When selecting the casting technologies for aluminum alloys, the wall thickness of the workpiece is an important factor. What are the common types of aluminum casting processes? Let’s look into the three main aluminum casting methods in this article.
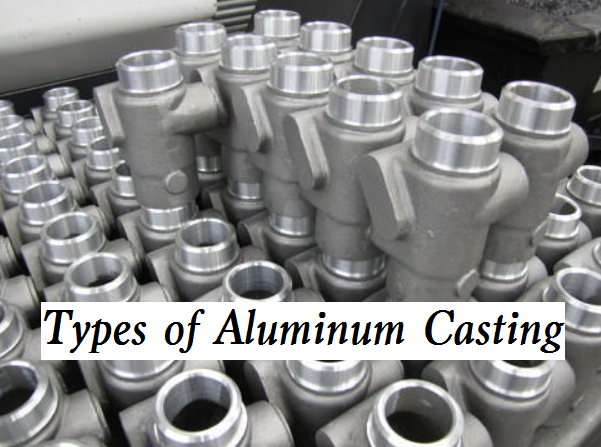
Different Types of Aluminum Casting Processes - Which Aluminum Casting Method to Choose
Pressure casting is divided into high-pressure casting and low-pressure casting. When the thickness of the casting part is great than 8mm, die casting may cause lots of pores in the product, so gravity casting is often used at this time.
1. Aluminum Gravity Casting
Gravity casting is the method of putting aluminum liquid into a casting mold using gravity. Gravity casting is classified in broad terms as sand casting, metal mold casting, lost foam casting, and so on; gravity casting is defined in a more restricted sense as metal casting. Gravity casting, in the narrowest sense, pertains only to metal casting. Metal type casting is classified as vertical hand casting or tilting casting. Tilting casting is presently the most widely used method of metal mold casting. The mold is built of heat-resistant alloy steel, and the cast aluminum casting has greater strength, size, and look than other casting techniques. Gravity casting aluminum liquid is typically poured into the gate by hand, relying on the metal liquid’s self-weight to fill the cavity, exhaust, cool, and open the mold to obtain a sample, and its process flow is generally as follows: aluminum liquid melting, pouring, filling, exhausting, cooling, opening the mold, clearing the production, heat treatment, and processing.
Characteristics of aluminum alloy gravity casting parts:
– The surface finish of the product is not high, and craters are easily produced after shot blasting
– Aluminum casting internal poreless, can be heat treatment
– Low denseness and slightly poor strength, but high elongation
– Lower mold cost and long mold life
– Low production efficiency, thus increasing the production cost
– The process is simpler and not suitable for producing thin-walled parts
– Low fluidity special aluminum alloy can be used
2. High-Pressure Aluminum Casting
High-pressure aluminum casting is what we usually call aluminum die casting, in which aluminum liquid is poured into the press chamber and filled with the mold cavity at high speed through its pressure, and the liquid solidifies under pressure to form aluminum casting. A casting method in which a liquid or semi-solid metal or alloy, or liquid metal or alloy containing an enhanced phase, is filled into the cavity of a die-casting mold at a high rate under high pressure, and the metal or alloy is solidified under pressure to form a casting. Die-casting commonly used pressure for 4 ~ 500MPa, metal filling speed for 0.5-120m/s. Therefore, the metal liquid filling time is very short, about 0.01-0.2 seconds (depending on the size of the casting and difference) can fill the cavity. Therefore, high pressure, high speed is the fundamental difference between the die-casting method and other casting methods, is also an important feature.
Characteristics of aluminum alloy die casting:
– The product surface finish is good, generally up to Ra6.3 or even up to Ra1.6
– Not heat treatment
– Product airtightness, casting strength, and surface hardness, but low elongation, wall thickness is too thick and easy to produce porosity
– High mold cost and short service life
– High production efficiency
– It can produce thin-walled parts with a small machining allowance
– It is impossible to use special aluminum alloy
3. Low-Pressure Aluminum Casting
In the sealed crucible (or sealed tank), dry compressed air is introduced, and the metal liquid, under the action of gas pressure, rises along the rising tube into the straight sprue and enters the cavity smoothly through the inner sprue, and maintains the gas pressure on the liquid surface inside the crucible. Until the casting is completely solidified. Then the gas pressure on the liquid surface is released and the unconsolidated metal in the riser flows back to the crucible. The casting is then opened and removed. This casting method has good shrinkage, dense castings, easy to cast large thin-walled complex castings, no bubble, a metal yield of 95%. No pollution, easy to achieve automation. However, the equipment cost is high and the production efficiency is low. Generally used for casting non-ferrous alloys.
Characteristics of low-pressure aluminum casting:
– The surface of the product than die casting is poorly stronger than gravity parts
– Aluminum castings with fewer internal pores, can be heat-treated
– Product airtightness, casting strength, and surface hardness are higher than die casting, but the elongation is lower than gravity casting.
– Mold cost is lower and the service life is lower
– Production efficiency is lower than gravity and much lower than die-casting
– The process is complex and used to produce high requirements and high-quality castings
– Low fluidity special aluminum alloy can be used