further corrosion. The oxide film formed by droplets and the composite structure alternately form Al-Ni-Y-Co composite coating, which makes magnesium alloy die castings have excellent corrosion resistance.