A foundry furnace, also kown as casting furnace, is a melting device used to melt different types metals, here we’ll walk you though different types of furnaces in foundry and what are they used for, as well as how does a foundry furnace work.
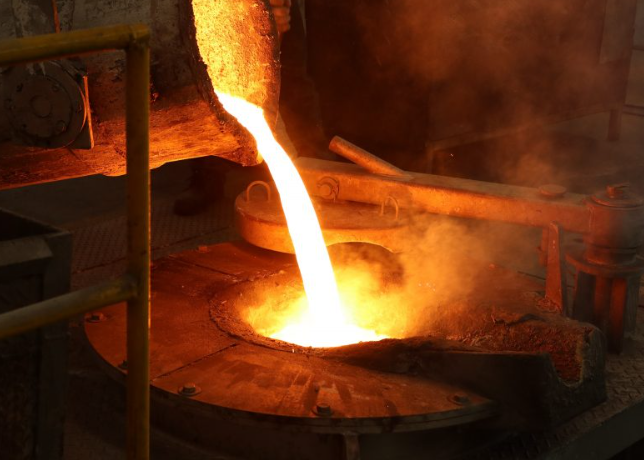
Different Types of Furnaces in Foundry and Their Uses
A furnace in the foundry is a specialized device used to melt and refine metal for casting. Foundry furnaces are typically designed to withstand high temperatures and can be fueled by a variety of sources, including natural gas, propane, and electricity. The furnace is loaded with metal scrap and other raw materials, which are then heated to a high temperature to melt the metal. Depending on the specific application, the metal is then refined by adding various chemical agents and using different refining techniques to achieve the desired metal composition and purity. Once the metal has been melted and refined, it can be poured into molds to create castings of the desired shape and size. Foundry furnaces can range in size from small, tabletop models to large, industrial-scale furnaces capable of melting and refining large quantities of metal. Foundries use several types of furnaces to melt different types of metals.
1. Cupola Furnace: This furnace is used for melting cast iron. It is a vertical furnace that is made of steel with a brick lining. Coke is used as fuel and air is blown into the furnace to create temperatures upwards of 2,800 degrees Fahrenheit. The metal is then melted and dropped out of the bottom of the cupola into a ladle.
2. Electric Arc Furnace (EAF): This furnace is used for melting steel and other types of alloys. It uses electricity to generate heat and can reach temperatures up to 3,600 degrees Fahrenheit. The furnace is made of refractory materials and contains a charging bucket for the metal scrap. Large graphite electrodes are used to create an electrical arc that melts the metal.
3. Induction Furnace: This furnace uses electromagnetic induction to heat and melt metals such as iron, brass, and aluminum. A crucible made of refractory material holds the metal and is placed inside a coil. An electrical current is passed through the coil, creating a magnetic field that induces electrical currents in the metal, causing it to heat and melt.
4. Crucible Furnace: This is a small and portable furnace used to melt small amounts of metal. It is made of clay graphite and is heated using gas, oil, or electricity. It is particularly useful for small-scale operations such as jewelry making, craftwork, and repair work.
5. Shaft Furnace: A furnace that uses natural gas or other fuel to create temperatures above 2,000 degrees Fahrenheit. It is used to smelt metals such as aluminum and zinc.
Differences between electric furnaces and induction furnaces
1. Heating method: Electric furnaces use electrical resistance (i.e., an electric current passing through a resistive material) to generate heat, while induction furnaces use electromagnetic induction to generate heat.
2. Energy efficiency: Induction furnaces are generally more energy efficient than electric furnaces, as they have a higher heating rate and a shorter heating cycle. This means that they use less energy overall to achieve the same melting results.
3. Melting speed: Induction furnaces have a faster melting speed than electric furnaces, as the electromagnetic field can induce heat directly into the metal charge, whereas with electric furnaces, the heat must first be conducted through the refractory lining and then to the metal charge.
4. Operational costs: Induction furnaces have a higher upfront cost than electric furnaces, but they require less maintenance and have lower operational costs due to their higher energy efficiency and faster melting speed.
5. Melting capacity: Induction furnaces generally have a smaller capacity than electric furnaces, making them more suitable for small-scale foundries or for melting specific alloy grades. Electric furnaces can be designed to melt larger quantities of metal in a single cycle.
Advantage of induction furnace over electric arc furnace
The primary advantage of an induction furnace over an electric arc furnace is its higher energy efficiency and faster heating rate. This is because induction furnaces use electromagnetic induction to generate heat directly within the metal charge, whereas electric arc furnaces rely on an electric arc to heat the metal. The use of electromagnetic induction allows for a more precise and localized heating process, which reduces energy waste and enables faster melting times. Additionally, induction furnaces have a lower electrode consumption, produce fewer emissions, and generally require less maintenance than electric arc furnaces. However, electric arc furnaces have a larger melting capacity than induction furnaces, making them more suitable for large-scale foundries or for melting certain types of metals.
How Does a Foundry Furnace Work?
A foundry furnace works by using heat to melt and refine metals. The furnace is typically loaded with metal scrap and other raw materials, which are then heated to a high temperature using fuel sources such as natural gas, propane, or electricity. As the metal begins to melt, it is carefully impurified and refined by adding various chemical agents and using various refining techniques. Once the metal has reached the desired purity and viscosity, it can be poured into molds to create castings of the desired shape and size. The furnace is then allowed to cool down before the finished castings can be removed.